Устойчивые ПЭТ-преформы
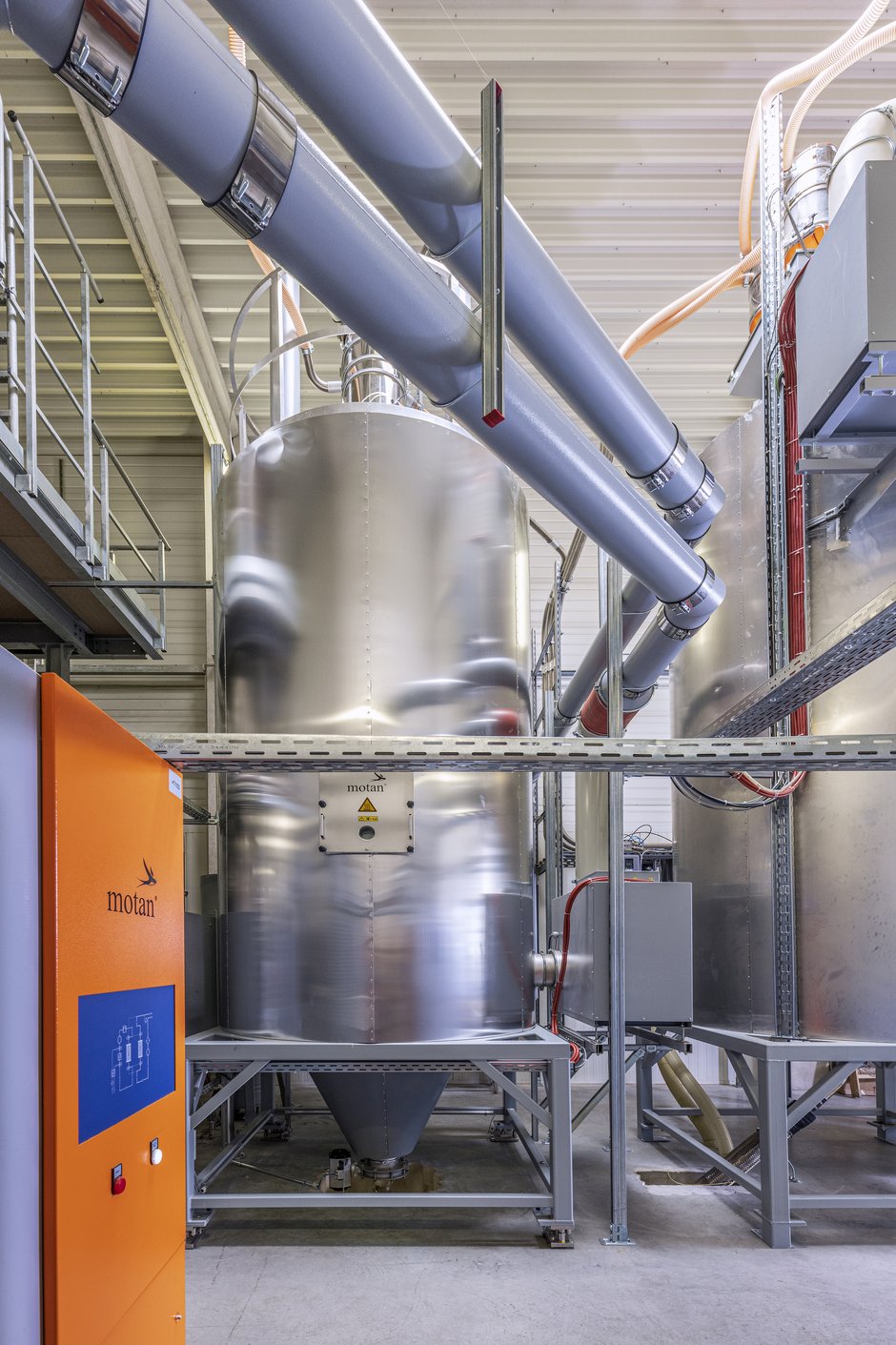
Повторное использование при дефиците сырья
Для других заводов в группе преформы изготавливаются в двух территориальных подразделениях — Брухзале и Клостер-Ленине. Поток проходящего материала огромен: в случае установок для литья преформ под давлением он составляет 830–1 300 кг/ч на одну установку. Однако технологические вызовы заключаются прежде всего в подготовке перерабатываемых материалов для процесса литья под давлением, так называемых «хлопьев для бутылок». Они с одной стороной должны быть пригодными для пищевых продуктов и с другой стороны — малозатратными в закупке и при подготовке. Уже много лет Hansa-Heemann делает ставку на закупку из экономики замкнутого цикла с партнерами в розничной торговле пищевыми продуктами, чтобы иметь возможность применять максимально чистосортный рециклированный материал. Вследствие большого спроса, эта стратегия, однако, все больше упирается в свои пределы. Высококачественный перерабатываемый материал сегодня является востребованным и дефицитным сырьем, и не достается бесплатно.
Новые вызовы
Одним из последних вызовов, с которым столкнулась Hansa-Heemann — феномен ПЭТ-бутылок со все более тонкими стенками. Когда стенки ПЭТ-бутылки становятся тоньше, на этапе использования бутылок это более экономично, однако цикл повторного использования усложняется вследствие измененных характеристик в механике сыпучих грузов соответствующих хлопьев для бутылок. Конкретно это означает, что подготовка материалов в преддверии процесса литья под давлением становится все более требовательной. Hansa-Heemann по этой причине приняла решение вместе с motan-colortronic запустить опытный проект пилотной установки. Разработанная концепция установки была реализована и протестирована на месте на заводе в Клостер-Ленине в отношении перерабатывающей машины. Рассчитанные технологические возможности установки за это время были отмечены и убедили участников.
Опытному проекту предшествовало многолетнее сотрудничество обеих компаний в сфере подготовки материалов. Первые контакты были установлены еще на выставке K 2007.
После этого совместно также был начат проект по хлопьям для бутылок. «С предшествующими установками motan-colortronic мы получили очень хороший опыт. С современными хлопьями для бутылок нам, конечно, сразу стало ясно, что мы вместе с motan-colortronic должны проложить новые пути», — заявил Ральф Меллер (Ralph Möller), руководитель направления изготовления преформ в Hansa-Heemann.
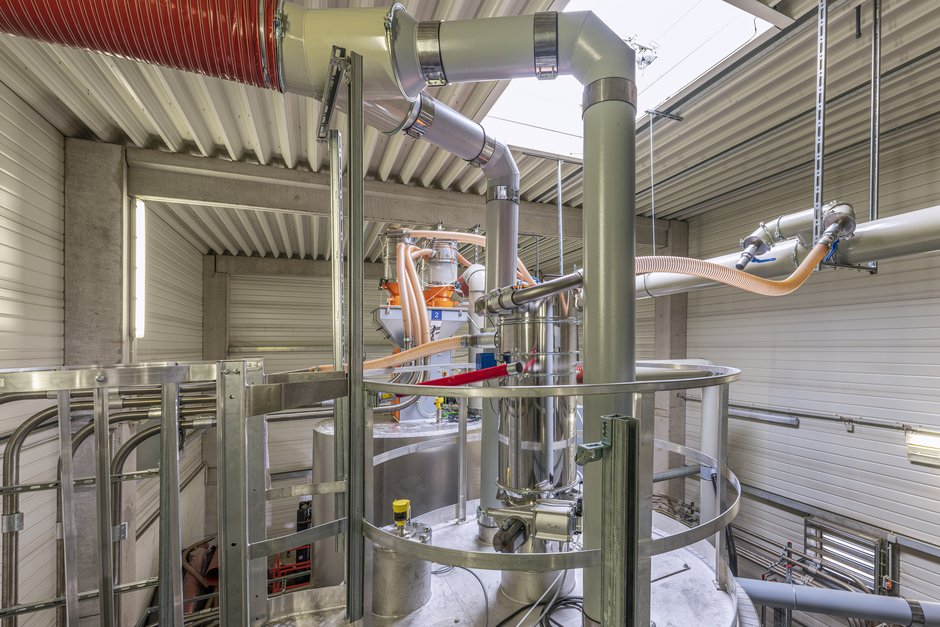
Смотреть прямо в глаза фактам
С 2017 г. Ральф Меллер наблюдал, что современные хлопья для бутылок все чаще становятся причиной дефектных преформ. Анализ техники установки не выявил ошибок, поэтому фокус был смещен на материал. Ральф Меллер и его команда быстро поняли, что хлопья из так называемых «легких бутылок» стали намного легче, чем в предыдущие годы. В загрузке они были, соответственно, более плотными, так что как текучесть при хранении и загрузке, так и прохождение в сушильном бункере для существующего технологического оборудования были недостаточными. Новые концепции в отношении подготовки материалов, в частности, для сушки и загрузки были также неизбежными.
Оценка основной стратегии
Hansa-Heemann достигла в прошлом большого успеха с хлопьями для бутылок, которые позволили использовать все более высокую долю перерабатываемого материала в преформах при одновременном сохранении необходимых качеств для процесса создания вакуума и заполнения, а также барьерных характеристик в готовом продукте. Это, с одной стороны, соответствует стратегии компании, а с другой стороны — обеспечивает также экономический успех.
«Эта основная стратегия не была проблемой, однако также должна была в дальнейшем стать частью решения», — заметил Ральф Меллер. Опытный проект с motan-colortronic преследовал тем самым простую и четкую цель: какая стратегия позволяет безопасно перерабатывать более легкие и мелкие хлопья для бутылок в ПЭТ-преформы с минимальной долей хлопьев 25 %?
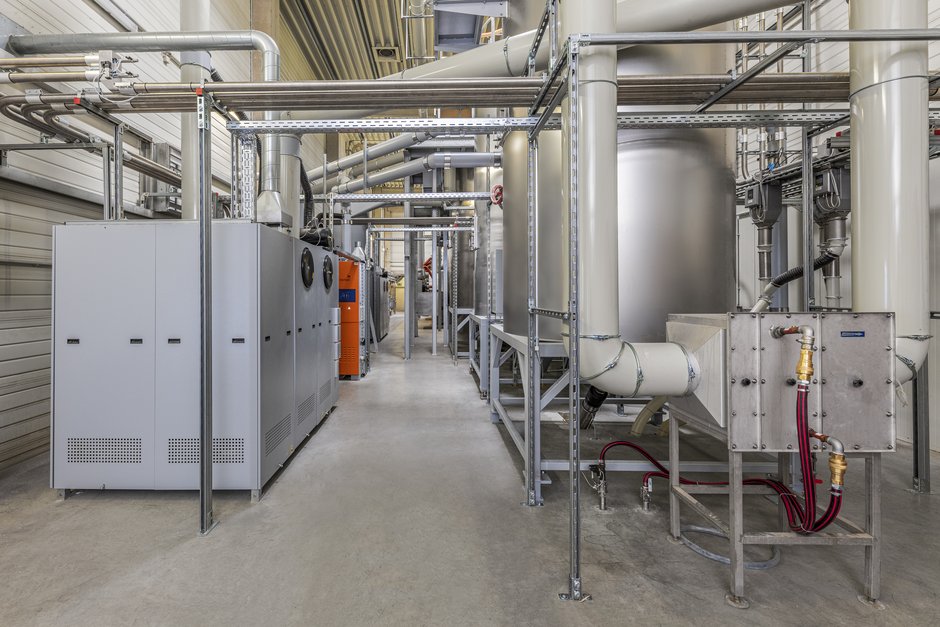
Прокладывать новые пути
Результаты предварительных исследований motan-colortronic продемонстрировали, что применяемые хлопья для бутылок показали достаточно высокую степень кристаллизации, так что в общем можно отказаться от кристаллизации. Таким образом, ключевым фактором была измененная механика сыпучих грузов и тем самым сопутствующие измененные характеристики хранения и текучести.
Поэтому, отделение применения motan-colortronic спроектировало новое устройство внутренней конструкции сушильного бункера, при которой благодаря измененной геометрии подача воздуха была оптимизирована под материал. Для этого мы в Исни провели пробные испытания, которые сразу продемонстрировали успех. Результатом является улучшенный поток воздуха благодаря более легким хлопьям, существенно повышающий эффективность сушки и при этом щадяще действующий в отношении материала. Хлопья для бутылок теперь высушены заметно более однородно. Кроме того, специальная геометрия сушильного бункера предотвращает возможное образование материалом мостиков.
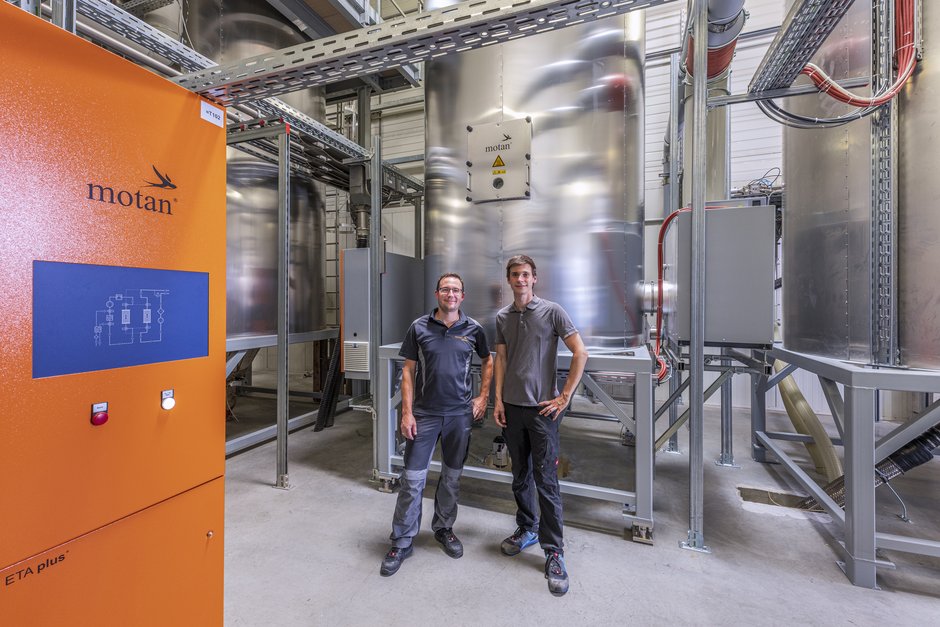
Переработка всей установки
После успешного нахождения решения для процесса сушки, эксперты motan-colortronic переработали существующую общую концепцию установки и адаптировали ее к новому перерабатываемому материалу. Существующая на заводе в Клостер-Ленине складская логистика расширяется подающими станциями для хлопьев для бутылок, поставляемых в биг-бегах. Подача материалов для пневматической загрузки осуществляется в резервуары и вытяжные коробки, адаптированные к материалу. Поскольку на заводе установлена централизованная система постоянного вакуума motan-colortronic с достаточной производительностью, распределение материала осуществляется через станцию распределения, так что в будущем в систему подачи материала могут встраиваться также и другие установки.
Система трубопроводов и загрузчик на сушильном бункере таким же образом рассчитаны для свойств хлопьев для бутылок, характерных для материала. Здесь применяется новая METRO G для больших объемов проходящего материала и хлопьев, оснащенная чрезвычайно большим выгрузным клапаном. Поскольку геометрия сушильного бункера обеспечивает равномерное протекания материала и предотвращает образование мостиков, можно отказаться от механической поддержки при выемке материалов. Резервуар встроен в платформу над перерабатывающей машиной и соединен с ней посредством спускного шланга. Прямо над отверстием загрузки материала перерабатывающей машины расположено волюметрическое дозировочное и смешивающее устройство, в котором — так же, как и в случае предыдущих установок — объединяются потоки нового и перерабатываемого материалов.
Успешные испытания
Первые испытания на месте с представленной пилотной установкой завершились с положительными результатами. В будущем запланировано пошаговое переведение всех установок на новую концепцию. «Это могло бы дать нам новые импульсы, установить новые масштабы в отношении экономичности, устойчивости и интенсификации экономики замкнутого цикла, чтобы поддерживать нашу конкурентоспособность», — надеется Ральф Меллер.
Дополнительная информация: знак качества RAL в отношении повторного использования ПЭТ в сфере упаковок для напитков
Устойчивая продукция и методы производства уже на протяжении многих лет лежат в философии Hansa-Heemann. Так компания еще в 2014 году получила знак качества RAL — как одна из четырех компаний-пионеров — за устойчивые ПЭТ-упаковки для напитков. Знаком качества RAL награждает Gütegemeinschaft Wertstoffkette PET-Getränkeverpackungen e.V., расположенная в Бад-Хомбурге (https://www.wertstoff-pet.de/).
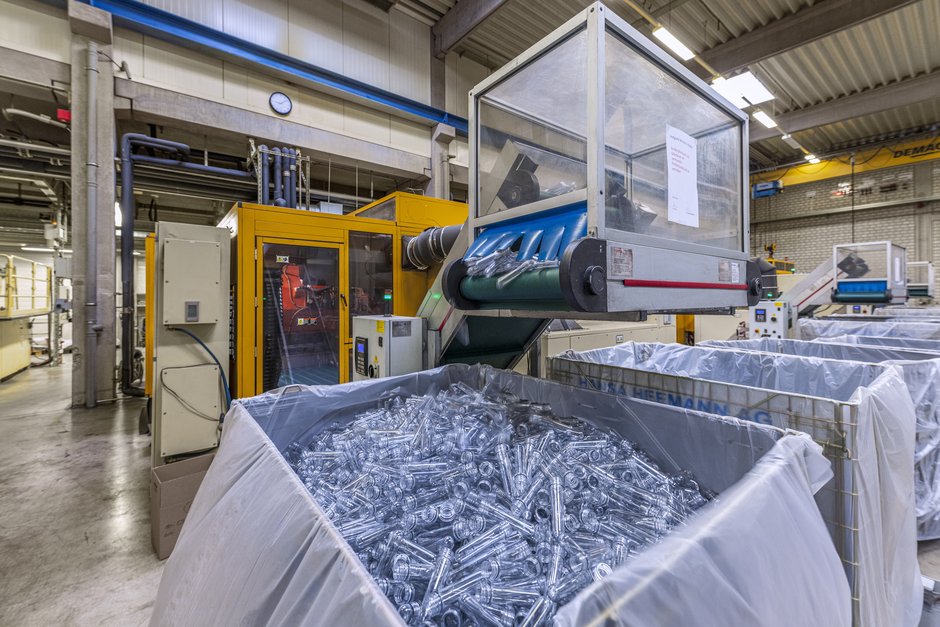
О Hansa-Heemann
Hansa-Heemann AG уже больше четырех десятилетий является ведущим поставщиком минеральных вод и прохладительных напитков в Германии. К компании относятся, кроме прочего, торговые марки Hella, Fürst Bismarck Quelle и St. Michaelis. Вместе с главным офисом в Реллингене рядом с Гамбургом, Hansa-Heemann имеет производственные подразделения в Аумюле, Траппенкампе, Клостер-Ленине, Лене и Брухзале. На производственных площадках в 2018 году было изготовлено и отгружено прибл. 2 млрд литров продукции. Годовой оборот от минеральной воды, вин с газированной водой, лимонадов, спортивных и энергетических напитков, а также фруктовых напитков составляет прибл. 300 млн евро. В компании работают прибл. 850 сотрудников; сейчас она является второй по размеру среди компаний-производителей минеральных вод в Германии.