A new era in automotive connectors: advanced central drying and conveying system
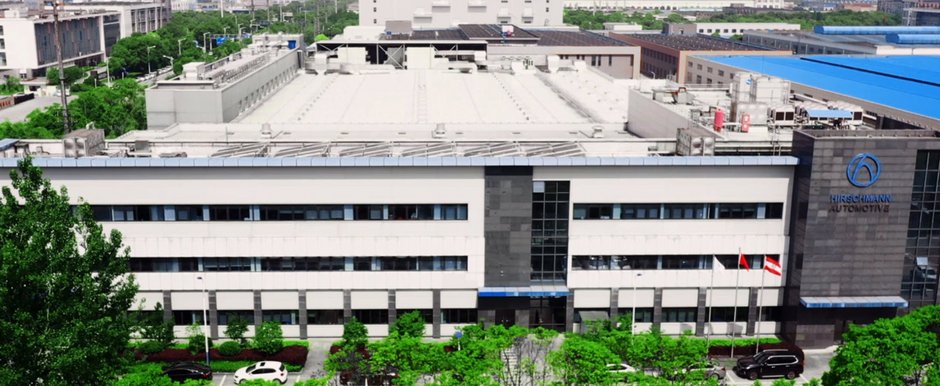
Approaching the gate of Hirschmann, blue buildings and green trees surround a modern factory. Our visit here is to unlock the secrets behind every safe and reliable automotive connector produced by Hirschmann.
An active player in the automotive industry
Headquartered in Austria, Hirschmann is one of the world’s leading automotive suppliers. With six production bases worldwide, it has been instrumental in shaping the developments in the automotive industry for over 60 years.
Hirschmann Automotive established its plant in Nantong, China in 2013 to house its production, R&D and sales. Its customers include a large number of international and local well-known automotive OEM manufacturers. “Now, Hirschmann has 360 employees in Nantong. We have achieved decent growth in recent years on the employee side and in our business as well,” Mr. Arsenic said.
In HV (High Voltage) business, customers expect high flexibility with maximum product safety. “In 2008, we developed the first generation of high-voltage connector product for the electric vehicle market. For more than 10 years, the company has been working rapidly on the further development of its high-voltage portfolio. Now, we are developing and producing the second generation of high-voltage connectors. At the same time, we started investing in the areas of digitization and automation,” Mr. Arsenic added.
For a company like Hirschmann that operates in a very agile business environment, it is important to have flexible suppliers, such as motan, on its side that is able to create customized solutions in the same way Hirschmann customizes solutions for its customers.
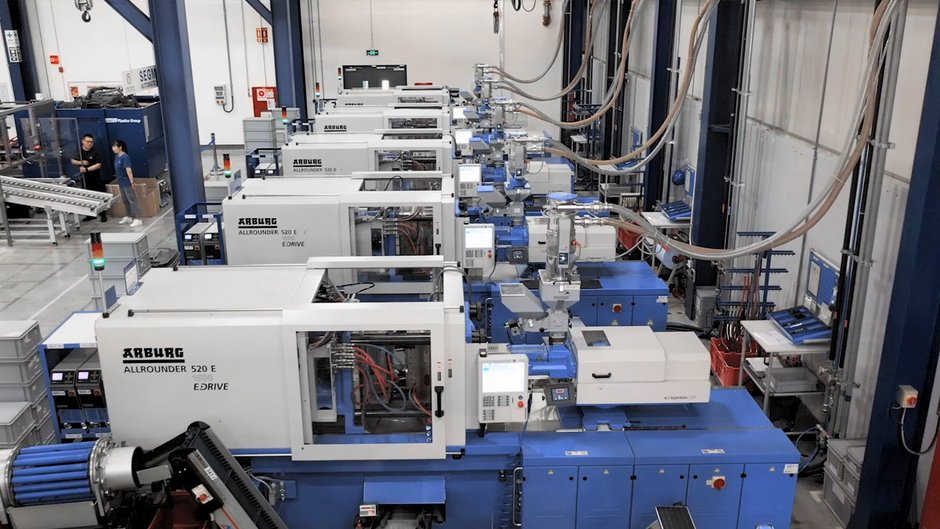
New requirements for drying and conveying systems in safe production
For a traditional vehicle, it needs almost 100 kinds of electronic connectors, which are mainly used in engine management system, safety system, entertainment system, etc. Compared with traditional fuel vehicles, electronically powered vehicles have higher demands for connectors. For example, high-voltage connectors have demanded more from the performance indicators of materials such as shielding, flame retardant, etc. than traditional low-voltage connectors.
“Especially HV (High Voltage) connectors and cables which need new processing technologies that cannot be transferred simply 1:1 from LV (low voltage) connectors and cables”, Mr. Ringel, Technical Supervisor of Hirschmann, said. “For this, a strong and experienced development is mandatory to keep the project timelines.”
For Hirschmann, it is important to ensure the high stability and reliable production process for safety parts like connectors and cables. motan with its broad product portfolio provides many solutions that meet Hirschmann’s requirements.
Globally, Hirschmann has in each plant a motan central drying and conveying system in use with mainly two LUXOR A dry air generators that work in parallel (reliability). Due to each local requirement, different number, and volumes of silos. “They are connected with hundreds of METRO Gs. Finally, all of these are controlled via the CONTROLnet system,” Mr. Ringel said.
There is also a separate “motan room” in Hirschmann Nantong plant, which incorporates a complete set of dosing and mixing, drying and conveying system from GRAVICOLORs to METRO G, LUXOR A and conveying pipes, with its unique industrial blue. The system consists of four LUXOR A dry air generators that provide 50 to 400 liters of dry air for eight LUXOR bin A silos.
“motan’s central drying and conveying system brings process stability, perfectly avoiding the risk of material contamination and reducing the risk of humidity fluctuations. More importantly, we could avoid material errors,”
Mr. Ringel explained. “The piping system is used to convey materials to silos. In the past, we used the coupling table system to allow operators to flexibly choose materials manually. However, this system has a risk that materials may be incorrectly selected during operation and conveyed to the machine for incorrect mixing. motan provides us with RFID coupling tables to avoid wrong materials conveyed to machines and reduce human error.”
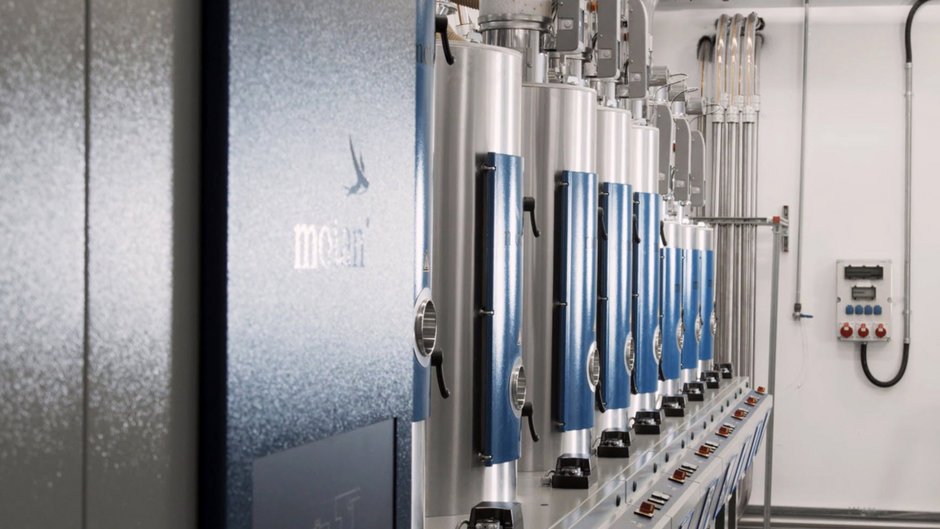
Taking a closer look, the piping in “motan room” is also one of the highlights. Glass bends are used rather than aluminum and stainless-steel pipes. “In the automotive industry, we usually use a lot of plastic materials with higher glass fiber content, which are prone to abrasion and dust. When the materials are conveyed to the injection molding machine, abrasion and dust may cause damage to the machine. Glass bends can solve issues with abrasive dust, offering higher quality and reliability,” said Mr. Ringel.
Today, when sustainability has attracted much attention, energy saving is also an important concern for Hirschmann. “Especially the focus on sustainability like energy saving features (for example the ETA plus® feature) help us to reach our targets.” With ETA plus® technology, it can automatically control the flow and temperature of the dry air while reducing energy consumption. That’s the reason, why this feature is standard on our LUXOR A central drying system. Especially the combination of drying, conveying and mixing in one system simplifies the integration into the Hirschmann-MES-System enormously.”
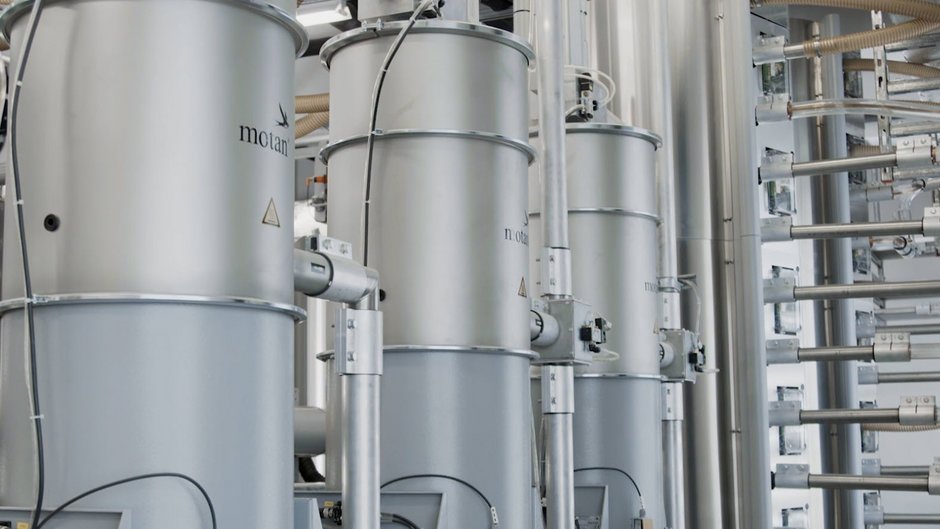
Challenges in smart factory era: system flexibility and efficiency
Shorter lead times, higher productivity, improved quality, and an enhanced degree of flexibility are the hallmarks of the transformation to the Smart Factory, which will take place in all plants over the next years. “A Smart Factory enables Hirschmann Automotive to better meet customer-specific requirements such as seamless traceability through the production processes to the product,” Mr. Arsenic said.
Challenges are everywhere and change over time. “Now we want to improve material changeover in the production of different products. In order to manufacture competitive quality products, we must complete this work quickly and efficiently. motan provided us with the METROLINK material distribution system. In the past, we had to change materials manually. Now the operating personnel only have to select the required materials on the operation panel. The METROLINK material distribution system can automatically distribute materials to different injection molding machines in order to maximize system safety,” introduced Mr. Ringel.
With the continuous expansion of production scale, Hirschmann is facing new challenges. “We have to continuously increase the number of silos and improve further material handling capabilities. However, how many units to be added and how to control them more intelligently is a difficult task. motan supports us a lot, they help us calculate the number of silos, choose the most suitable specification and unit, etc. Especially its CONTROLnet product allows us to control the drying and conveying systems in one monitoring system,” Mr. Ringel said.
“motan is for us a reliable partner with high flexibility and is open to our ideas and improvements, especially in discontinuous material drying with various consumption quantities and flexible material handling, we see potentials for the future. This is, what our customers expect and what we are willed to fulfil,”
Mr. Ringel added.
Words in the end
“Whether standard products or individual customer solutions, our innovative portfolio ensures reliability under the most extreme conditions and in highly demanding areas within a vehicle.” This is Hirschmann’s commitment to the market.
China has become one of the largest connector production bases worldwide. With the steady development of China’s new energy automotive industry, the technical requirements and quality assurance of high-voltage connectors will inevitably become a new concern of Hirschmann users. Meanwhile, a complete drying and conveying system that can ensure the safety and reliability of materials will be a driving force for product development in the new journey.