motan innovation award 2018
This is the motto of the motan innovation award (mia), which motan issues every two years. An independent expert jury has reviewed and evaluated the numerous submissions. Six particularly innovative ideas made it to the final round and are nominated for the mia 2018. The award ceremony will take place on 18 October 2018 during the FAKUMA at the Dornier Museum in Friedrichshafen. These are the nominees:
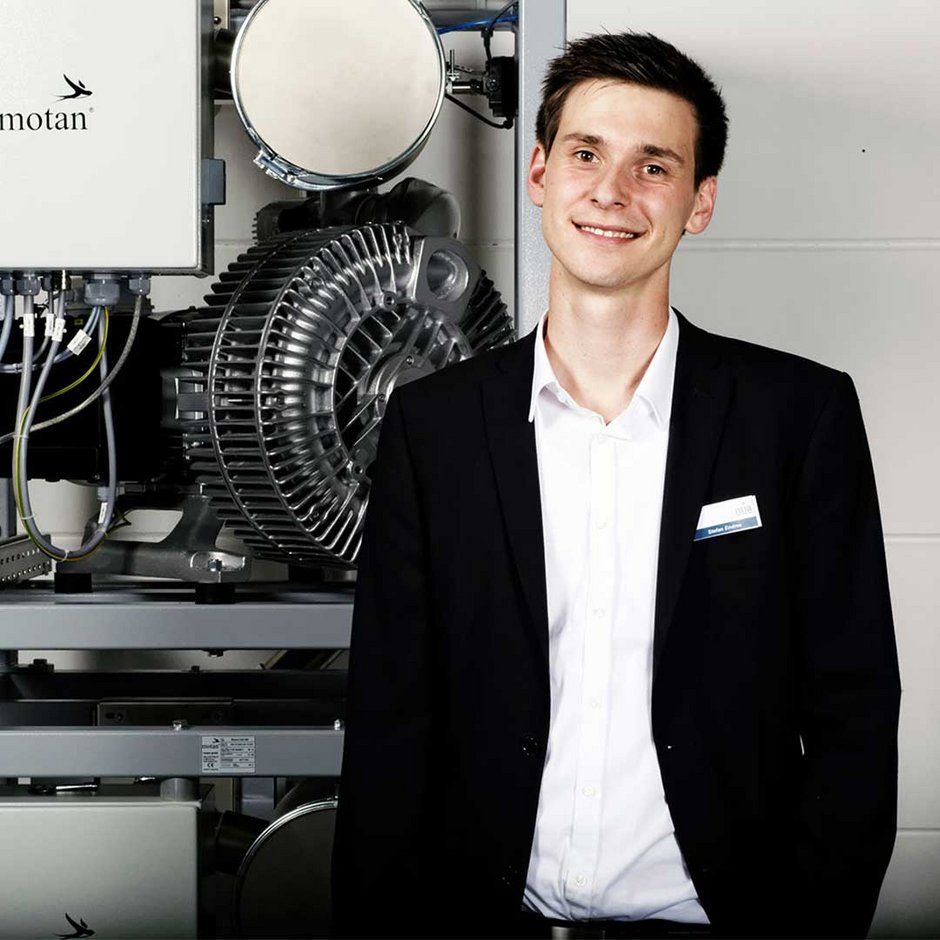
Adaptive central vacuum control
More efficient plant utilization and higher production reliability
With the adaptive central vacuum control, the simultaneity factor of the active conveyors is included even more in the process and thus an adjustment can be made depending on the production utilization. This increases energy efficiency, protects the equipment and enables material-saving production.
Stefan Endres (27) completed his training as an electronics technician for energy and building technology at the state vocational school Kempten. In 2013, he founded his own company ‘Endres Industriedienstleistungen’, where he is managing director and owner until today. Privately, Stefan Endres likes to climb and is interested in motorsport.
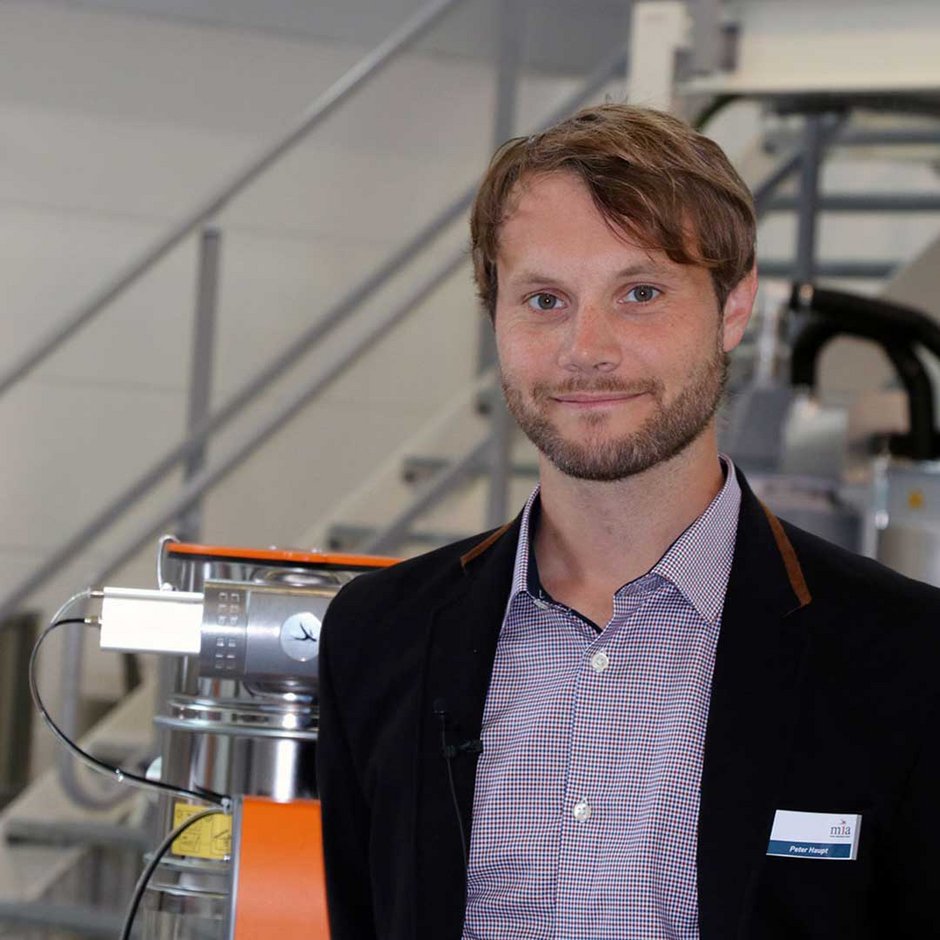
Regulated conveying of bulk materials
Conveying speed measuring and process optimization
The conveying of bulk material is often disturbed by external influences, as these are not automatically detected and corrected. The idea of Peter Haupt aims to measure the material velocity of the bulk material in real time with the help of a sensor and to adapt the blower speed with this knowledge. So, it is possible that the bulk material always moves with the optimum speed of the respective material in the pipes. For this, neither a complicated additional tool is necessary nor is the material flow impaired.
Peter Haupt (33) started as a Bachelor of Engineering at motan in equipment engineering. From 2011 to 2014 he was with the motan-colortronic project manager for Lego. Since 2015 he has been development engineer and project manager in dosing and mixing. His hobbies include mountain biking, skiing, football and tennis.
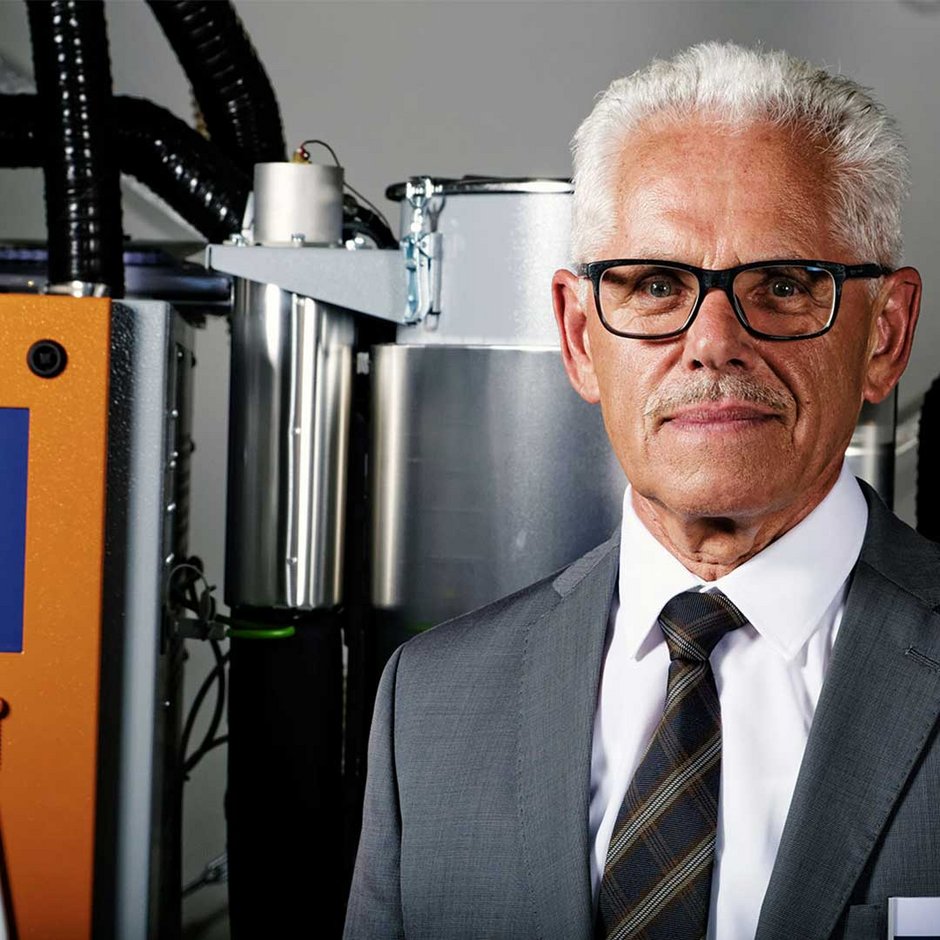
The GAK system
Automation, control and monitoring of suction conveyor systems
The newly developed GAK system (gravimetric suction box) records all machine throughputs directly at the material source and thus replaces the measuring process at the consumer (machine). By means of a gravimetric dispenser integrated in the suction box, each delivery batch is weighed individually before aspiration and then selectively assigned to the operated machine. This weighing system opens up completely new possibilities for the control and monitoring of suction conveyor systems, since many processes are automated. The increase in the degree of automation is also accompanied by an increase in the reliability of the systems.
Reinhard Herro (68) is a state-certified engineer specializing in electrical engineering and a trained business economist. He joined motan in 1979 as a manufacturer and developer of electronic controls, and held various executive positions in the company until 2015. Most recently, he was responsible for technical marketing. He has been retired for three years now. Privately Reinhard Herro likes to travel and hike.
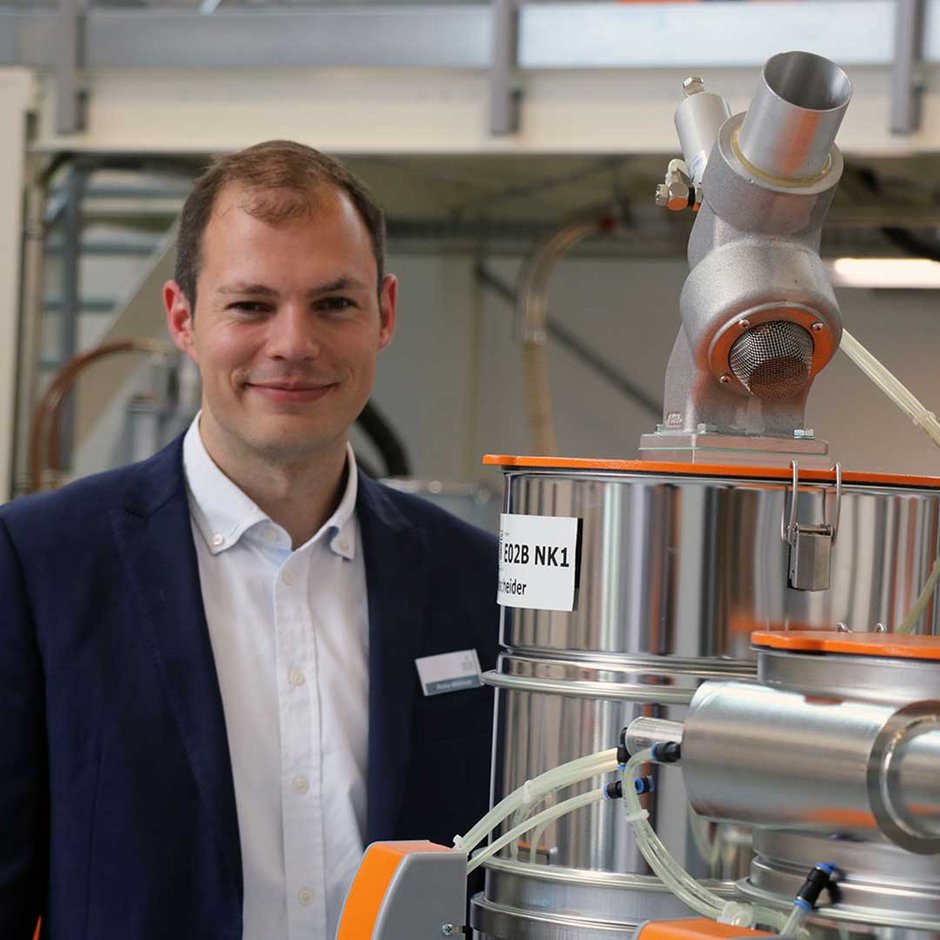
Plant control on mobile device
Query status information specifically via QR codes
To be able to serve plants optimally requires a quick and precise retrieval of the current status information. With the new app by Philipp Mählmeyer even an inexperienced employee is able to query status information with a mobile device via QR codes and control the actuators accordingly. For example, incorrect mixtures in formulations can be prevented.
Philipp Mählmeyer (29) graduated in 2015 with a Master of Science in Computer Science and is currently the Managing Director of pmb Software. Since 2009 he is also working as a freelance software developer. In his free time, he likes to take pictures and play tennis.
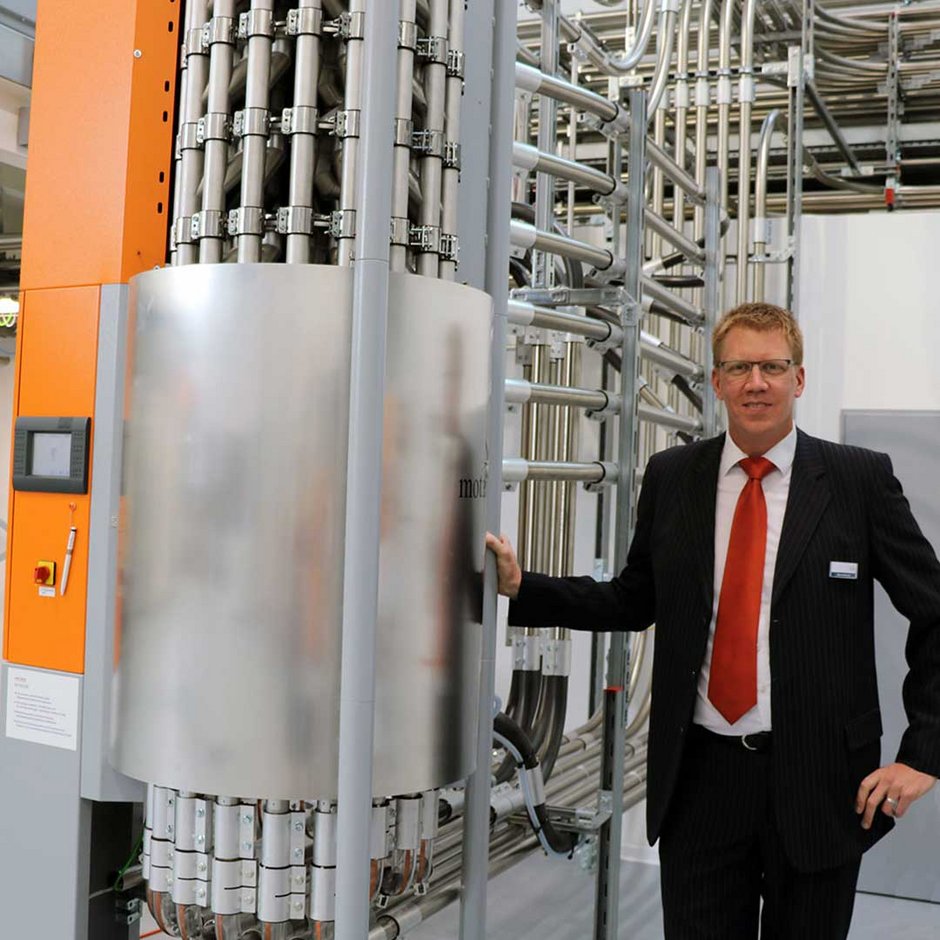
The METRO-Lay system
Efficient creation of routes for material and vacuum lines
Supply lines can be created more efficiently with the new, highly flexible “METRO-Lay” system. It significantly reduces installation times, reduces assembly costs and thus increases the project margin. Even valuable human resources can be spared by the comprehensibly structured system.
Bernd Michael (46) studied mechanical engineering and process engineering at the FH Niederrhein in Krefeld. He began his career in 1997 at the motan site in Isny. Today he is Sales Manager for Southern Germany. Privately, Bernd Michael is interested in model making, among other things.
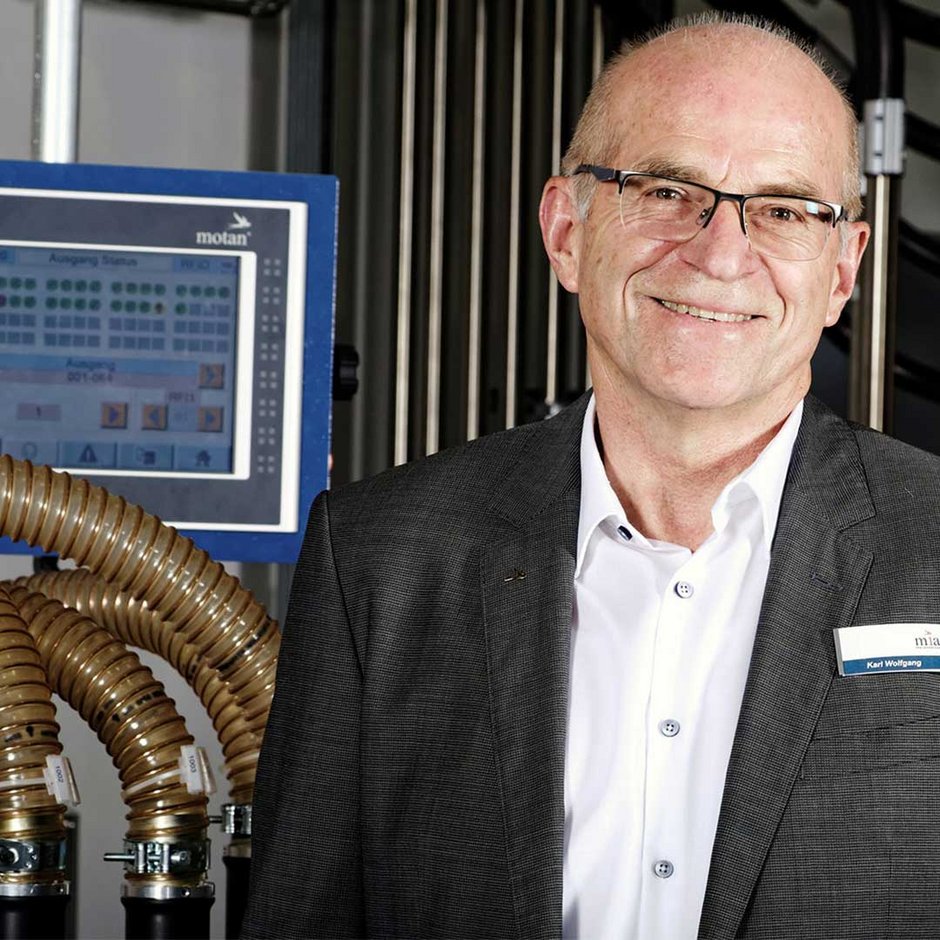
The Repeater
Material-protection conveying in the vacuum area
The new development “Repeater” is a so-called conveying support. The idea is to subdivide the flow line once or twice, but with the help of the repeater, this does not interrupt the routing and the conveyance. In this way it is possible to convey material over long distances and high throughput rates. The advantages of this material-saving conveying also includes lower material and equipment wear and low investment costs.
Karl Wolfgang (61) is a state-certified mechanical engineer with additional training in PLC control technology and project management. At motan he started in 1981 as a project developer. Today, he heads the conveying and storage department at motan holding. In his free time, you can find Karl Wolfgang in his garden and on his bike.
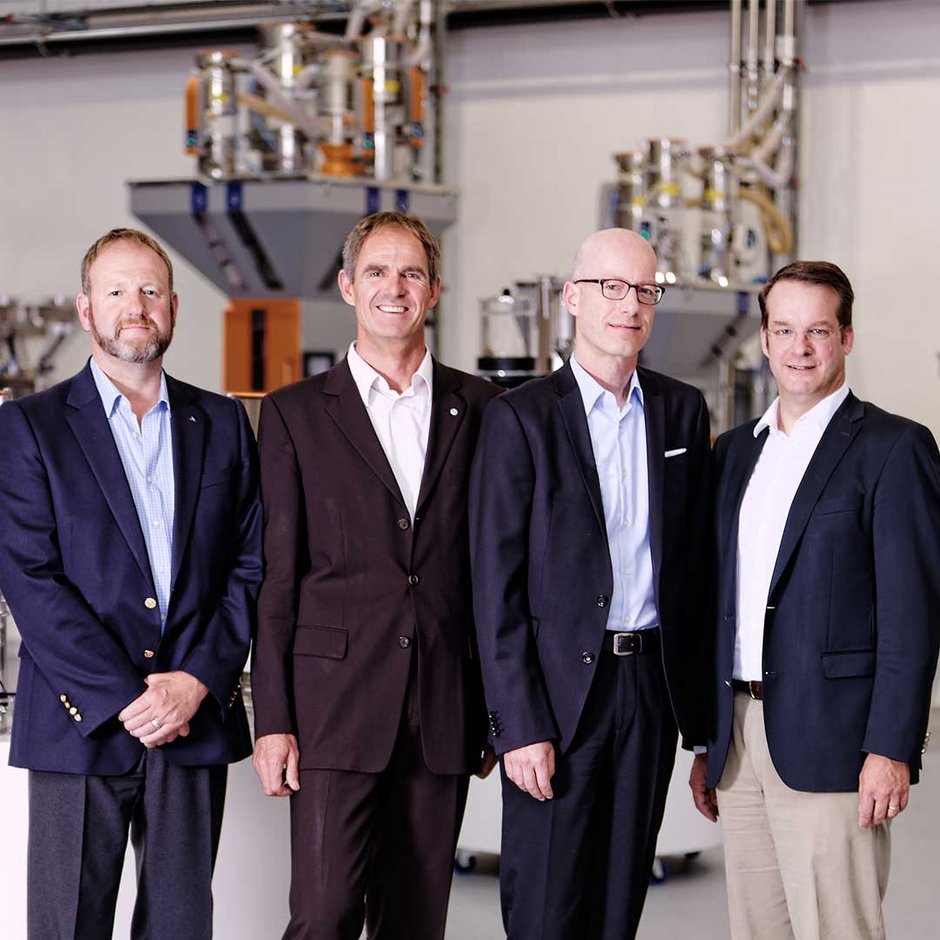
The jury
An independent jury of renowned experts, who have immense theoretical and practical knowledge in plastics manufacturing and processing, decides on the best innovation.
Left to right: Karl Miller started at Colortronic in 1987 as Technical Sales Engineer and today manages motan-colortronic Ltd. in England.
Prof. Dr. Martin Bastian has been since 2006, Institute Director at SKZ in Würzburg, the largest plastics institute in Germany.
Dr.-Ing. Peter Faatz was a professor of plastics technology and since 2005 has been in charge of the process development for plastics technology at INA Schaeffler plant.
Prof. Dr.-Ing. Christian Hopmann has been the Head of the Institute for Plastics Processing (IKV) in industry and trade at RWTH Aachen since April 2011