Allgaier relies on the best of two worlds
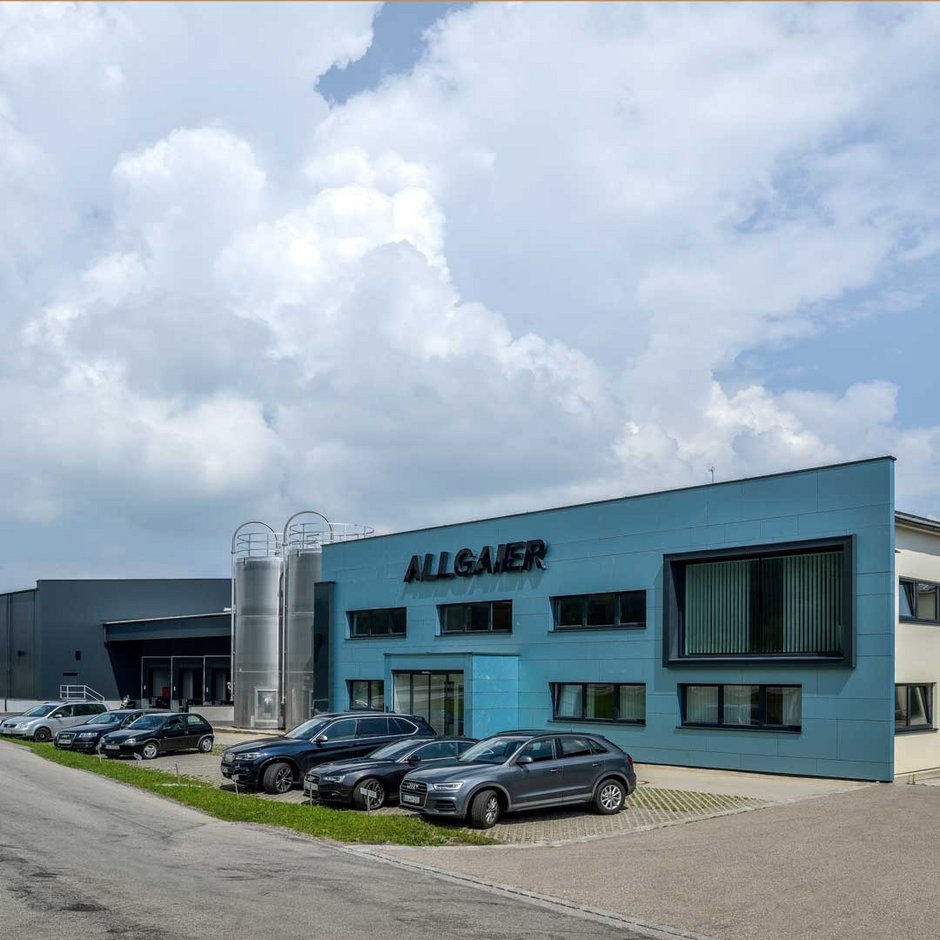
Recently, in 2011, this resulted in an overall concept which has proven itself in the last five years and repeatedly shows how the products and the know-how of two companies can be successfully combined.
So how does one feel with 113 years of company history on ones shoulders?
Thomas Allgaier // Young. But tradition, consistency and a sense of responsibility are very important for us. These are values which characterise our attitude to our customers and employees. Your company was originally a joinery …
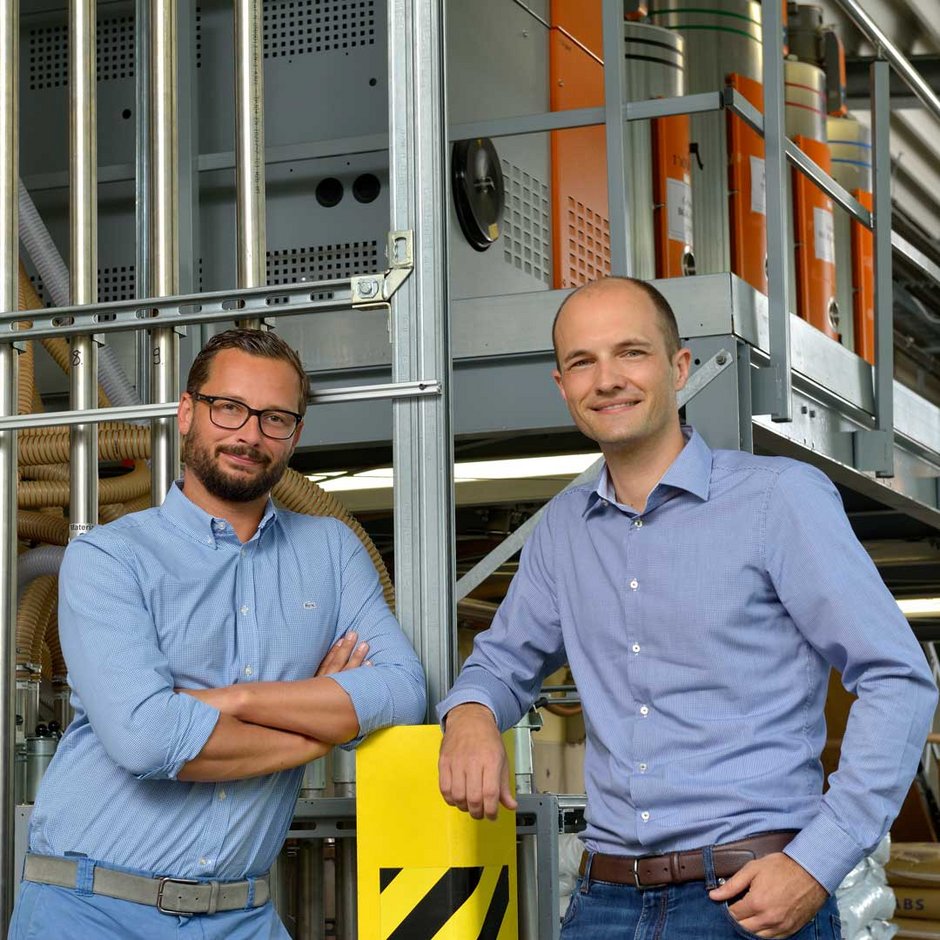
Your company was originally a joinery ...
Christoph Allgaier // Correct, that’s right. And the old building is even still standing today. Immediately after the war, our grandfather also built glider planes from wood and was there-fore ahead of his time.
Thomas Allgaier // Conversion to injection moulding and plas-tics processing only took place at the end of the 1960s. First we processed polyurethane, before we increasingly relied on the TSG process.
If one considers your current range of services, the high degree of specialisation is conspicuous. Is it usual for a company to use so many special processes?
Thomas Allgaier // This is due to the fact that we only became injection moulders via the special processes. We have always oriented ourselves according to the needs of the customer and developed solutions which were the most suitable for his applications.
Christoph Allgaier // … and nothing has changed about that today. In addition to TSG, we use compact, 2-component, sandwich injection moulding, MuCell® and injection stamping. Our in-company tool manufacture also contributes to this pro-duction depth. In this way, we can offer our customers a degree of flexibility which is almost unique for a company of our size.
Thomas Allgaier // Already in 1976, when we built our produc-tion hall, we relied on colortronic products. At that time, disc dosing was more effective and more exact than any manual mixing with powders.
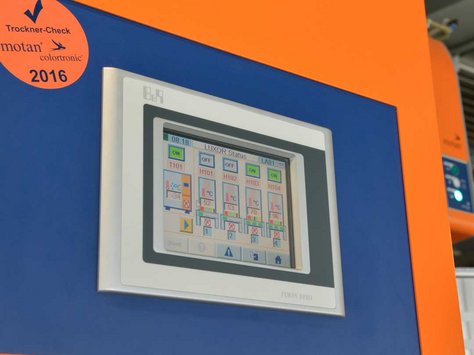
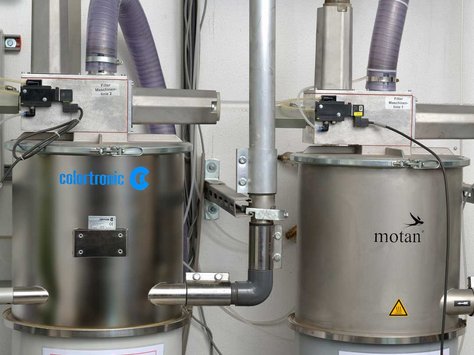
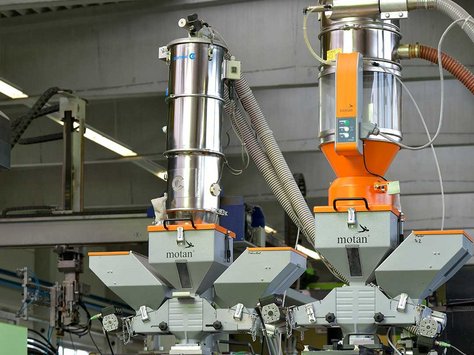
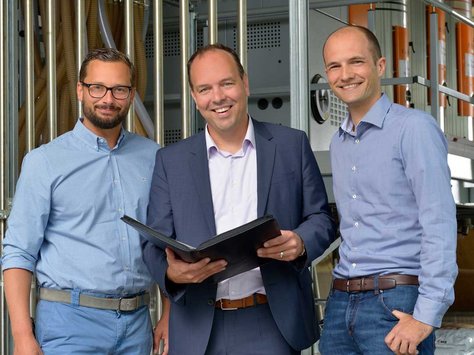
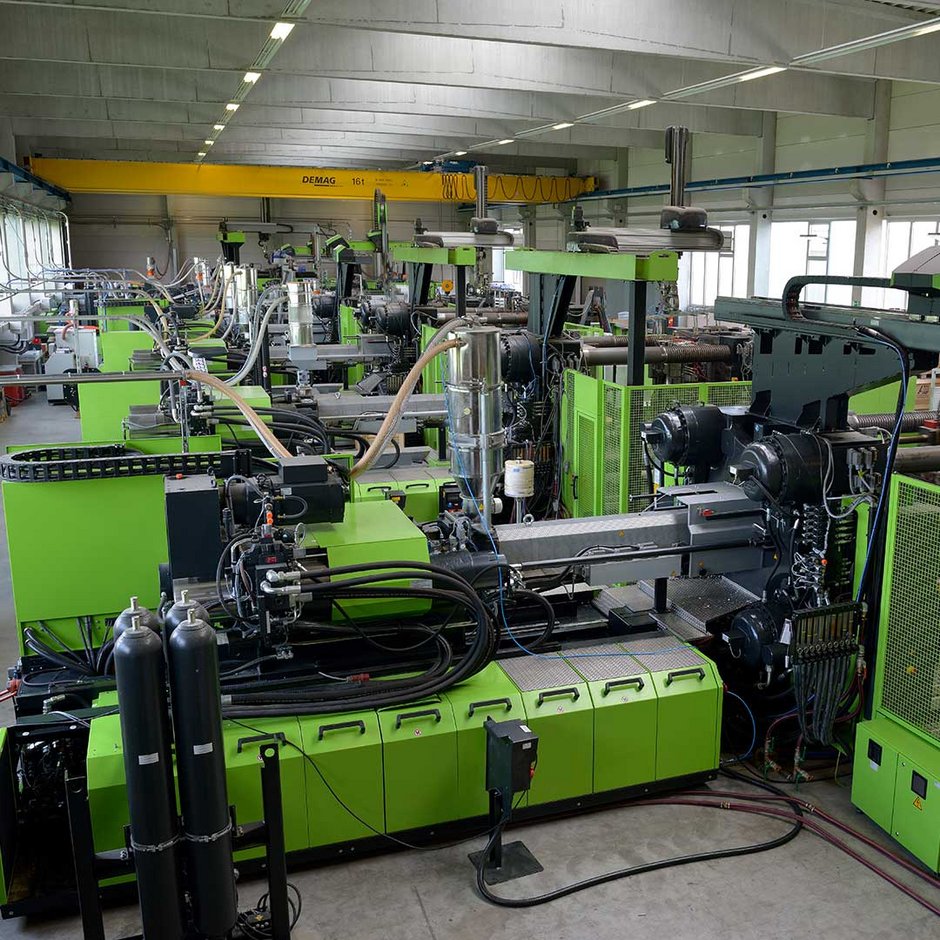
Since then you have grown continually and have also expanded production and logistics. In the course of this, you integrated motan systems with the existing colortronic products. How did this arise?
Christoph Allgaier // The decisive factor was that we no longer used powders. Screw dosing with our current process has handling advantages compared with disc dosing. The area of ap-plication is also larger and dosing accuracy is very good for our applications. In addition, the new VOLUnet MC control offers considerable advantages in terms of user-friendliness and rec-ipe storage.
Thomas Allgaier // In the course of conversion, a complete sys-tem – into which we could integrate our existing colortronic units – was naturally also important for us.
Markus Schinabeck // From 2011, conversion of the central material supply was carried out. This also included central drying with LUXOR A and a central METROnet conveying control. In addition, MINICOLOR V dosing and mixing units, METRO hopper loaders in a glass design and a central coupling table were acquired for the existing units of the Allgaier company.
The 19 injection moulding machines at that time were supplied via three conveying circuits with claw pumps. Over the years, Allgaier purchased more machines, and 22 injection moulding machines (including 12 two-component machines) are current-ly supplied via four conveying circuits. The drying capacity was also expanded with a mobile compact dryer LUXOR S.
Thomas Allgaier // This also shows our specialisation: in all, 18 of our 22 injection moulding machines are designed for spe-cial processes. Especially with regard to the branches for which we work, this is indispensable – white goods, rehabili-tation technology, vehicle equipment and medical technology.
Materials handling with colortronic and conversion to motan – that sounds like successful co-operation.
Markus Schinabeck // In 2009, I took over the sales force for Bavaria for colortronic from my predecessor Mr Stapf, who has served Allgaier for around 25 years. Since then, we have fur-ther improved the already good customer relations of that time because we understand each other well at a professional, technical and personal level.
Thomas Allgaier // For us this is a success story, as we have taken and combined the best of two worlds.