Kat Mekatronik
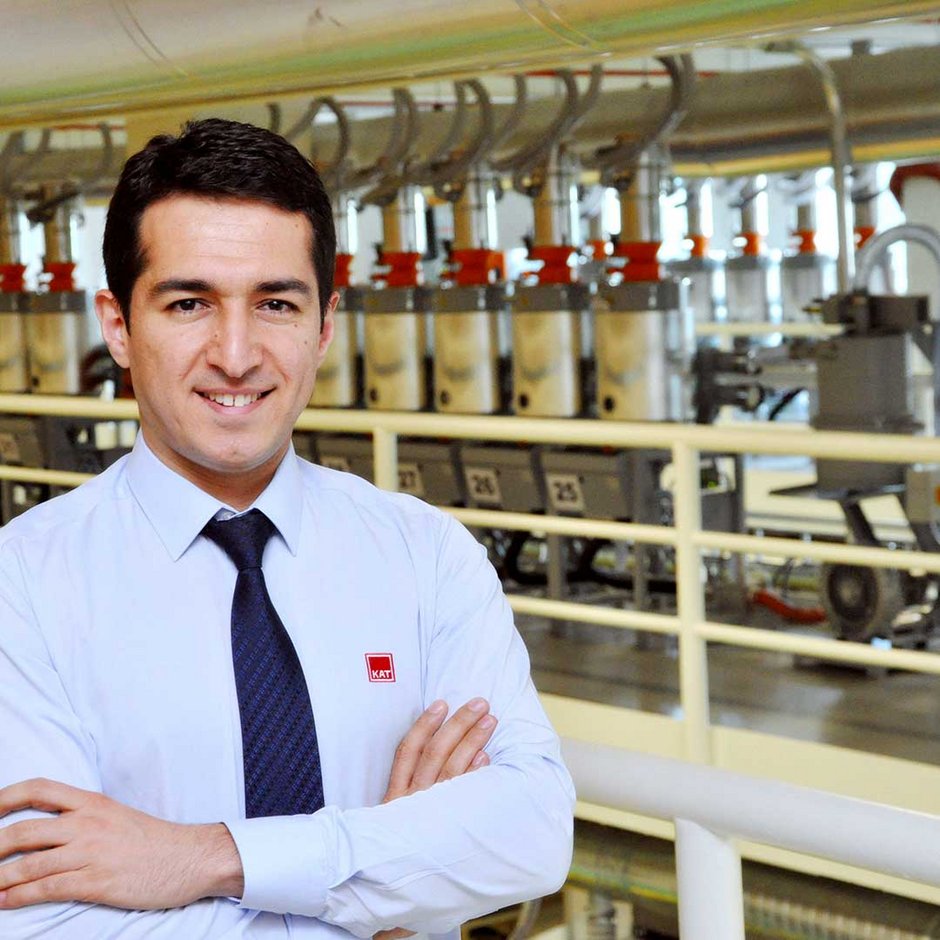
Mr. Mehmet, could you briefly introduce yourself and your company?
Our company was first established in 1955 and produced accessories for electrical household appliances, with the first factory founded in Ortakoy. Later, we started manufacturing for the telecommunication and automotive industries with new product ranges. As our product ranges increased, we moved from Ortakoy to Levent and then expanded our production facilities with a factory in Ikitelli. Today, we manufacture in this very building here in Catalca.
WE changed our company’s name to Kat Mekatronic when we moved to Catalca Free Zone and today, we manufacture products for the telecommunication infrastructure, and automotive industries.
Our telecommunication infrastructure products include connection modules and connectors. Our company also manufactures mechanical and electro-mechanical products such as connectors, switches, indicators, and buttons for the automotive industry – an industry for which we have been producing for the last 20 years. Our company has created new product ranges for passenger cars in the last five years and now we manufacture higher quality and more technically advanced products.
I have been working for the company for about 10 years. I started as a production engineer and have been working as production manager for the last 5 years. I am responsible from the processes where raw materials, or semi-products, are made into main products at the factory.
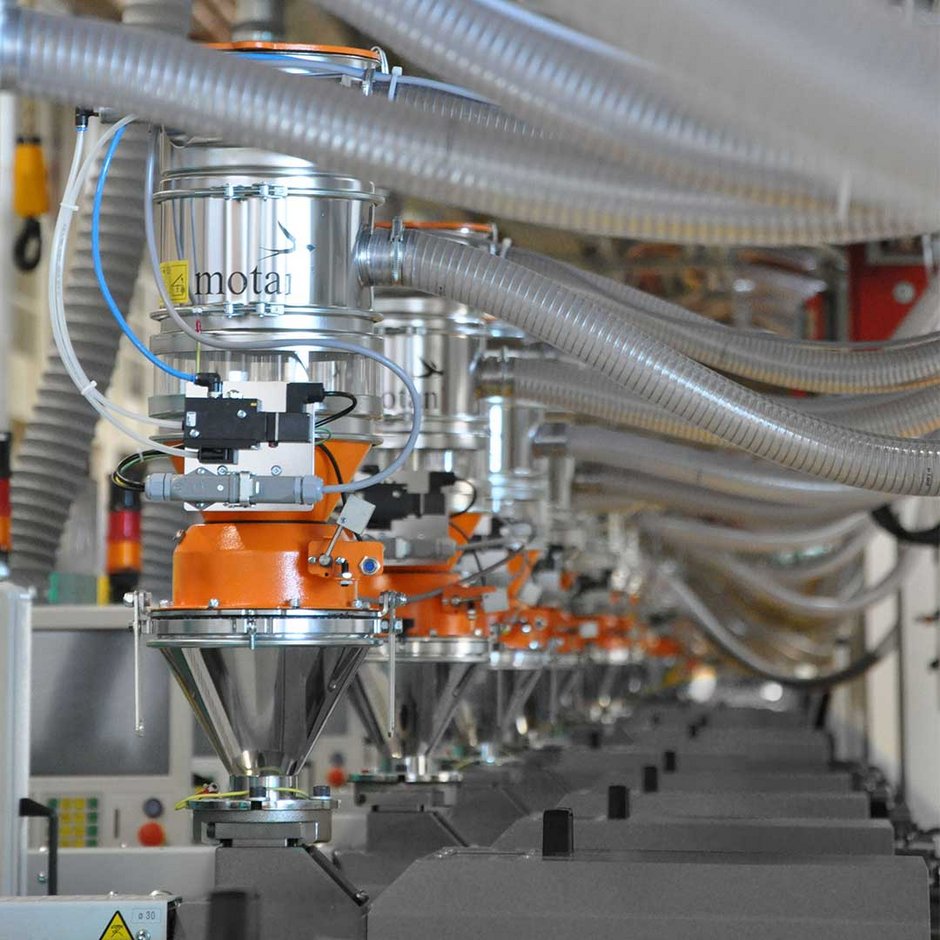
Speaking of different product ranges, I understand that you are completely focusing on motan-colortronic products for materials management. Do you have any special reasons for such a preference? Why do you prefer motan?
Yes. As I have mentioned, we manufacture for the automotive and passenger car industries, which both require incredibly high quality products. Our raw materials, workmanship, and manufacturing equipment must therefore also be of the highest quality.
We have invested in specific technology at our new factory in order to increase the quality of our products and the quality of the technology we already had there. motan is one of these technological investments.
To increase the quality of our products, each step of every single process the raw material undergoes has to be monitored and tracked in minute detail, and the entire process has to be continuously analysed and assessed. This is a reason why we chose motan. They fulfil all our needs in this respect.
Has motan-colortronic fulfilled all your technical demands? What kind of initial requirements did you have that made you chose motan-colortronic?
We talked with many different companies before investing. We compared products from 4-5 different European companies and made in-depth inquiries since we had very high requirements and expectations. We had previously been encountering some problems and, we specified these during our inquiries to prevent them from recurring and to obtain better results in the future. We had been having problems in follow-up drying of raw material. Raw material was either far too dry or used before it had been dried adequately. We needed a solution to this problem and motan found one quickly.
Previously, we had been entering drying set values for each raw material manually for each process, which often resulted in faults in the drying process. We specified that we needed a database that enables us to enter and then select the drying parameters for the different raw materials as set by our engineers. We also wanted the most energy-efficient drying system as possible. motan delivered an extremely satisfactory solution, so choosing motan was not a difficult decision.
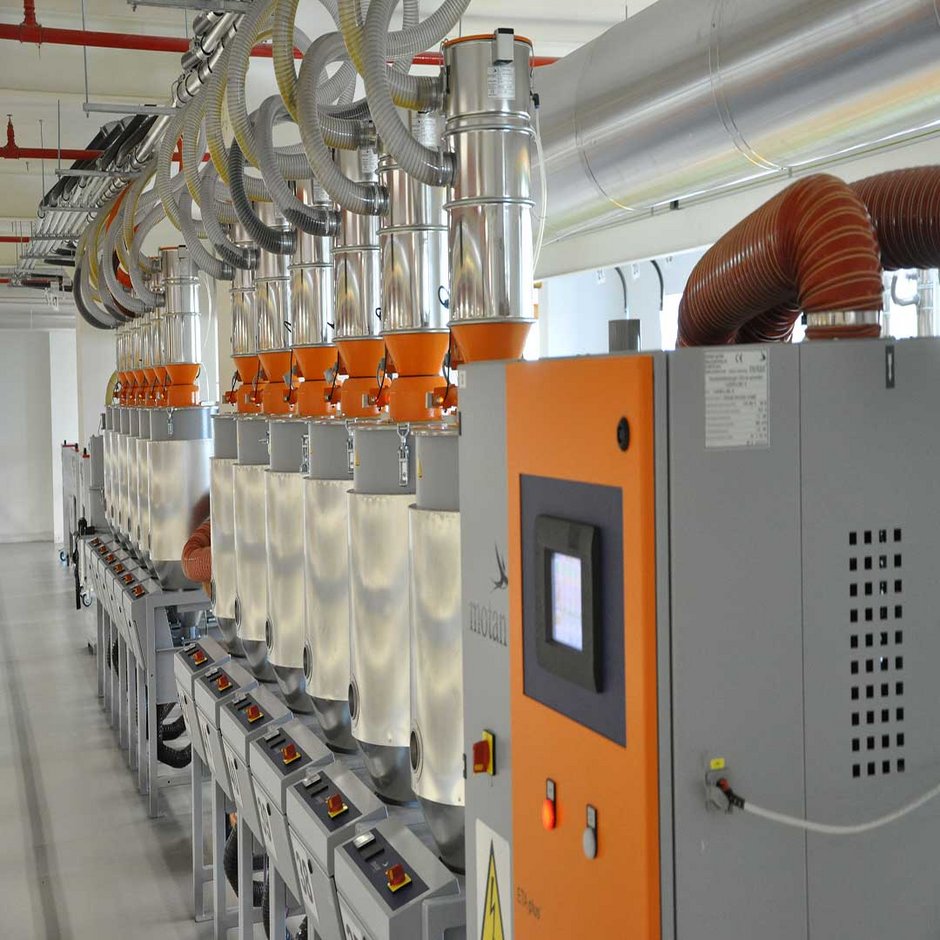
Do you believe that your investment in motan products has paid off?
Yes. Our energy consumption has decreased dramatically and we have not encountered any of the previous problems during drying.
Finally, is there anything that you would like to add?
At Kat Mekatronik, we believe in constant improvement. In order to achieve this, we invest in new technology that helps us provide sustainable quality. We would like to thank Tepro/T-Max for offering us the opportunity to work with motan. We wish them continued success with providing the industry with hi-tech equipment.
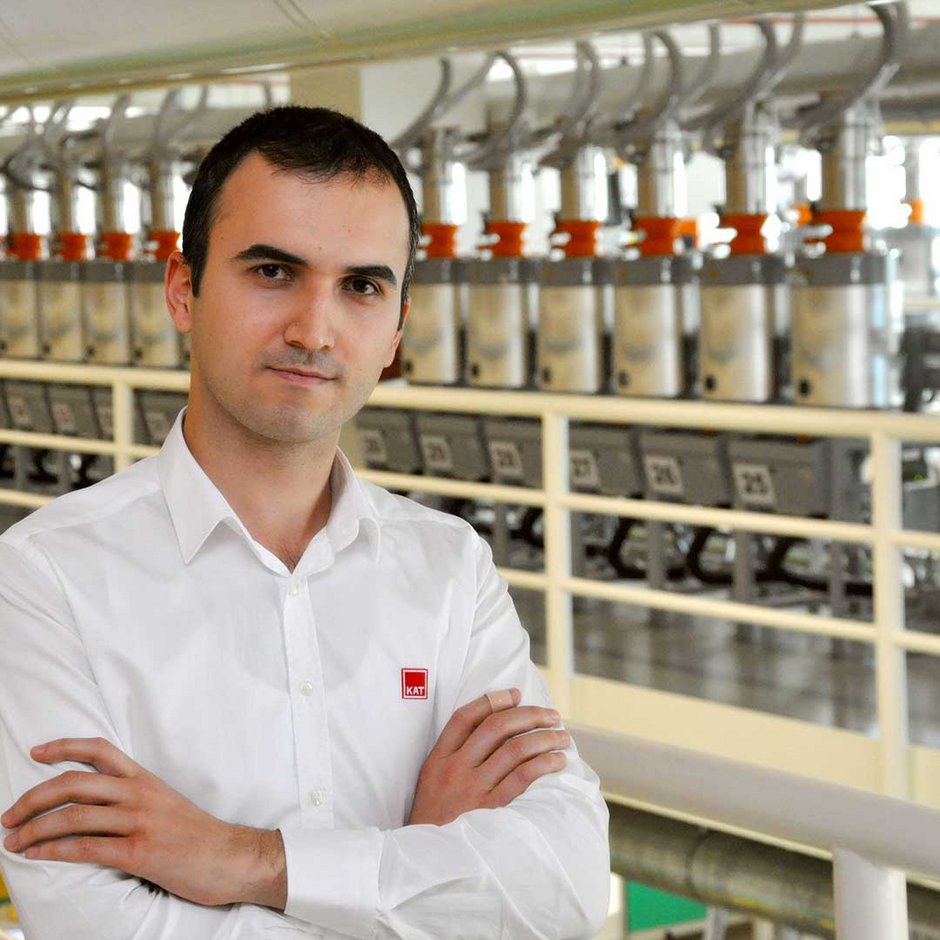
Could you please briefly introduce yourself?
My name is Burak Aslan and I am senior mechanical engineer. I began working for Kat Mekatronik when the new factory was established. I have been working as a production engineer for semi-finished products for Kat Mekatronik for about a year now. I am responsible for both the plastic injection-moulding and metal parts departments.
Could you tell us about the processes in the departments that use motan products?
Our production consists of two floors. We organise raw material and manage materials on the upper floor. Our processing machinery is on the lower floor. Raw materials arrive after being ordered from the warehouse through an IRP system, which we use throughout the company. At the preparation department, raw materials are filled into portable motan containers according to production order and are then connected to the drying bins. After this, the required material is selected according to the respective recipe and the drying process starts. Once the material is dry, the injection-moulding machines downstairs prepare for production.
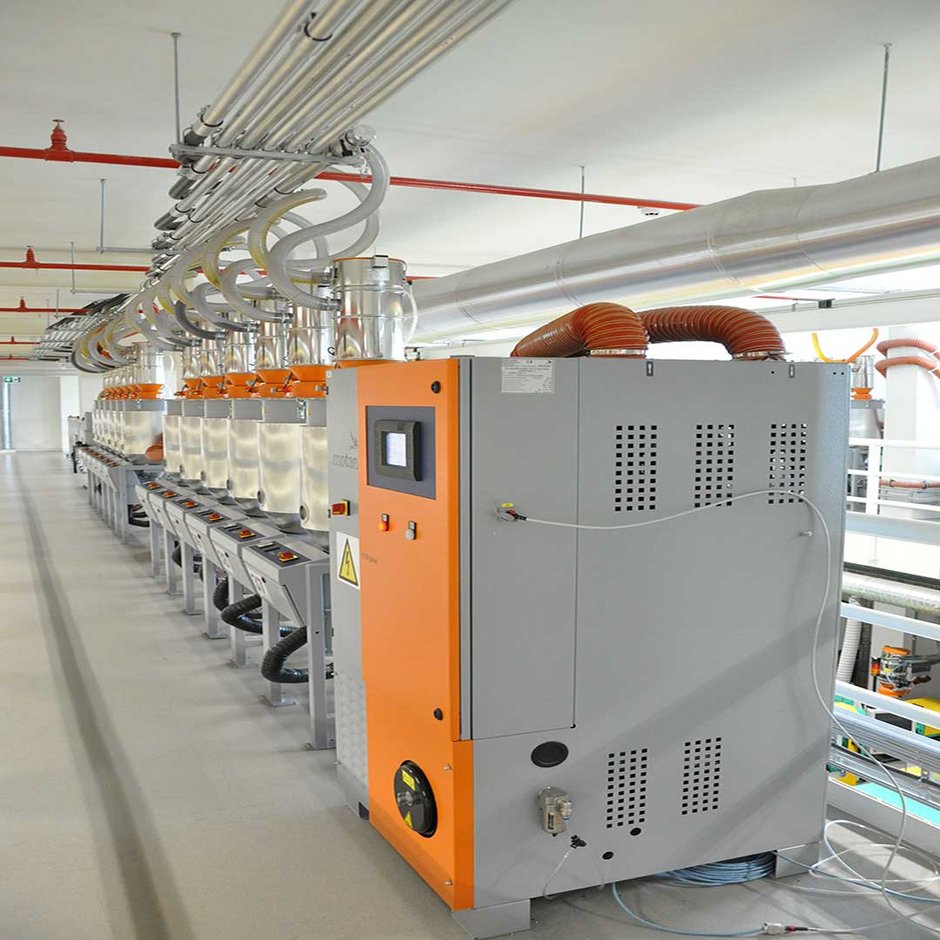
Do you think the services offered by Tepro/T-Max were efficient?
While we did not encounter many problems, Tepro/T-Max supported us 24/7 when needed. In addition to technical services, they also supported us with training, which allowed us to improve ourselves and effectively use our motan products.
Finally, is there anything you would like to add?
motan has really helped us increase the quality of both our processes and products thanks to its technological contributions. More importantly, they have helped us engineers improve our skills with their technical support.