Дозировка пластмассы 4.0 обретает форму
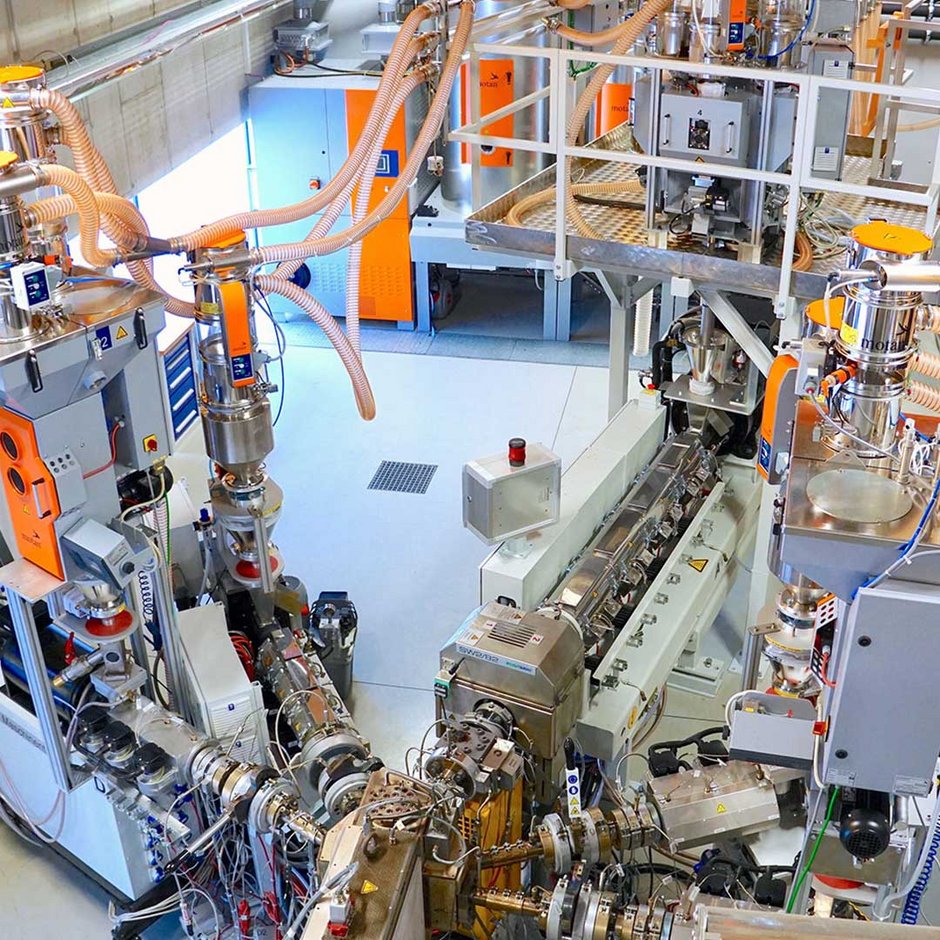
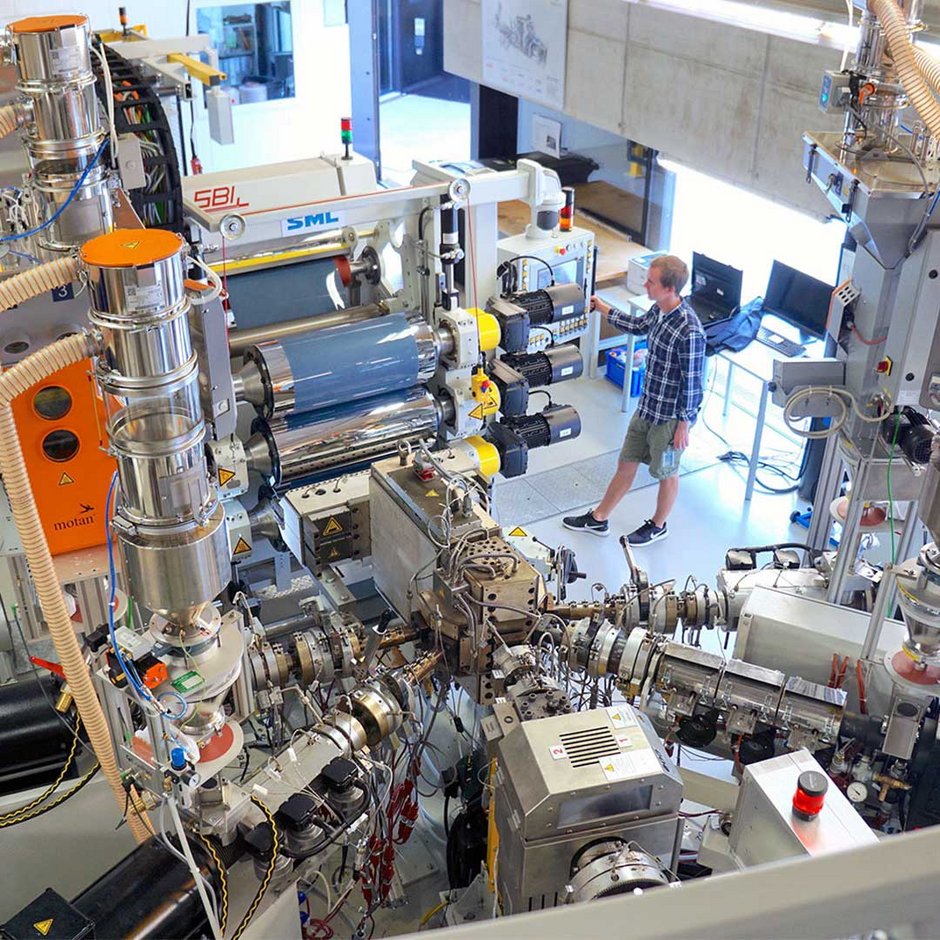
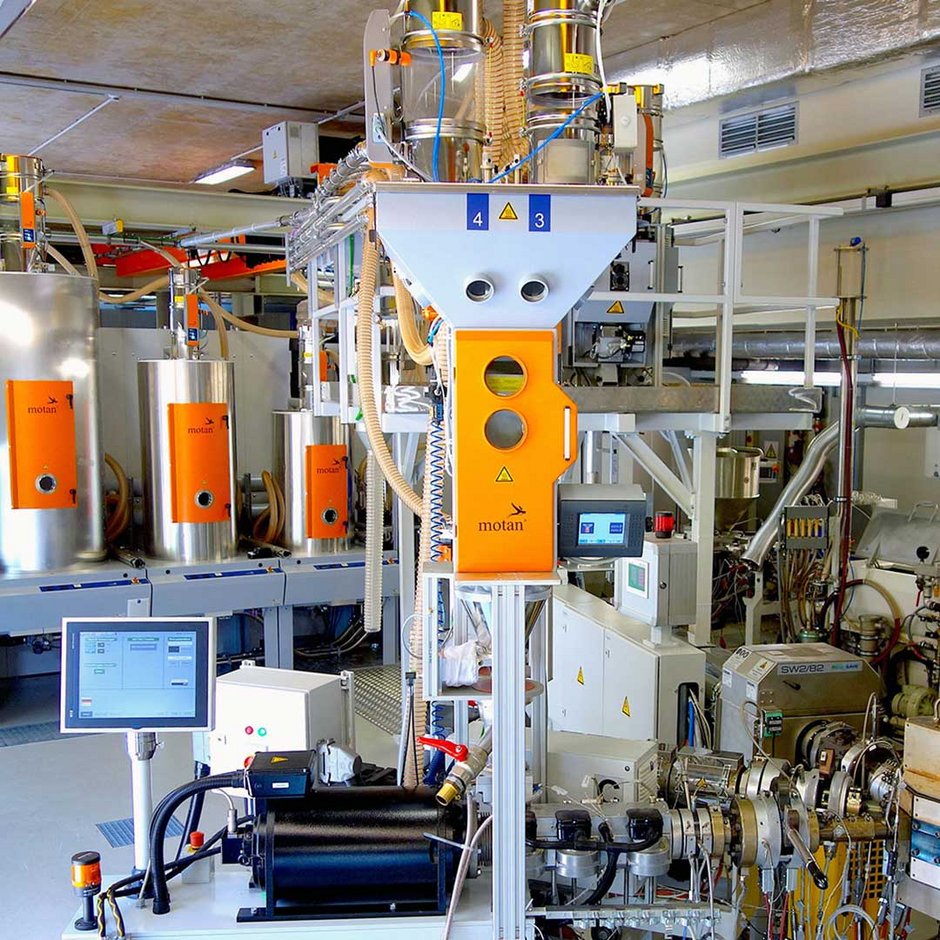
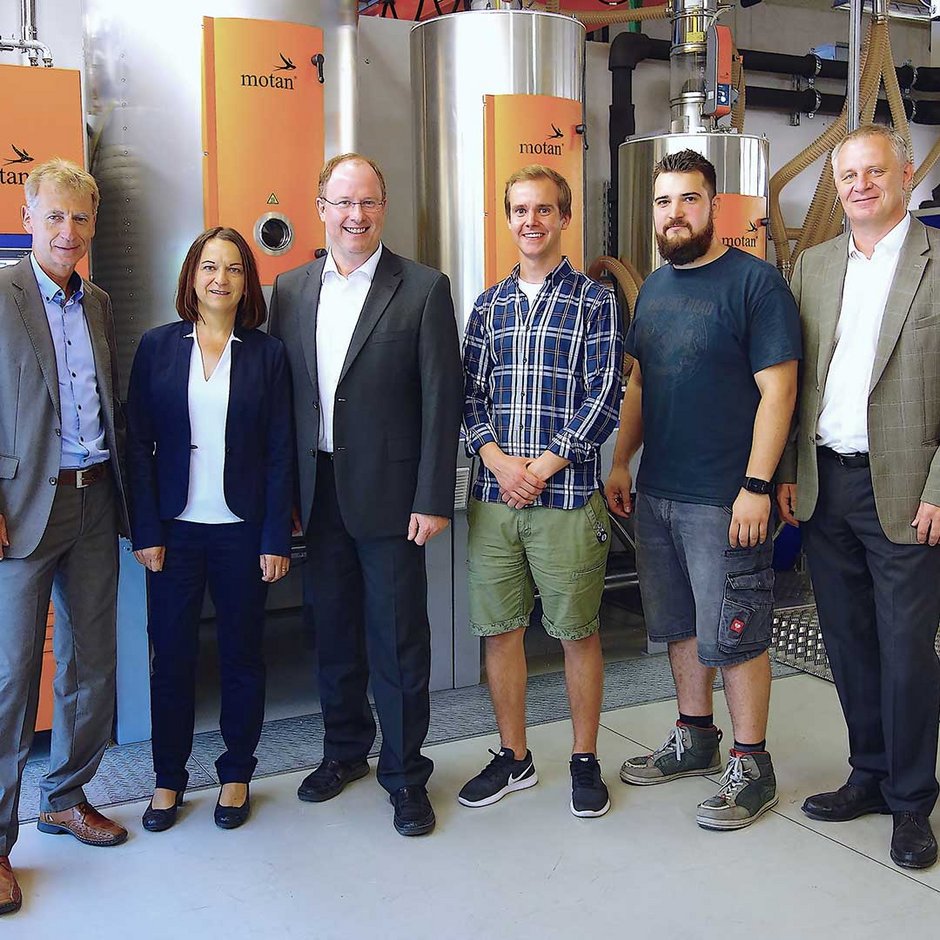
Комплексное автоматизированное управление процессом экструзионного оборудования находится в верхней части повестки дня института полимерной экструзии и многослойных материалов (IPEC) университета им. Йоханнеса Кеплера (JKU) в г. Линце на Дунае (Австрия).
Необходимые для этого алгоритмы управления разрабатываются совместно с промышленными партнерами и другими институтами JKU из сферы мехатроники и информатики. Платформа разработки – это 9-слойная экструзионная установка в промышленном масштабе. В этих разработках участвует в качестве партнера и компания motan. Целью сотрудничества является разработка простой в использовании системы управления оборудованием, в которой все компоненты общаются друг с другом и автоматически согласовываются в соответствии со стандартом Индустрии 4.0.
Найти оптимальную точку работы экструзионной установки, несмотря на очень широкие возможности в области сенсорной и измерительной техники, обработки данных и технологии управления, все еще является сложной задачей для оператора машины. В частности тогда, когда в зависимости от базовой машины дополнительно необходимо изменить эксплуатационные точки таких различных инфраструктурных объектов, как, например, устройства подачи и дозирования материала. Особенно, когда продукты часто меняются под давлением времени.
Именно это является отправной точкой для исследователей, техников и студентов института IPEC университета JKU в г. Линц. По этому поводу профессор университета Юрген Митлингер говорит следующее: «Наше видение – это саморегулируемая комплексная система, которая при переходе на другой продукт «берет с собою» все компоненты установки в новую рабочую точку, а затем постоянно согласовывает и оптимизирует их во время эксплуатации. Предпосылкой для этого является точное отображение реальности производства. В этих целях мы регистрируем измерительные сигналы всех компонентов системы в миллисекундном ритме. Наши специалисты по «большим данным» структурируют эти данные, которые представляют собой цифровую реальность теоретических физических процессов.
В конце проекта мы получим полное цифровое изображение всей системы, включая все инфраструктурные объекты. Наша цель состоит в работе с цифровой реальной машиной в качестве симулятора процесса и в дополнении его функцией самообучения. Таким образом, новые рабочие состояния, а также алгоритмы управления для текущей работы можно заранее моделировать и оптимизировать во всех деталях. Таким образом, продолжительное время смены продукции и фазы запуска останутся в прошлом, что облегчит гибкое использование экструзионных установок. Важной предпосылкой успеха исследований является возможность полностью интегрировать процессы инфраструктурного оборудования в процесс работы базовой установки.»
Оптимальный общий процесс благодаря оптимальным частичным процессам
Подпроектом в рамках всего проекта является изучение гравиметрического дозирования как минимальных, так и максимальных пропускных способностей. Значение этого частичного аспекта иллюстрирует, например, спецификацию 7-слойной барьерной пленки толщиной 1 мм. Ее центральный слой изготовлен из высококачественных барьерных материалов толщиной 50 мкм (= 5 процентов материала). Над ней расположены двое связующих средств, каждое толщиной 25 мкм, а также два слоя конструкционного материала толщиной 350 мкм, например, из обрабатываемого материала, каждая с поверхностным покрытием толщиной 100 мкм. Для достижения неизменно ровной толщины слоя наиболее важной переменной является дозирующая стабильность подачи материала.
Тот факт, что устройства компании motan соответствуют ожиданиям исследователей JKU, было технической основой для заключения договора о партнерстве с IPEC/JKU. На следующем этапе планируется также расширение партнерства на создание фабрики будущего на университетском кампусе – LIT Factory. Там работы по экструзии и литья под давлением будут осуществляться согласно Индустрии 4.0.