motan-colortronic with focus on "Smart manufactory" at Chinaplas 2021
The lack of skilled workers and the demand for increasing efficiency among manufacturers in the plastics industry are increasing worldwide. At the end of the day, the only solution left for many manufacturing companies is Industry 4.0, the networking of all plant components and the complete automation of their plants from material supply to packaging and shipping of the end product as a solution for increasing the efficiency of the entire production in order to promote business growth.
It is precisely one of these points that motan picks up on with its materials management products. When we talk about an intelligent materials management system, we are not just talking about a simple material feed system.
In the Industry 4.0 factory of the future, an additional adsales trade booth, motan, ZGY smart cloud, china unicom and black lake showed how production data and manufacturing system can be connected and visualised with materials management. Among other benefits, this makes it possible to save on energy consumption and materials and to ensure the stability of production.
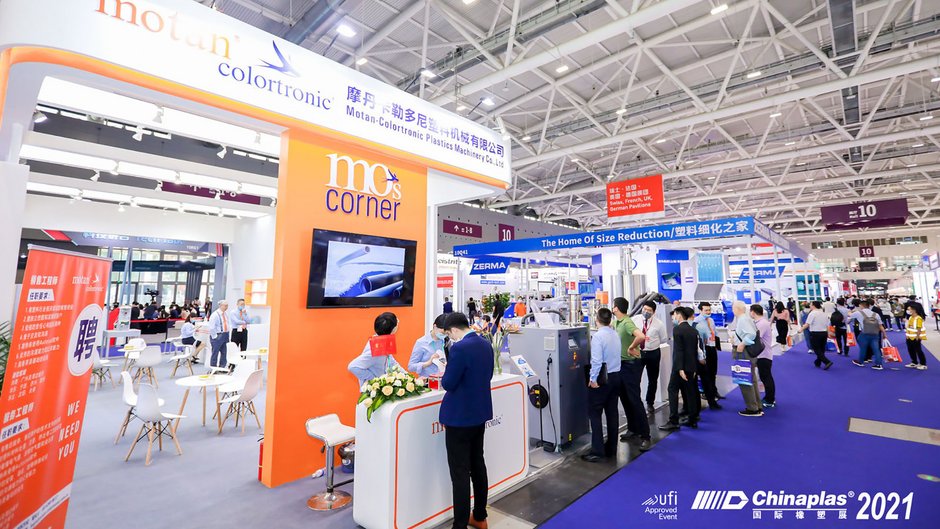
With an additional Industry 4.0 dashboard at the motan-colortronic stand, the topic of “smart manufacturing” was again taken up. Here, however, it was visualised and implemented with the new “motan swift” product range in combination with injection moulding machines from Arburg, Engel and KraussMaffei. In this context, motan focuses on three themes. On the one hand, the product compatibility and high automation of the motan units, which were placed in three exemplary production lines in other exhibition halls. The units themselves supplied real-time data to a visualisation software for production data directly on the dashboard at the motan-colortronic stand.
The focus of product development at motan is on the graphic visualisation of production and device data, so that potential problems in the production line process can be quickly displayed and detected visually by the users. This results in optimised human-computer interaction and overview across the entire production line. Faster reaction times and preventive warnings in the event of or before errors in the system means at the same time shorter downtimes and predictive maintenance, so that these can even be avoided completely.
On the other hand, the connection of all system components via IoT and the graphical visualisation can also quickly identify weak points and optimisations in the system. There are several advantages for the use of such data evaluations:
- Energy efficiency increase of the plant,
- conservation of resources in material consumption,
- improved end-product quality
- higher production efficiency and throughputs.
Due to the internet capability of the entire system and data management systems and visualisations via WIFI, standard web technologies can be used that have already been used in the consumer sector for many years. This enables access to the data visualisation and control of the system via app conveniently on mobile devices and completely independent of location. Data acquisition and storage usually take place on a central PC, server or, if available, cloud-based storage.
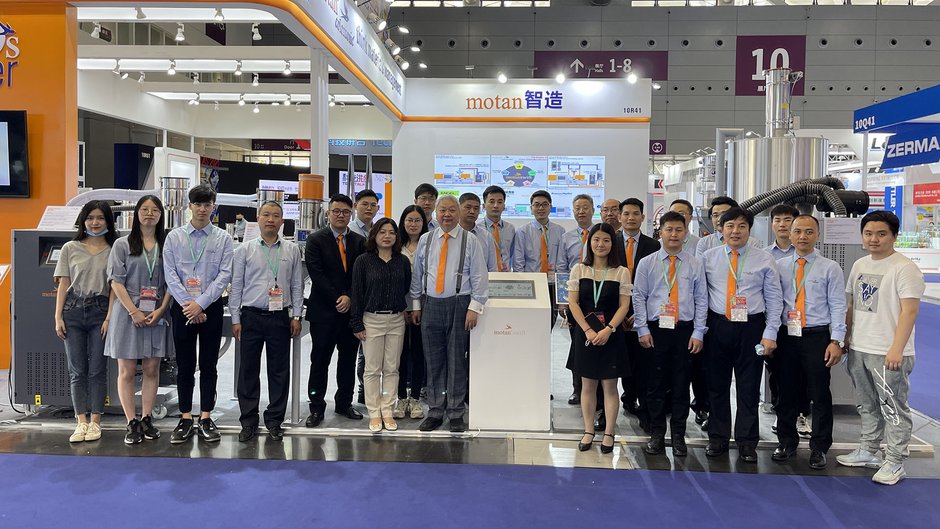
The presented pilot factory “Industry 4.0-Factory of the Future” was part of the adsales partner programme for the second time after 2019. For motan-colortronic itself, it was the long-awaited restart for exhibitions. Despite the tough quarantine guidelines in China for visitors entering the country, motan-colortronic recorded a good number of visitors. Although the numbers of previous years could not yet be achieved, this was a successful start for an almost purely Chinese exhibition after more than a year without a major “presence exhibition”. The new product line motan swift with a very good price-performance ratio generated a lot of interest among the stand visitors.