Des bouteilles aux plaques
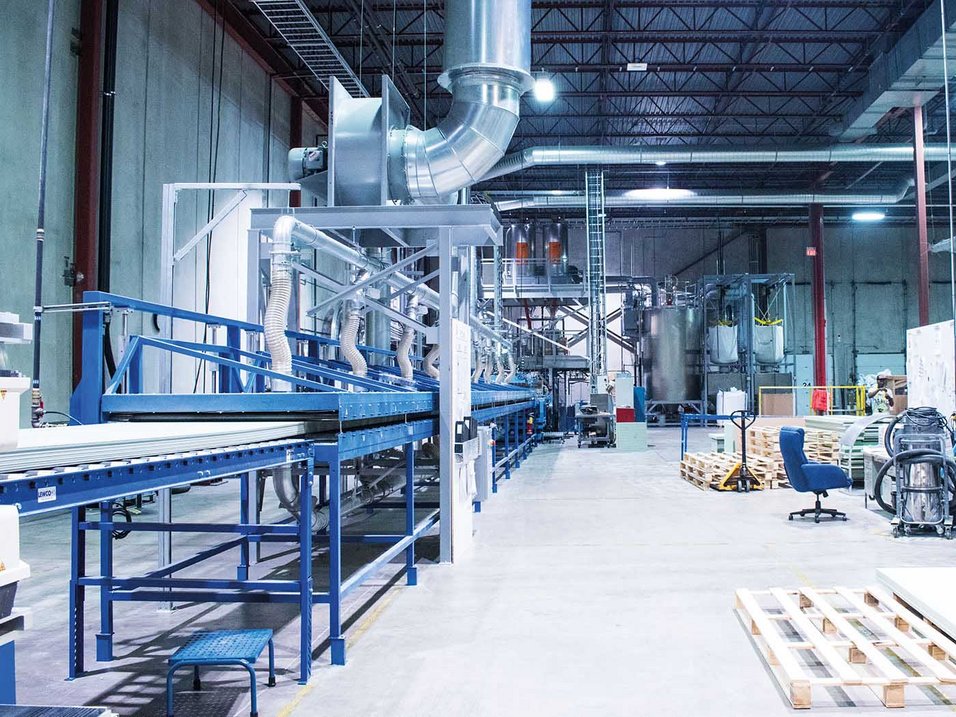
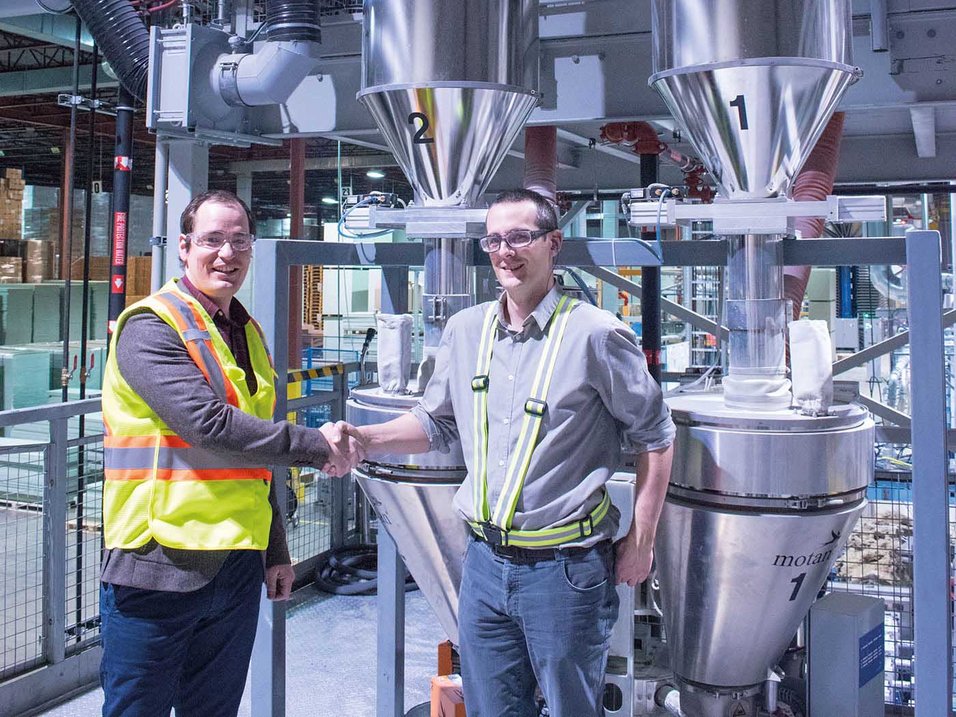
Deux ans avant cette décision, Armacell a fait l’acquisition de la société canadienne « Industrial Thermo Polymers Limited (ITP) » de Brampton. C’est là que des tubes en mousse, ainsi que d’autres produits en PE, étaient produits jusqu’ici sur des installations nettement plus petites. La décision de créer une production d’âmes en mousse PET sur le site canadien a été prise trois mois déjà après l’achat d’ITP.
Comparée aux chaînes d’extrusion existantes, la nouvelle installation est nettement plus complexe : son débit maximal est de 1 500 kg/h et l’épaisseur des larges plaques de ~1,2 mètres (4 pieds) peut être réglée entre cinq et 150 mm, en adaptant la longueur en fonction du souhait du client. La manutention du matériau dont était chargé Armacell Canada motan Inc., une filiale du Groupe motan, s’avère tout aussi complexe. Les deux partenaires se connaissent indirectement depuis longtemps, à travers leur collaboration avec l’agence de motan-colortronic, ORA, en Belgique.
« Un avantage, pour nous, a été que nous avons obtenu de motan elle-même l’équipement complet pour la manutention, comprenant le séchage, l’alimentation et le dosage », explique Frédéric Gauder, Directeur de production PET, qui est arrivé au Canada d’Armacell Benelux, en Belgique, afin de gérer l’intégration de l’installation à Brampton. motan Inc. est l’unique entreprise en Amérique du Nord qui pilote de façon normalisée tous les produits nécessaires pour les processus en continu : du stockage et du séchage au dosage et au mélange avec des réseaux de contrôle intelligents, en passant par l’alimentation.
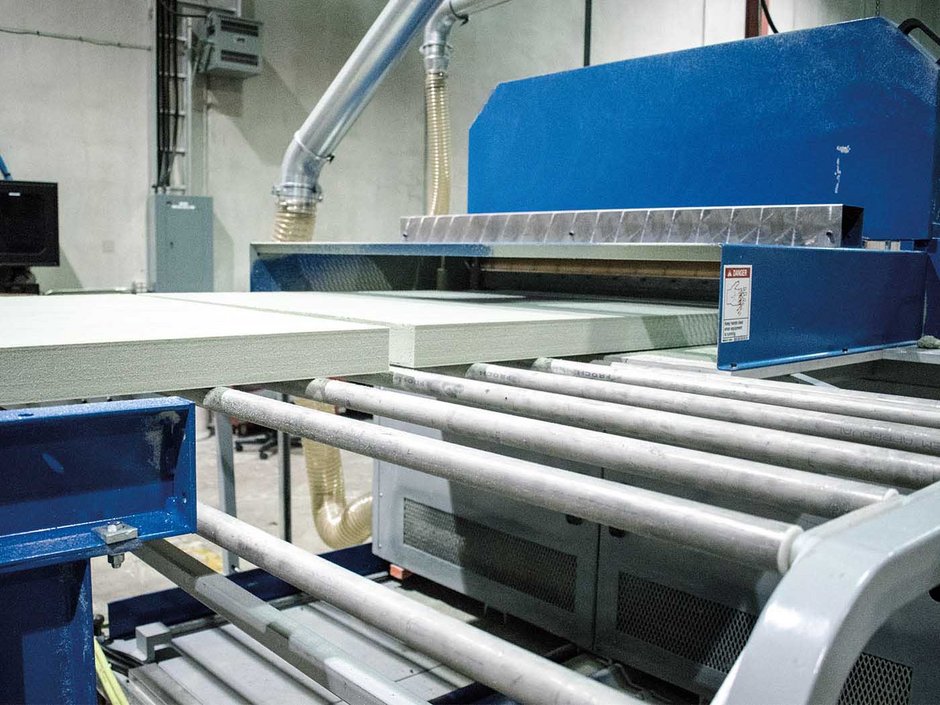
Un défi, lors de la conception, était constitué par le besoin en matières de l’extrudeuse. « Étant donné que l’installation a une vitesse de transmission relativement élevée et que le PET et les additifs requièrent de longs temps de séchage, nous avons dû connecter en parallèle deux générateurs d’air sec LUXOR A 2400 et utiliser des trémies de séchage de dimension équivalente. En outre, l’installation a dû être construite de la manière la plus compacte possible, en raison d’un manque d’espace », rapporte Jan Rickenbach, Directeur régional des ventes chez motan Inc.
L’alimentation en matériaux de l’extrudeuse est réalisée une fois avec deux trémies de séchage d’une contenance de 9 000 litres chacune pour les matières neuves en PET et les matières rebroyées en PET. A cela s’ajoutent deux autres trémies de séchage de 1 200 litres chacune, pour les additifs spéciaux. Tandis que le PET doit sécher pendant environ six heures, le séchage des additifs est plus intense. Afin de gagner de la place et d’épargner d’autres appareils d’alimentation, les deux trémies de séchage pour les additifs pour l’alimentation des matériaux en PET ont été montées sur une passerelle, directement au-dessus de l’extrudeuse.
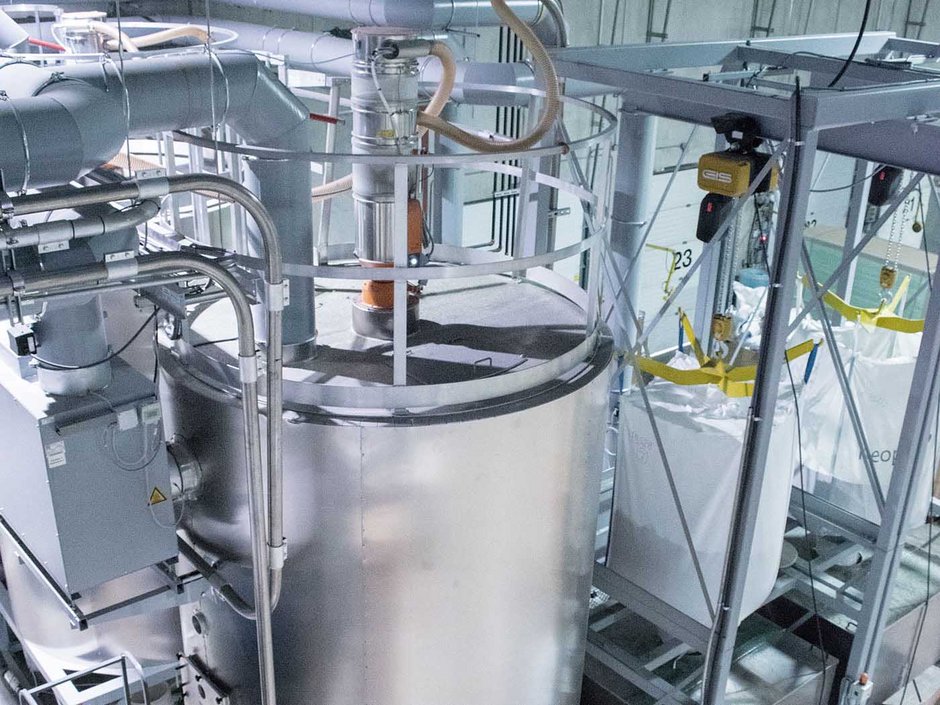
Le dosage des composants est réalisé par une station gravimétrique de dosage et de mélange synchrone GRAVIPLUS®, qui de son côté, est alimentée par deux appareils d’alimentation à haute température, METRO HCG 50 et HCG 15, ainsi que par une goulotte vibrante. Un convoyeur sans filtre, combiné à un filtre central METRO F50-28, d’un modèle à haute température, est utilisé, afin de filtrer la poussière provenant du matériau de recyclage. Deux circuits de vide servent à l’alimentation des matériaux : l’un alimente les deux grandes trémies de séchage PET et l’autre GRAVIPLUS®, ainsi que les trémies de séchage d’additifs.
L’ensemble des dispositifs d’alimentation en matériaux – séchage, alimentation et dosage – sont commandés de façon centralisée par le poste de commande de l’extrudeuse. C’est là que toutes les données requises, telles que les valeurs théoriques, les formulations, sont saisies et vérifiées. La communication entre le poste de commande de l’extrudeuse et l’installation motan se produit par éthernet et une interface pro sur le net. « Afin de prendre en compte les particularités de l’installation relatives au séchage et au dosage, il s’est avéré nécessaire de modifier le logiciel en fonction. Dans ce contexte, il a été important pour nous d’harmoniser et de tester l’interface avec le fabricant de l’extrudeuse à un stade très précoce », explique Steve Watson, Directeur du support technique chez motan Inc. « L’exigence, consistant à pouvoir achever la ligne PET dans un délai court, a été rendue possible par un travail en équipe et en particulier, grâce à la motivation de tous les partenaires qui y ont participé », souligne Frédéric Gauder.
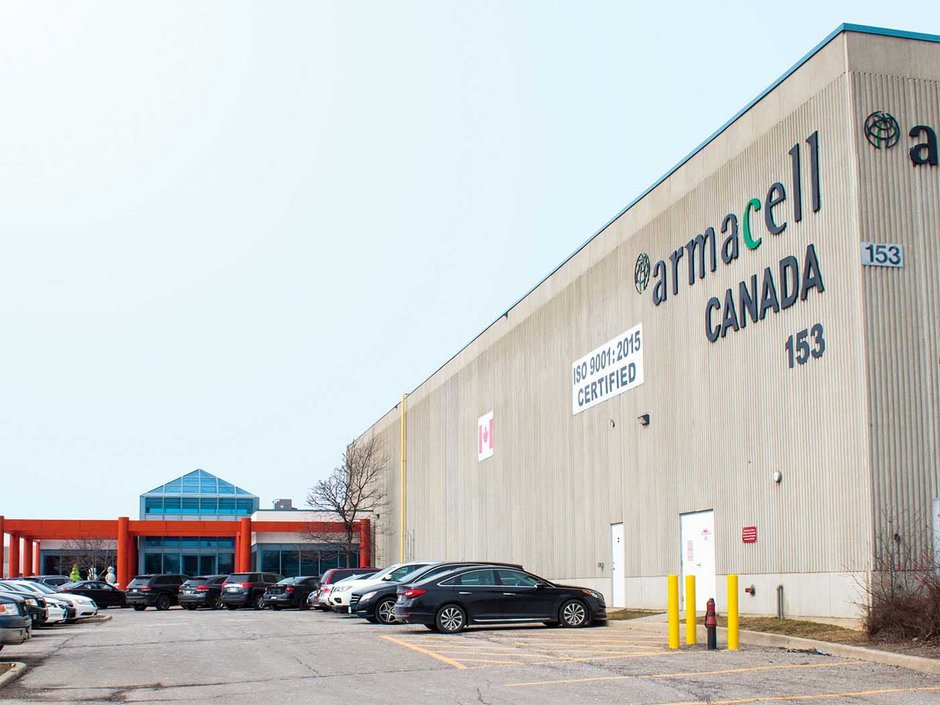
AU-SUJET D’ARMACELL
Inventeur des matériaux isolants flexibles pour l’isolation de l’installation et fournisseur leader de mousses techniques, Armacell a développé des solutions thermiques, acoustiques et mécaniques innovantes et sécuritaires, prodiguant une valeur ajoutée durable pour ses clients. Les produits Armacell contribuent chaque jour de façon décisive à l’augmentation du rendement énergétique dans le monde entier. Avec 3 000 collaborateurs et 25 sites de production dans 16 pays, l’entreprise est présente dans deux secteurs d’activité, « Advanced Insulation » et « Engineered Foams » ; en 2017, elle a généré un chiffre d’affaires de 603 millions d’Euros et un EBITDA ajusté de 102 millions d’Euros. Armacell se concentre sur la fabrication de matériaux isolants pour l’isolation de l’installation, de mousses à haut rendement pour l’industrie hightech et de construction légère, ainsi que pour la technologie de tapis aérogel de la prochaine génération.
Vous trouverez de plus amples informations sur : www.armacell-core-foams.com