Preforme in PET sostenibili
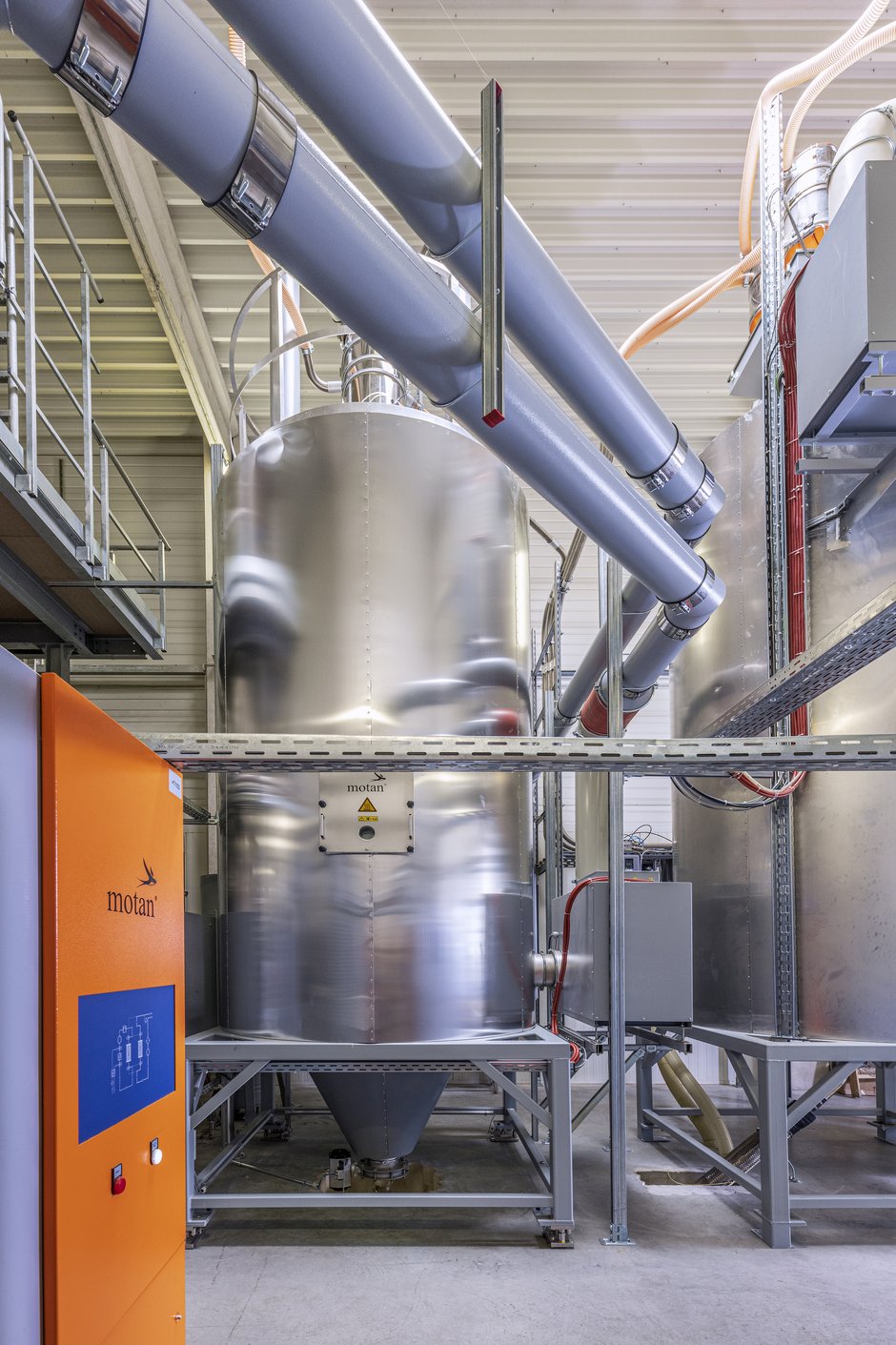
Riciclaggio quando le materie prime sono scarse
Le preforme vengono prodotte per gli altri stabilimenti del gruppo, in due siti, Bruchsal e Kloster Lehnin. La portata di materiale è enorme: con i sistemi di stampaggio ad iniezione preforma, a seconda del sistema, è compresa tra 830 e 1.300 kg / h a seconda dell’impianto. Tuttavia, le sfide dell’ingegneria di processo risiedono soprattutto nella preparazione del materiale di riciclaggio per il processo di stampaggio ad iniezione, i cosiddetti fiocchi di bottiglia. Queste devono, da un lato essere adatte agli alimenti e, dall’altro, devono essere convenienti dal punto di vista dei costi di acquisto e della lavorazione. Da molti anni Hansa-Heemann si affida all’approvvigionamento dell’economia circolare con i partner del commercio al dettaglio di generi alimentari per poter utilizzare il riciclato più puro possibile. Tuttavia, a causa dell’elevata domanda, questa strategia sta raggiungendo sempre più spesso i suoi limiti. Oggi, il materiale da riciclo di alta qualità è una materia prima molto ricercata e scarsa e non può essere ottenuta gratuitamente.
Nuove sfide
La sfida più recente di Hansa-Heemann è stata il fenomeno delle bottiglie in PET a parete sempre più sottile. Se le bottiglie in PET diventano più sottili, questo è più economico nella fase di utilizzo delle bottiglie, ma rende più difficile il ciclo di riciclaggio a causa delle mutate proprietà della meccanica del materiale sfuso dei relativi fiocchi di bottiglie. Concretamente questo significa che la preparazione del materiale in vista del processo di stampaggio ad iniezione diventa molto più impegnativa. Hansa-Heemann ha perciò deciso di avviare un progetto di sviluppo di un impianto pilota insieme a motan-colortronic. Il concetto di impianto che ne è derivato è stato implementato e testato in loco presso lo stabilimento di Kloster Lehnin per una macchina di lavorazione Nel frattempo, la capacità di processo desiderata dell’impianto sta diventando evidente e sta convincendo gli attori.
Il progetto di sviluppo è stato preceduto da molti anni di collaborazione tra le due aziende nel campo della lavorazione dei materiali. I primi contatti esistevano già dal K 2007.
Quindi era logico iniziare il progetto per i fiocchi di bottiglia insieme. “Con i precedenti sistemi di motan-colortronic, abbiamo avuto ottime esperienze. Per i fiocchi di bottiglia di oggi, tuttavia, ci è stato subito chiaro che avremmo dovuto aprire nuove strade insieme a motan-colortronic”, afferma Ralph Möller, responsabile della produzione di preforma presso Hansa-Heemann.
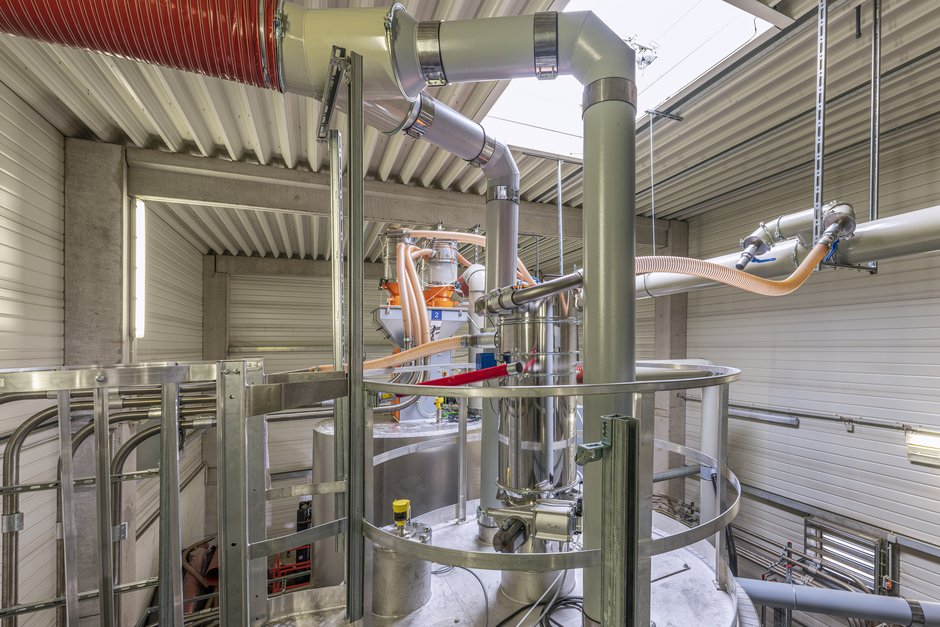
Guardare chiaramente la realtà
Dal 2017 Ralph Möller si era accorto che gli attuali fiocchi di bottiglie sono stati sempre più spesso causa di preforma difettose. Un’analisi della tecnologia dell’impianto non ha rivelato errori, quindi l’attenzione si è concentrata sul materiale. Ralph Möller e il suo team hanno subito scoperto che i fiocchi delle cosiddette “bottiglie leggere” erano molto più leggeri rispetto agli anni precedenti. Alla rinfusa erano conseguentemente più compatti, cosicché sia le proprietà di flusso durante lo stoccaggio e il trasporto che il flusso nella tramoggia a secco erano insufficienti per la tecnologia dell’impianto esistente. Erano quindi inevitabili nuovi concetti nella preparazione del materiale, in particolare per l’essiccazione e il trasporto.
Valutazione della strategia di base
In passato, Hansa-Heemann ha ottenuto un grande successo con i fiocchi di bottiglia, che hanno permesso di ottenere una percentuale sempre maggiore di materiale riciclato nelle preforma, mantenendo allo stesso tempo le proprietà richieste per il processo di soffiaggio e riempimento e le proprietà barriera del prodotto finito. Da un lato, questo si inserisce nella strategia aziendale dell’azienda stessa e, dall’altro, garantisce anche il successo economico.
“Il problema non era questa strategia di base, ma dovrebbe continuare a far parte della soluzione”, dice Ralph Möller. Il progetto di sviluppo con motan-colortronic aveva quindi un obiettivo semplice e chiaro: quale strategia permette di trasformare in modo affidabile i fiocchi di bottiglie più leggeri e più piccoli in preforma PET con almeno il 25 % di fiocchi?
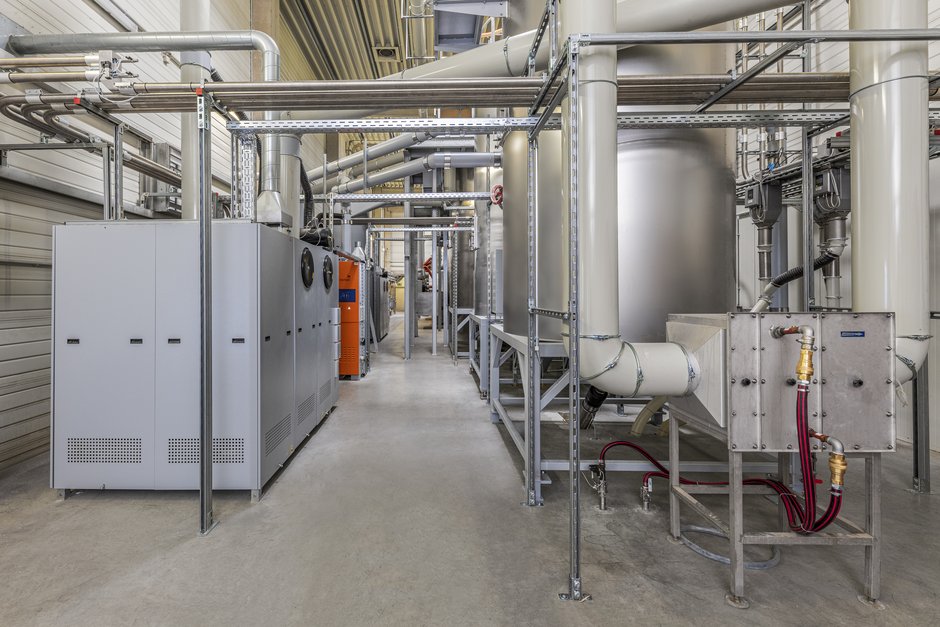
Percorrere nuove strade
Indagini preliminari svolte da motan-colortronic hanno dimostrato che i fiocchi di bottiglia utilizzati hanno un grado di cristallizzazione sufficientemente elevato, in modo che, in generale, la cristallizzazione può essere evitata. Il fattore chiave è stato quindi il cambiamento della meccanica dei solidi sfusi e i cambiamenti associati nelle proprietà di stoccaggio e di flusso.
Il reparto applicativo di motan-colortronic ha quindi progettato un nuovo design per la struttura interna della tramoggia a secco, in cui l’alimentazione dell’aria è stata ottimizzata per il materiale da una geometria modificata. Per questo motivo sono stati effettuati test a Isny, che hanno avuto successo fin dall’inizio. Il risultato è un migliore flusso d’aria attraverso i fiocchi leggeri, che aumenta notevolmente le prestazioni di asciugatura e protegge anche il materiale. Ora i fiocchi di bottiglia vengono essicati in modo molto più omogeneo. La speciale geometria della tramoggia a secco impedisce anche possibili ponti del materiale.
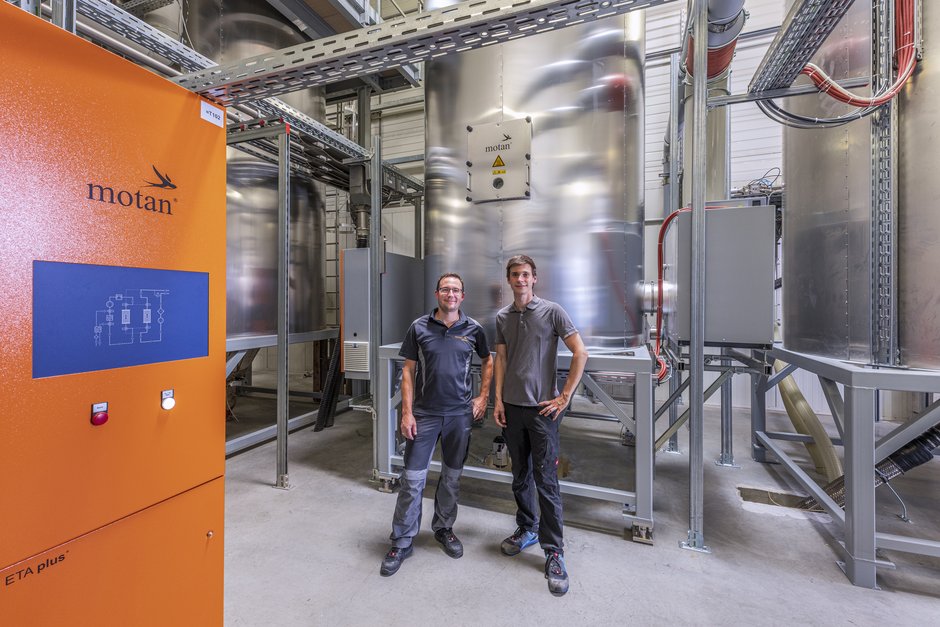
Revisione del sistema completo
Dopo aver trovato una soluzione di successo per il processo di essiccazione, gli esperti di motan-colortronic hanno rivisto il concetto generale dell’impianto esistente e lo hanno adattato al nuovo materiale di riciclaggio. La logistica di magazzino dello stabilimento di Kloster Lehnin sarà integrata da stazioni di alimentazione per i fiocchi di bottiglie consegnati in grandi sacchi. L’alimentazione del materiale per il trasporto pneumatico avviene in contenitori e cassette di aspirazione abbinate al materiale. Poiché nell’impianto è installato un sistema di aspirazione centrale permanente di motan-colortronic con prestazioni sufficienti, la distribuzione del materiale può essere effettuata tramite una stazione di collegamento in modo che anche altri sistemi possano essere integrati nell’alimentazione del materiale in un momento successivo.
Il sistema di tubazioni e il sistema di trasporto sulla tramoggia a secco sono progettati anche per le proprietà specifiche del materiale dei fiocchi di bottiglia. Qui, la nuova METRO G è stata utilizzata per grandi produzioni di materiale e fiocchi, dotate di un lembo di espulsione extra-large. Poiché la geometria della tramoggia a secco assicura uno scarico uniforme del materiale e contrasta i ponti, non c’è bisogno di un supporto meccanico durante la rimozione del materiale. Il contenitore viene installato in una piattaforma sopra la macchina di lavorazione e collegato ad essa tramite un tubo di scarico. Direttamente sopra l’ingresso del materiale della macchina di lavorazione è presente un’unità volumetrica di dosaggio e miscelazione in cui – come nei sistemi precedenti – si combinano i flussi di materiale vergine e materiale riciclato.
Test di successo
I primi test in loco con l’impianto pilota descritto sono stati positivi. Per il futuro è prevista la conversione graduale di tutti gli impianti al nuovo concetto. “Questo potrebbe darci nuovi impulsi e standard per la redditività, la sostenibilità e l’intensificazione della gestione del riciclaggio per mantenere la nostra competitività”, spera Ralph Möller.
Informazioni di base: marchio di qualità RAL per il riciclaggio del PET negli imballaggi per bevande
Prodotti e metodi di produzione sostenibili appartengono alla filosofia Hansa-Heemann da molti anni. Già nel 2014 l’azienda ha ricevuto il marchio di qualità RAL come una delle quattro aziende pioniere nel settore degli imballaggi sostenibili per bevande in PET. Il marchio di qualità RAL viene assegnato dalla Gütegemeinschaft Wertstoffkette PET-Getränkeverpackungen e.V., con sede a Bad Homburg (https://www.wertstoff-pet.de/).
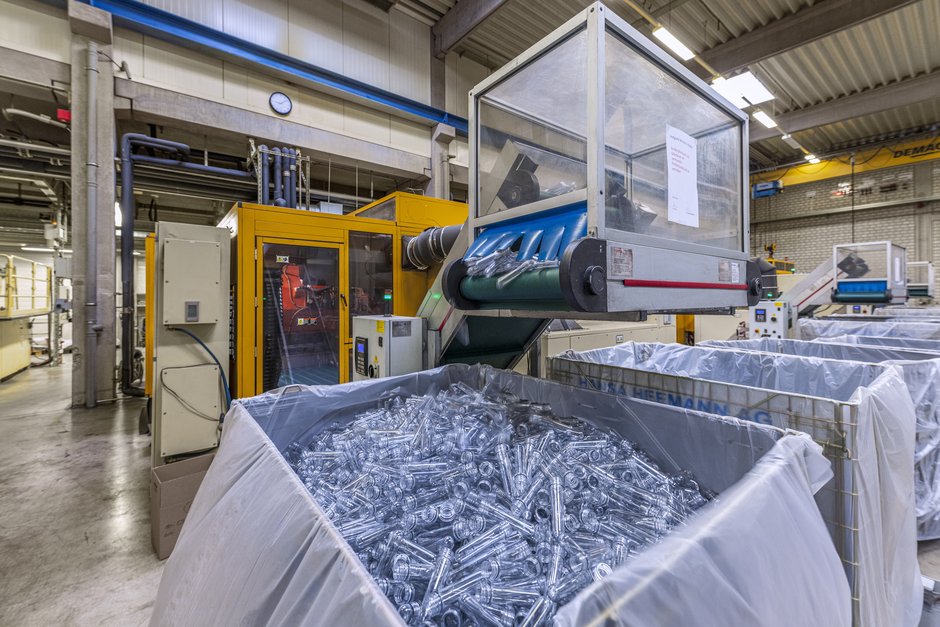
A proposito di Hansa-Heemann
Hansa-Heemann AG è da oltre quattro decenni uno dei principali fornitori di acqua minerale e bibite analcoliche in Germania. A questa azienda appartengono i marchi Hella, Fürst Bismarck Quelle e St. Michaelis. Oltre alla sede centrale di Rellingen vicino ad Amburgo, Hansa-Heemann ha stabilimenti ad Aumühle, Trappenkamp, Kloster Lehnin, Löhne e Bruchsal. Nel 2018 sono stati prodotti e venduti circa 2 miliardi di litri nei siti di produzione. Il fatturato annuo con acque minerali, Schorlen, limonate, bevande sportive ed energetiche e succhi di frutta ammonta a circa 300 milioni di euro. L’azienda impiega circa 850 dipendenti ed è attualmente il secondo fornitore di acqua minerale più grande della Germania.