Preformas PET sustentables
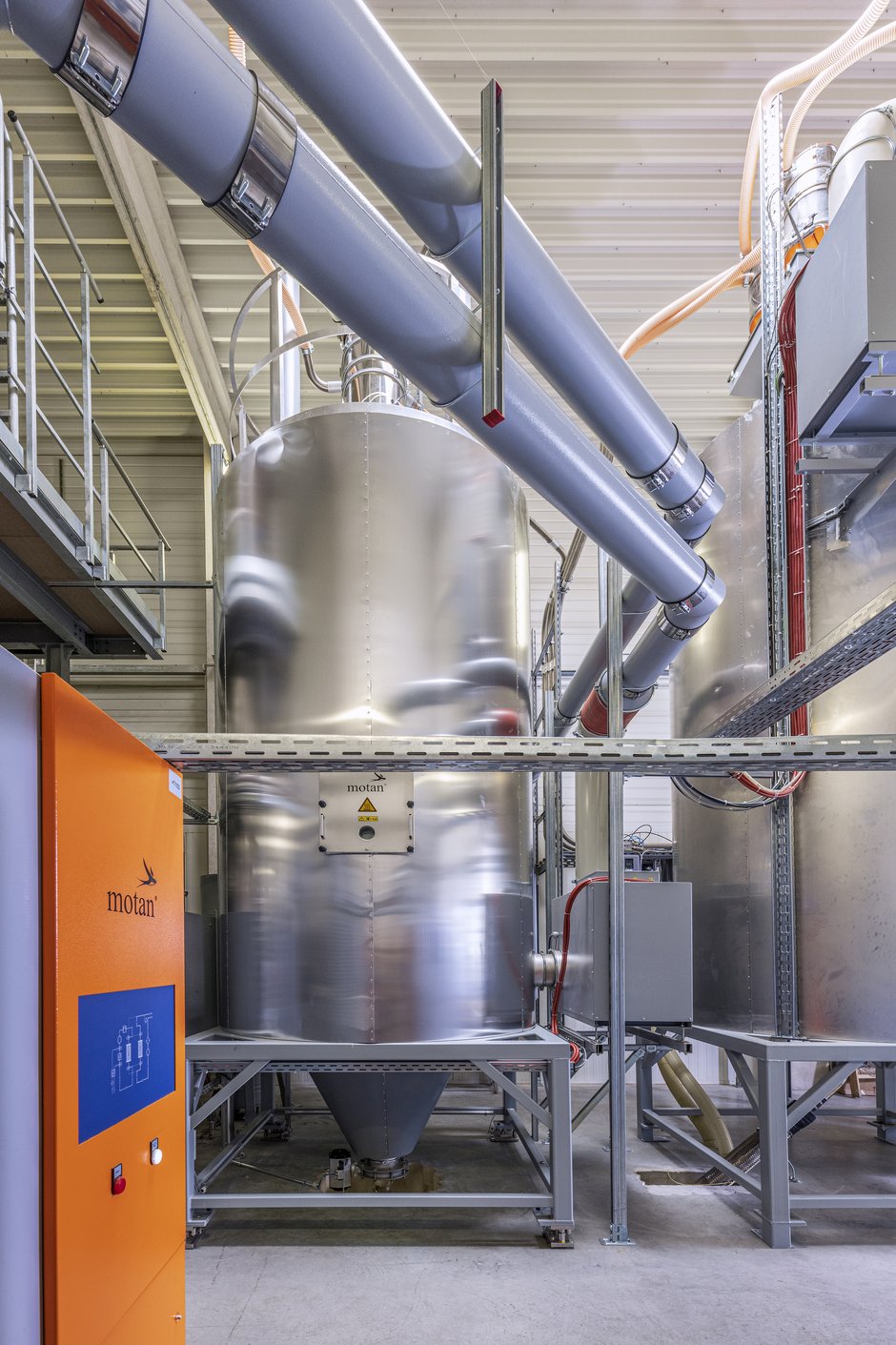
Reciclaje ante la escasez de materias primas
Las preformas se producen en dos lugares, Bruchsal y Kloster Lehnin, para las otras plantas del grupo. El paso de material es enorme: en el caso de los sistemas de moldeo de preformas por inyección, es de entre 830 y 1.300 kg/h, según el sistema. Sin embargo, los desafíos de la ingeniería de procesos se encuentran sobre todo en la preparación del material reciclado para el proceso de moldeo por inyección, los llamados copos o flakes de botella. Por un lado, tienen que ser seguros para alimentos y, por el otro, deben ser rentables a la hora de la compra y e procesamiento. Hace muchos años, Hansa-Heemann apostó al aprovisionamiento desde la economía circular con socios en el comercio minorista de alimentos para poder emplear un producto reciclado lo más puro posible. Sin embargo, debido a la gran demanda, esta estrategia está cada vez más cerca de alcanzar sus límites. Hoy en día, el material reciclado de alta calidad es una materia prima muy solicitada y escasa y no puede obtenerse gratuitamente.
Nuevos desafíos
El desafío más reciente de Hansa-Heemann fue el fenómeno de las botellas PET de paredes cada vez más delgadas. Las botellas de PET de paredes más delgadas resultan más económicas en la fase de uso de las botellas, pero implican un circuito de reciclaje más complejo debido a las cambiantes propiedades de la mecánica de los materiales a granel de los copos o flakes de botella producidos. Esto significa en concreto que el procesamiento del material en la fase previa al proceso de moldeo por inyección se torna considerablemente más exigente. Por ello, Hansa-Heemann decidió iniciar un proyecto de desarrollo de una planta piloto junto con motan-colortronic. El concepto de planta resultante fue implementado y probado in situ en la planta de Kloster Lehnin para una máquina de procesamiento. Al momento se destaca la capacidad de procesamiento deseada para la planta y convence a los involucrados.
El proyecto de desarrollo fue precedido por muchos años de cooperación entre las dos empresas en el campo del procesamiento de materiales. Los primeros contactos se tendieron en la K 2007. Por lo tanto resultaba lógico encarar el proyecto de los copos o flakes de botella juntos. “Tuvimos muy buenas experiencias con los anteriores sistemas motan-colortronic. Sin embargo, en el caso de los copos o flakes de botellas actuales, nos quedó inmediatamente en claro que tendríamos que abrirnos nuevos caminos junto con motan-colortronic”, afirma Ralph Möller, Director de Producción de Preformas de Hansa-Heemann.
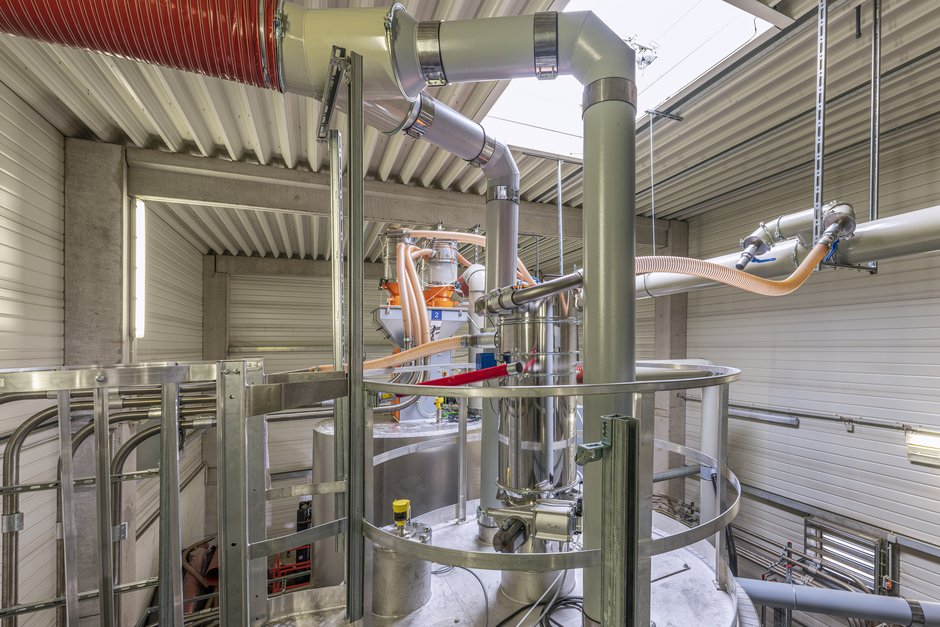
Mirar a los hechos de frente
Ralph Möller nota desde 2017 que los copos o flakes de botella actuales resultaban en cada vez más preformas defectuosas. No se detectó ningún error cuando se analizó la tecnología del sistema, por lo que se centró la atención en el material. Ralph Möller y su equipo descubrieron rápidamente que los copos o flakes de las llamadas “botellas ligeras” eran mucho más ligeros que en años anteriores. Por lo tanto, resultaban más compactas a granel, de modo que tanto las propiedades de flujo durante el almacenamiento y el transporte como el paso por la tolva de secado eran insuficientes para la tecnología del sistema existente. En consecuencia resultó inevitable emplear nuevos conceptos en el procesamiento de materiales, en particular para el secado y el transporte.
Evaluación de la estrategia básica
En el pasado, Hansa-Heemann ha logrado un gran éxito con los copos o flakes de botellas, lo que ha posibilitado lograr una proporción cada vez mayor de material reciclado en las preformas, mientras que se mantienen las propiedades requeridas para el proceso de soplado y llenado así como las propiedades de barrera del producto acabado. Por un lado, esto encaja con la estrategia corporativa de la empresa y, por el otro, asegura el éxito económico.
“Esta estrategia básica no era el problema, sino que debería seguir siendo parte de la solución”, dice Ralph Möller. El proyecto de desarrollo con motan-colortronic tenía un objetivo simple y claro: ¿Qué estrategia permite procesar de forma confiable los copos o flakes de botellas más ligeros y pequeños en preformas de PET con una proporción de copos o flakes de menos 25 %?
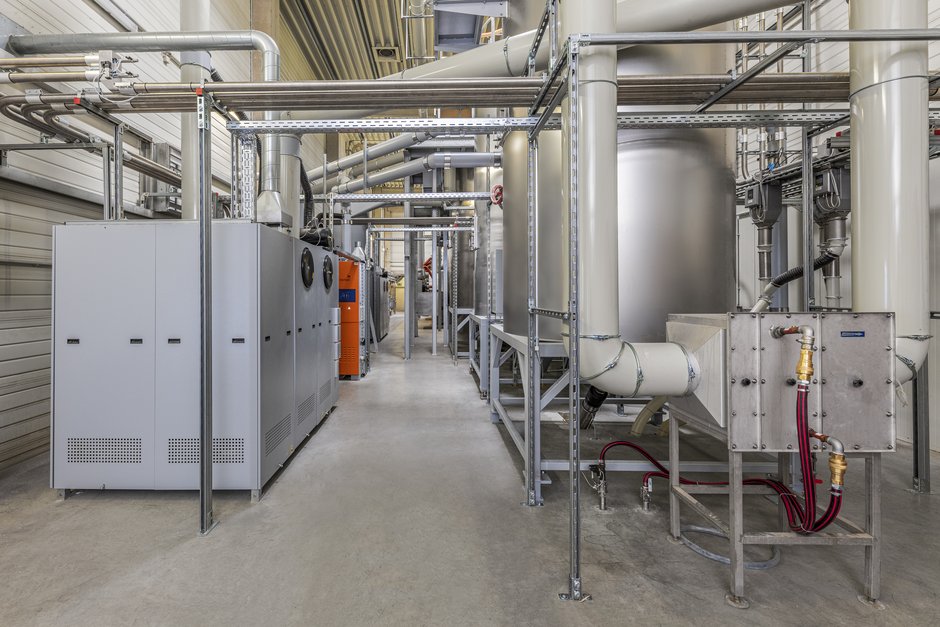
Recorrer nuevos caminos
Las investigaciones preliminares en motan-colortronic han demostrado que los copos o flakes de botella utilizados tienen un grado de cristalización lo suficientemente alto, de que en general se pueda prescindir de un paso de cristalización. El factor clave fue el cambio en la mecánica del material a granel y los correspondientes cambios en las propiedades de almacenamiento y flujo.
Por ello, el departamento de aplicaciones de motan-colortronic desarrolló un nuevo diseño para la estructura interna de la tolva de secado, en la que se optimizó el suministro de aire para el material mediante una geometría modificada. Para ello, se realizaron pruebas en Isny, que tuvieron éxito desde el principio. El resultado es un mejor flujo de aire a través de los copos o flakes ligeros, lo que aumenta significativamente el rendimiento de secado y reduce el daño al material. El secado de los copos o flakes de botella es ahora mucho más homogéneo. La geometría especial de la tolva de secado también evita la formación de puentes en el material.
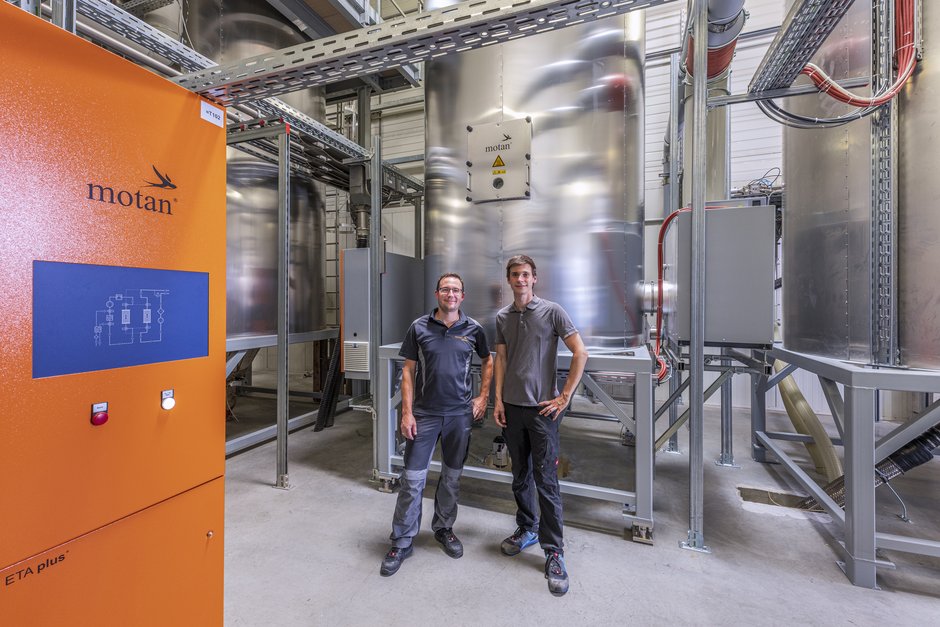
Revisar el sistema complet
Después de encontrar una solución exitosa para el proceso de secado, los expertos de motan-colortronic revisaron el concepto general del sistema existente y lo adaptaron al nuevo material de reciclaje. La logística de almacenamiento de la planta de Kloster Lehnin se complementará con estaciones de alimentación para los copos o flakes de botella entregados en Big Bags. El suministro de material para el transporte neumático se realiza en contenedores y cajas de aspiración adaptadas al material. Dado que en la planta se ha instalado un sistema de aspiración central permanente de motan-colortronic con suficiente rendimiento, la distribución de material se puede realizar a través de una estación de acoplamiento, de modo que posteriormente también se pueden integrar otros sistemas en el suministro de material.
El sistema de tuberías y el equipo de transporte de la tolva de secado también están diseñados para las propiedades específicas del material de los copos o flakes de botella. En este caso se utilizó el nuevo METRO G para grandes pasos de material y copos o flakes, que fue equipado con una compuerta de eyección extra grande. Dado que la geometría de la tolva de secado asegura una salida pareja del material y evita la formación de puentes, no se requiere el apoyo mecánico durante la remoción del material. El contenedor se instala en una plataforma encima de la máquina de procesamiento y se conecta a ella a través de una manguera de caída. Justo encima de la entrada de material de la máquina de procesamiento se encuentra una unidad de dosificación y mezcla volumétrica en la que, al igual que en los sistemas anteriores, se combinan los flujos de material virgen y reciclado.
Pruebas exitosa
Las primeras pruebas in situ con la planta piloto descrita fueron exitosos. Para el futuro, se prevé convertir paso a paso todos los sistemas al nuevo concepto. “Esto podría proporcionarnos nuevos impulsos y estándares de rentabilidad, sustentabilidad e intensificación de la economía circular para poder mantener nuestra competitividad”, espera Ralph Möller.
marca de calidad RAL para el reciclaje de PET en envases de bebidas
Los productos y métodos de producción sustentables forman parte de la filosofía de Hansa-Heemann desde hace muchos años. Ya en 2014, la empresa recibió la marca de calidad RAL como una de las cuatro empresas pioneras en el envasado sostenible de bebidas en PET. La marca de calidad RAL es otorgada por la Gütegemeinschaft Wertstoffkette PET-Getränkeverpackungen e.V., con sede en Bad Homburg (https://www.wertstoff-pet.de/).
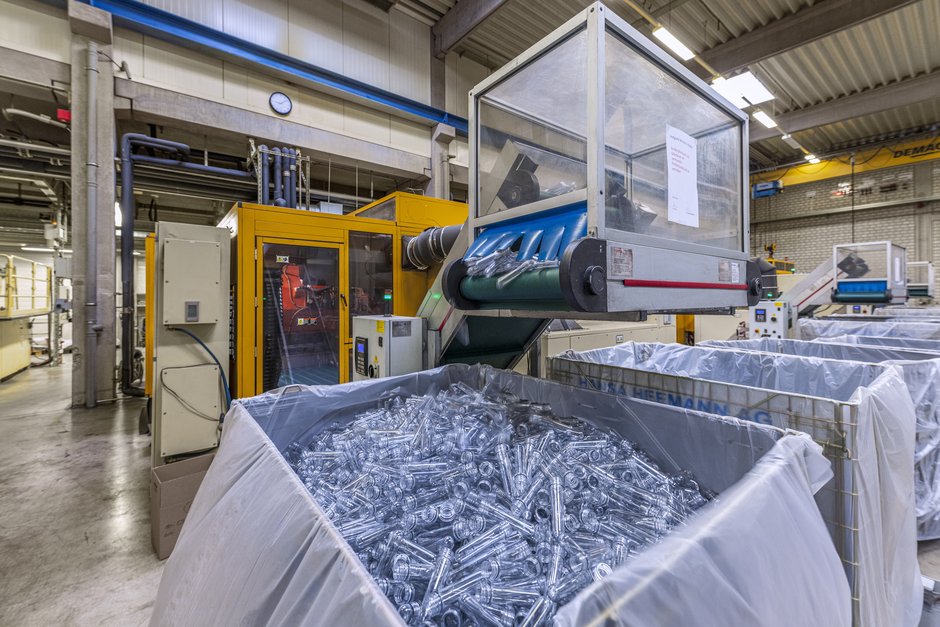
Sobre Hansa-Heemann
Hansa-Heemann AG es uno de los principales proveedores de agua mineral y refrescos en Alemania desde hace más de cuatro décadas. Entre las marcas de la empresa se encuentran Hella, Fürst Bismarck Quelle y St. Michaelis. Además de su sede central en Rellingen, cerca de Hamburgo, Hansa-Heemann cuenta con plantas en Aumühle, Trappenkamp, Kloster Lehnin, Löhne y Bruchsal. En 2018 se produjeron y vendieron aproximadamente 2 mil millones de litros en los centros de producción. El volumen de ventas anual de aguas minerales, refrescos, bebidas para deportistas y bebidas energéticas, así como de jugos de frutas asciende a unos 300 millones de euros. La empresa emplea a unas 850 personas y es actualmente la segunda fuente mineral más grande de Alemania.