Four ideas for mia 2016
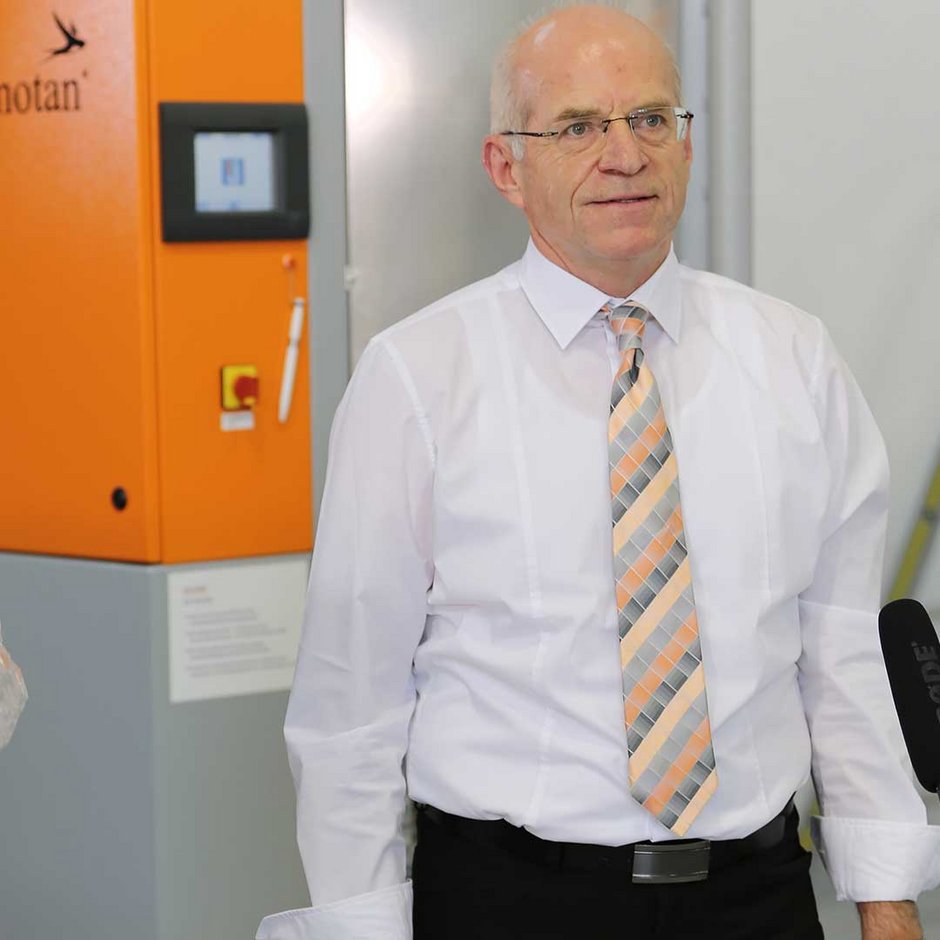
Inductive heating
Energy transmission through radiation
Octabins are widely used as delivery packaging for plastic granules. They are usually emptied in production with an automatic conveyor system. However, material residues often remain in the corners and have to be extracted manually. A new development automatically conveys these residues to the center of the octabin, where they can be removed without difficulty.
Karl Wolfgang (59) is a state-certified mechanical engineer with additional training in PLC control technology and project management. He started at motan in 1981 as a project processor. Today, he is in charge of the Conveying & Storage division at motan holding.
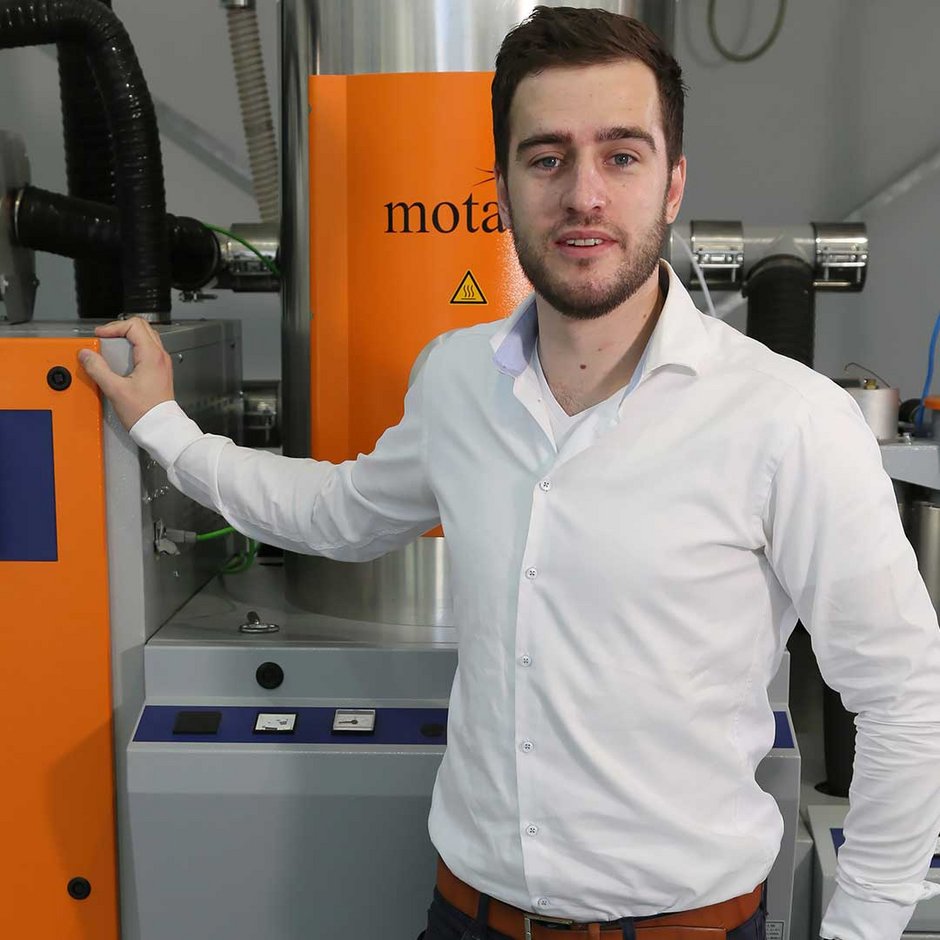
Inductive heating
Energy transmission through radiation
Nowadays, pre-heated, flowing drying air removes humidity from the plastic granulate. A new type of automatic drying is based on energy transfer through radiation. Very efficient and precisely controllable – these are the advantages of an idea which was born of the search for a dew point sensor system.
Fabian Kienzler (26) studied mechanical engineering at the University of Applied Sciences in Constance and today is the Regional Sales Manager at PRIAMUS SYSTEM TECHNOLOGIES AG Schaffhausen with responsibility for the regions Switzerland, BeNeLux and Scandinavia. He developed the idea of inductive drying together with Arnulf Hörtnagl (32), Marc Hiefer (26) and Oscar Lattner (26) in his time as a research assistant at the Institute for Material Systems Technology, Constance/laboratory for plastics technology, where he worked until 2015.
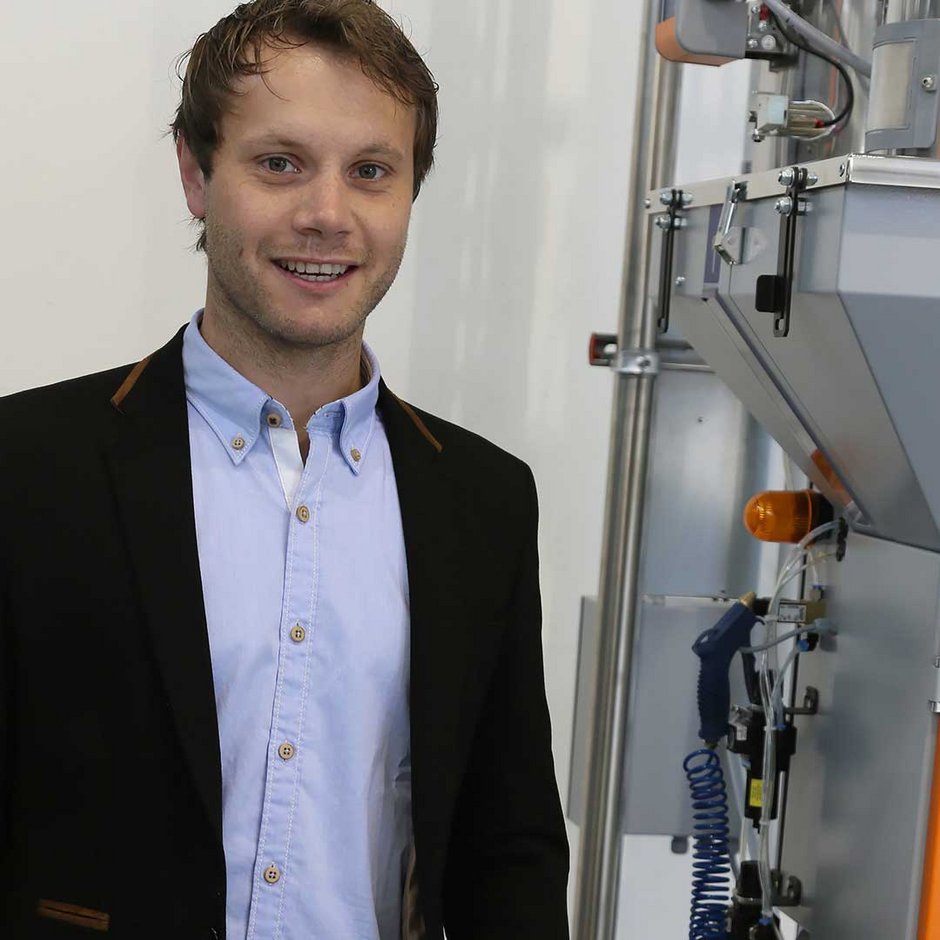
The dry doser
Recycle energy for drying and dosing
Hygroscopic plastics must be dried before processing for many applications. The idea is aimed at recycling energy in the areas of dosing and drying and considerably reducing total energy consumption. In addition, work can thus be more ergonomically designed.
Peter Haupt (31) began at motan in 2009 as a Bachelor of Engineering. From 2011 to 2014, he was the Project Manager for Lego at motan-colortronic. Since 2015 he has been responsible as the Group Engineer for dosing and mixing. In his private life, Peter Haupt likes walking and cycling in the countryside.
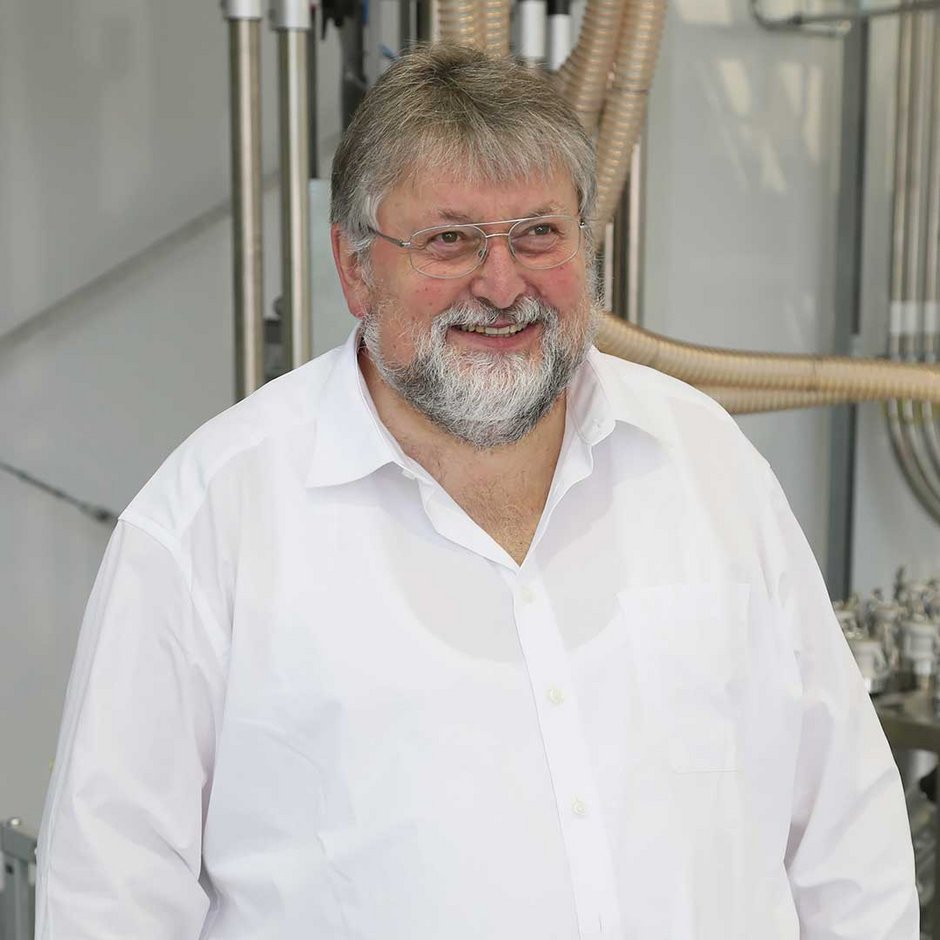
Matrix coupler
Automatic material station for small hopper loaders
When changing materials, conventional material stations require manual switching of the hose leading to the hopper loader. The matrix coupler automates the material allocation with a newly designed multiple separator. In this way, contamination of the adjacent lines is prevented. This is practical, low cost and innovative.
Ludwig Reissner (58) studied electrical energy engineering at the University of Applied Sciences in Augsburg. At motan he has been working in software design since 1990. His responsibilities include customer applications, re-design and updating of standard sofware as well as employee training. He loves the blues and has a passion for designing and making his own furniture.
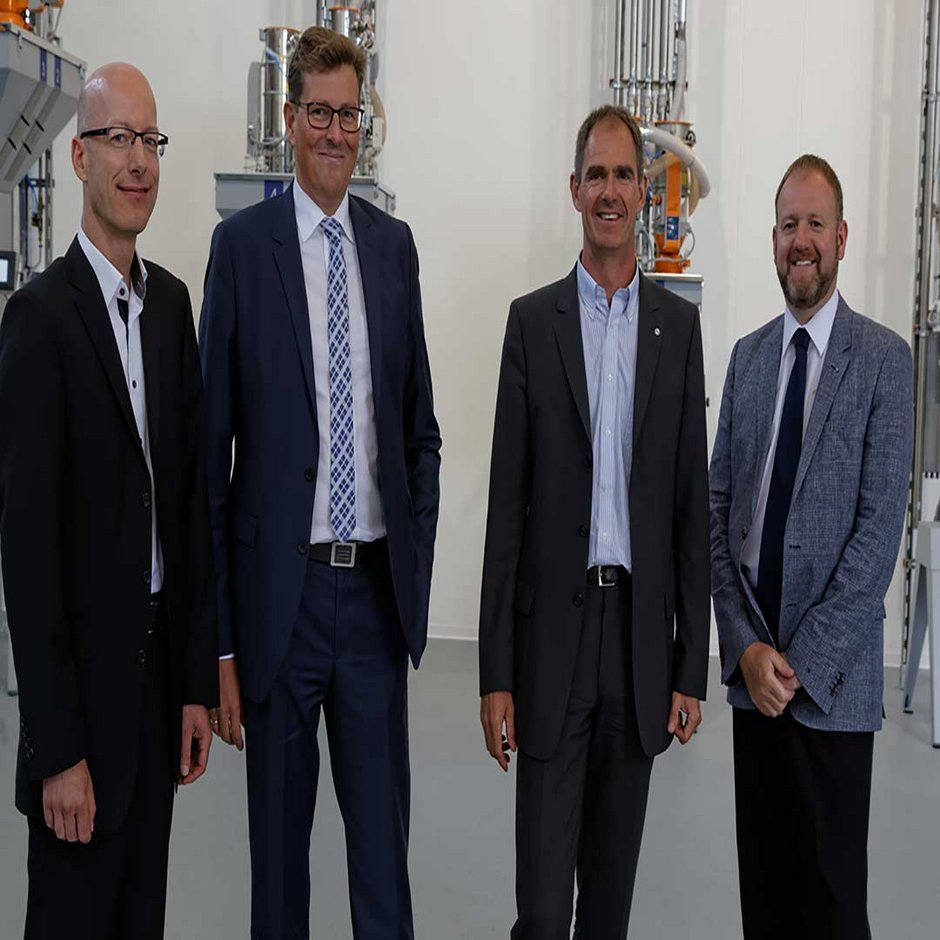
An independent
jury of renowned experts,
who have immense theoretical and practical knowledge in plastics manufacture and processing, decides on the best innovation.
From left to right: Dr.-Ing. Peter Faatz was a Professor for plastics technology and since 2005 has been Head of Process Development for Plastics Technology at the INA factory Schaeffler. Prof. Dr.-Ing. Carsten Manz has been the President of the University of Constance for Technology, Economics and Design since 2014. As the institution director, Prof. Dr. Martin Bastian has been head of the SKZ, Germany’s largest plastics institute since 2006. Karl Miller began at Colortronic in 1987 as a Technical Sales Engineer and today is head of motan-colortronic Ltd. in England.