40 Ans d’expérience et un penchant pour les projets de moulage par injection fastidieux
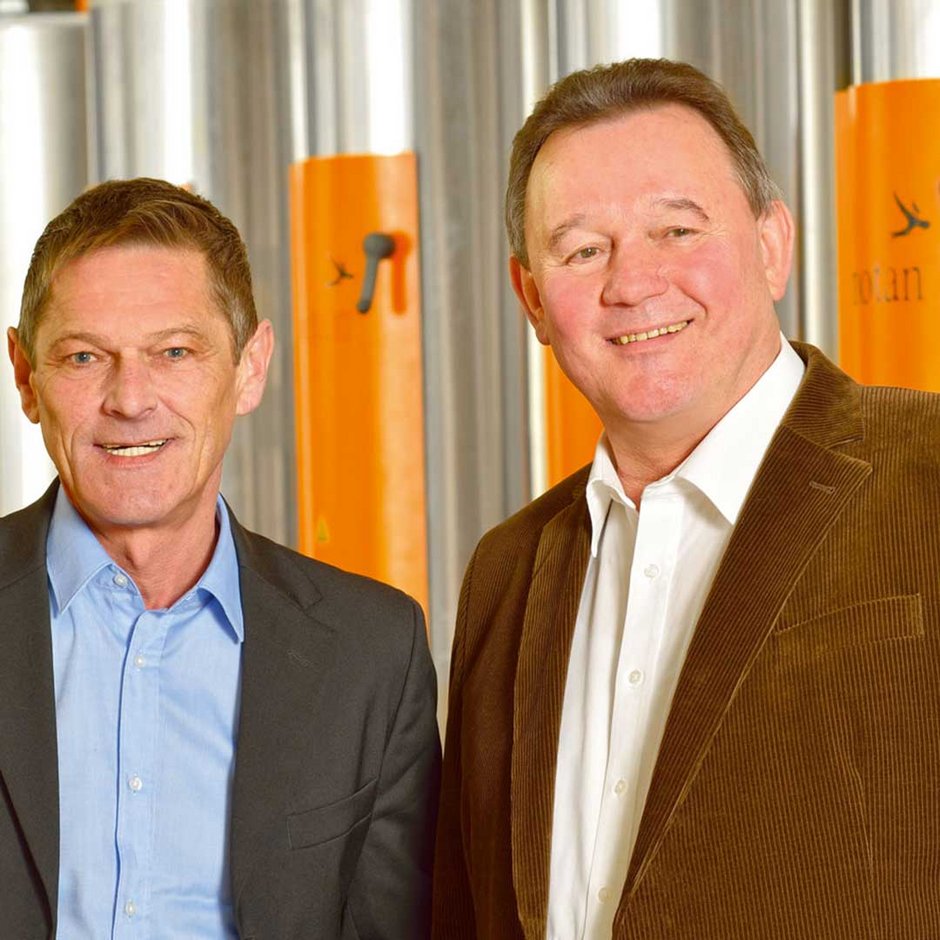
L’entreprise Mayer se considère comme un fournisseur de systèmes exible à part entière, qui offre tout : depuis la conception du produit jusqu’à la livraison des modules prêts au montage. Sur environ 40 presses à injection avec des forces de serrage entre 250 et 17 000 kN, des pièces de formes complexes à surfaces impeccables, car visibles, sont réalisées. Ce qui est inhabituel pour une entreprise de cette taille est la performance du traitement de surface : diverses technologies d’impression et une propre installation de pein- ture assurent la fabrication de pièces extérieures pour véhicules d’aspect mat ou luisant en série. Diverses techniques de xation et d’assemblage ainsi qu’une propre logistique complètent la gamme des prestations. C’est une vaste gamme de matières thermoplastiques, notamment en TPE mais aussi à base de multi-composants qui y est traitée.
Depuis sa fondation, l’entreprise n’a cessé de croître et motan-colortronic en faisait partie dès le début. Et la prochaine étape d’expansion est déjà en cours de plani cation.
Fournisseur de rang 1 et 2 pour les constructeurs automobiles et leurs sous-traitants et ce comme PME de moulage par injection et fabricant de moules avec un effectif de 110 personnes au Sud de l’Allemagne ? Comment y êtes-vous arrivé Monsieur Mayer ?
V. Mayer //
Nous avons toujours eu un penchant pour les produits inédits et les défis, que d’autres entreprises de moulage par injection refusent de relever, comme p. ex. des éléments simples comme les tapis auto en TPE pour la BMW X1. Les éléments design que le client peut utiliser pour personnaliser sa BMW Mini, exigent d’excellentes surfaces dans une grande variété de couleurs. Là, nos différentes installations de traitement de surface et le fait que nous traitons une vaste gamme de matériaux, constituent un grand atout. Cela nous rend très flexible et très performant. Et ceci nous permet également de décrocher en tant que PME des projets sophistiqués et attrayants comme des éléments design pour la VW Passat, partiellement peints mat et luisant.
Pour en revenir à la variété des matériaux. La production moderne montre que vous misez totalement sur motan-colortronic pour la manutention des matériaux. Pourquoi ?
V. Mayer // 40 ans de bonne collaboration. Parce que là tout le monde sait ce qui est important pour l’autre. On se comprend. Depuis la fondation de notre entreprise dans les années 70, nous avons fait de bonnes expériences avec les séchoirs ainsi que les mélangeurs et doseur motan. Ceci vaut également pour les conseils d’experts. Surtout quand il s’agit de la transformation de nouvelles matières, plus complexes, motan-colortronic nous a toujours épaulés avec ses bons conseils et son service rapide. Nous avons donc toujours eu recours aux composants toujours plus puissants de motan-colortronic à chaque étape de croissance. En 2014 nous avons alors conjointement mis en place un nouveau concept d’économie d’énergie uniforme avec un approvisionnement en matériau centralisé, pour pouvoir assurer une production encore plus rentable et exible à l’avenir. Aujourd’hui, nous préséchons environ 70 % de nos matériaux tels que le PA, le PC et l’ABS.
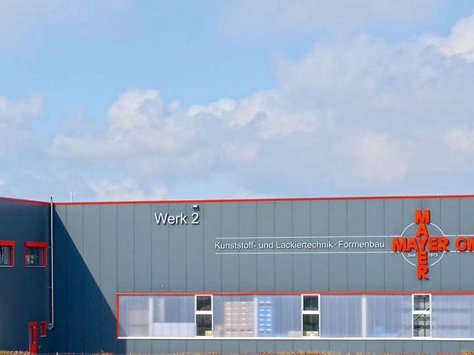
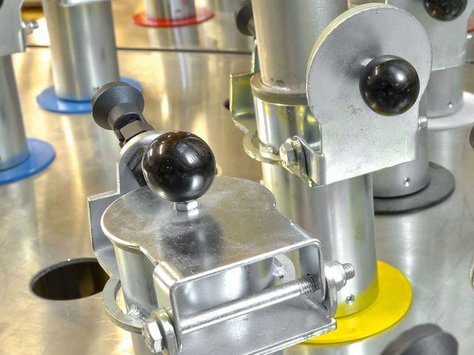
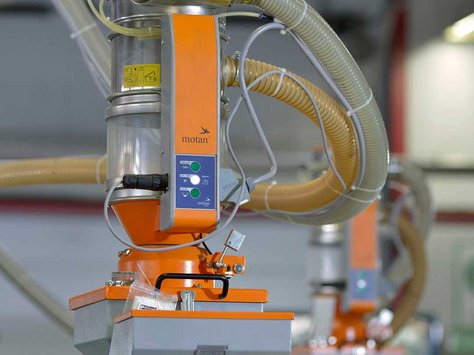
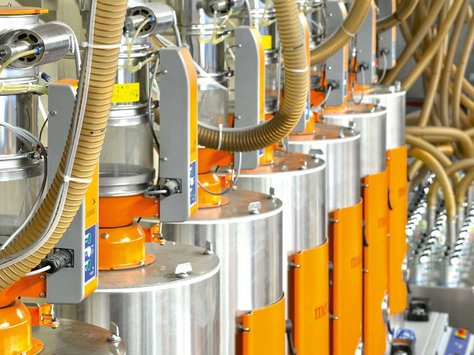
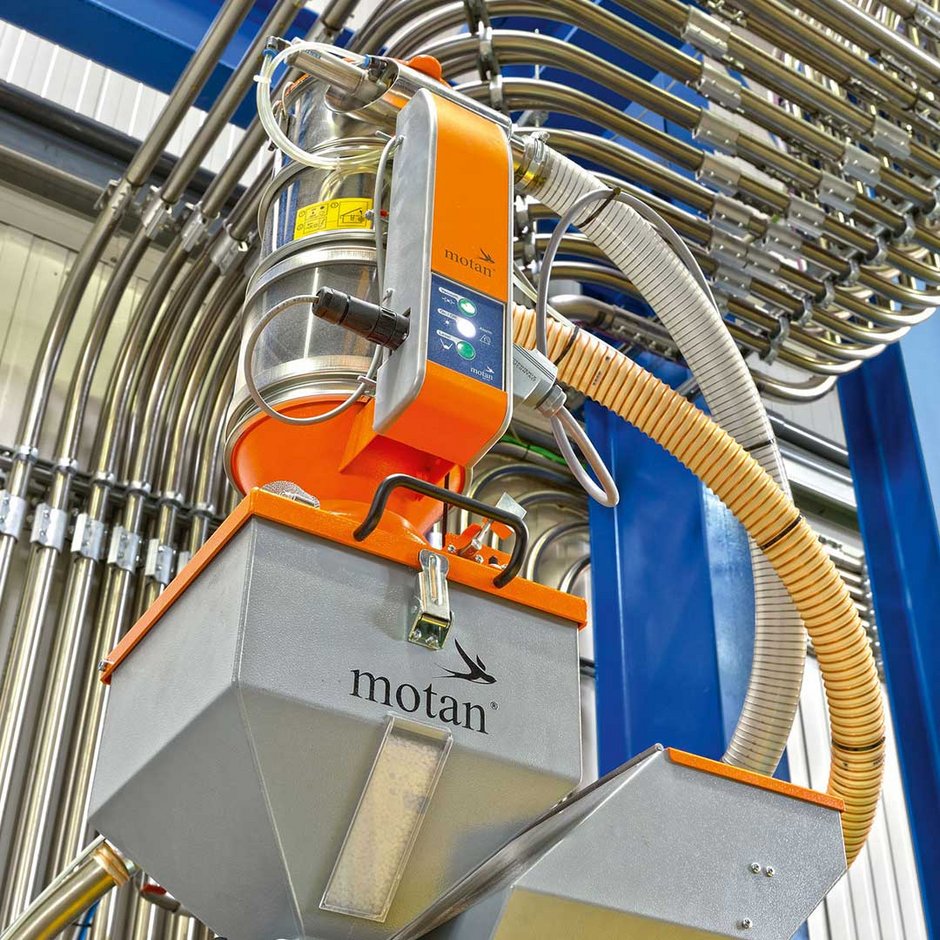
Comment avez-vous conçu l’approvisionnement en matériel ?
V. Mayer //
Lorsque l’on dispose de plus de 40 presses d’injection et qu’on traite de plus en plus de matériaux, un approvisionnement en matériau décentralisé ne répond plus aux exigences requises. Dans ces cas, on a besoin d’un concept global. Déjà rien que pour diminuer la consommation d’énergie pendant le séchage. Et ceci s’applique d’autant plus si vous êtes toujours en pleine expansion. Pour attaquer cette étape, nous avons une fois de plus consulté Ingo Staib et Anton Küble de motan-colortronic et nous avons développé un concept avant-gardiste qui répond exactement à nos besoins. Ce concept va du stockage du matériau en passant par la technologie de séchage et de distribution jusqu’à l’injection automatique de matériaux recyclés et la technologie de mélange et de dosage sur les machines.
Dans ce domaine, nous avons tout simplement eu besoin d’une vaste expertise en termes de conseils, même pour les problèmes secondaires, tels que l’effet de la poussière sur notre qualité de moulage irréprochable. motan-colortronic s’est avéré être un véritable partenaire et n’a rien promis qui n’a pas été tenu à la n. Les plans et les prestations ont été respectés sur toute la ligne. Pour citer un chiffre : aujourd’hui, nous consom- mons seulement environ 40 % de la quantité d’énergie requise autrefois. Nous économisons 60 %. Cela est éloquent. Et ceci nous aide également en termes de concurrence.
Ingo Staib // La restructuration sur une alimentation en matériau centralisée soulage également le personnel chargé du transport des matériaux. Ainsi, nous n’avons plus besoin d’espaces de stockage coûteux dans les halls et les erreurs de chargement sont également évitées. Et il fait bien plus propre dans la production.
Dans l’optique actuelle et avec l’expérience sur le long terme que vous avez, est-ce que vous feriez les choses différemment?
V. Mayer // En principe non. Nous sommes justement sur le point d’étendre notre production avec des presses d’injection jusqu’à 2 000 tonnes et la technologie multi-composants sur une parcelle adjacente. Ici aussi, motan-colortronic fera le suivi. Au final, motan-technique nous également aidé à convaincre les clients du haut de gamme de notre production. A la fin des visites guidées, nos visiteurs passent devant l’installation de séchage et nous leur démontrons directement sur la machine ce que nous faisons pour la qualité de leurs produits. Et cela porte ses fruits !