Projektierungs-Know-how als Wettbewerbsvorteil
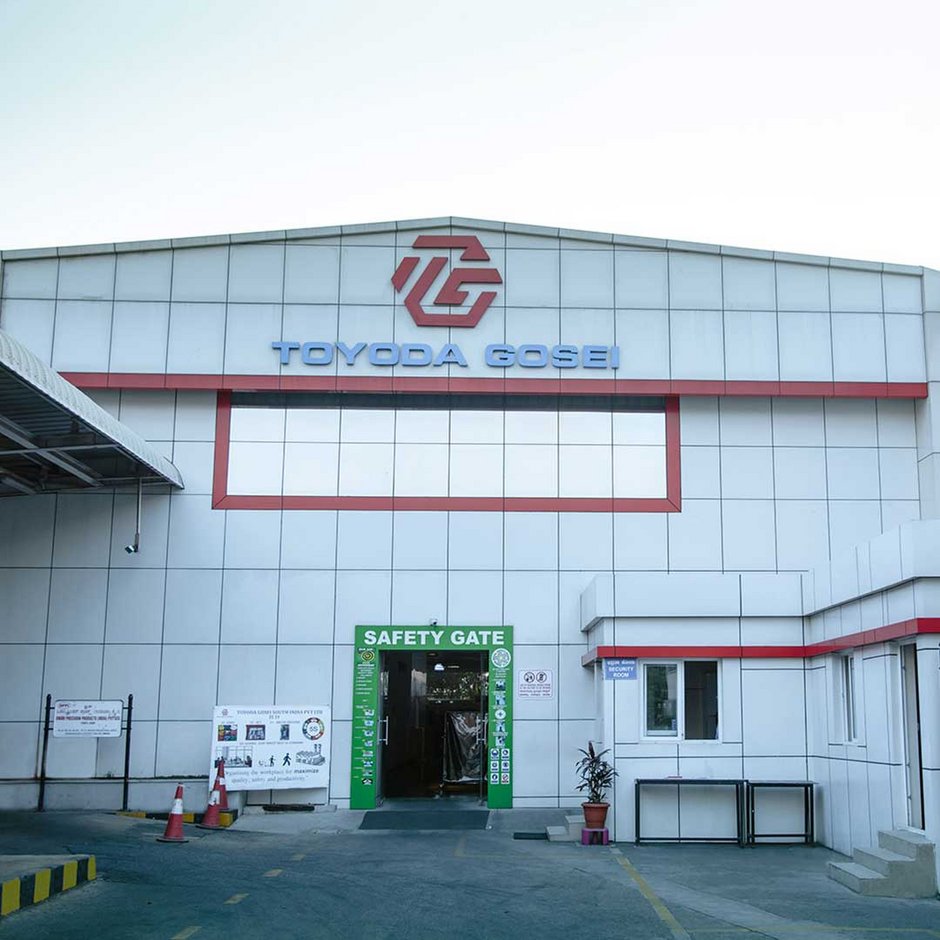
„Heute haben wir uns mit Kunden wie Toyota, Nissan oder Renault in Indien zu einem führenden Unternehmen in der Automobilindustrie entwickelt“, erzählt Vorsitzender und Geschäftsführer Bijay Krishna Shrestha. Inzwischen beschäftigt TGSIN rund 850 Mitarbeiter und erwirtschaftete im vergangenen Jahr einen Umsatz von rund 43 Mio. EUR.
In Bengaluru, im Toyota Techno Park, hat TGSIN eine Produktionsfläche von ca. 23.400 m² zur Verfügung. Spritzgießen, Harzlackierung und Teile für Sicherheitssysteme (Fahrer- und Beifahrerairbags) sind ihre wichtigsten Fertigungsfunktionen. Das Unternehmen besitzt über 25 Spritzgießmaschinen mit Schließkräften zwischen 80 und 3500 Tonnen. Stoßfänger, Kühlergrills, Radkappen, hintere Türverkleidung und Instrumententafeln, Säulenteile, Konsolenmodule und Armlehnen sind in dem Produktprofil enthalten.
Im Zuge einer Produktionserweiterung im Jahr 2014 suchte TGSIN einen Anbieter für eine Trocknungs- und Förderanlage, der einerseits lokal ansässig ist und andererseits technisch hochwertige Lösungen anbietet, die den hohen Qualitätsansprüchen des Unternehmens gerecht werden. Fündig wurde das Unternehmen bei motan-colortronic India.
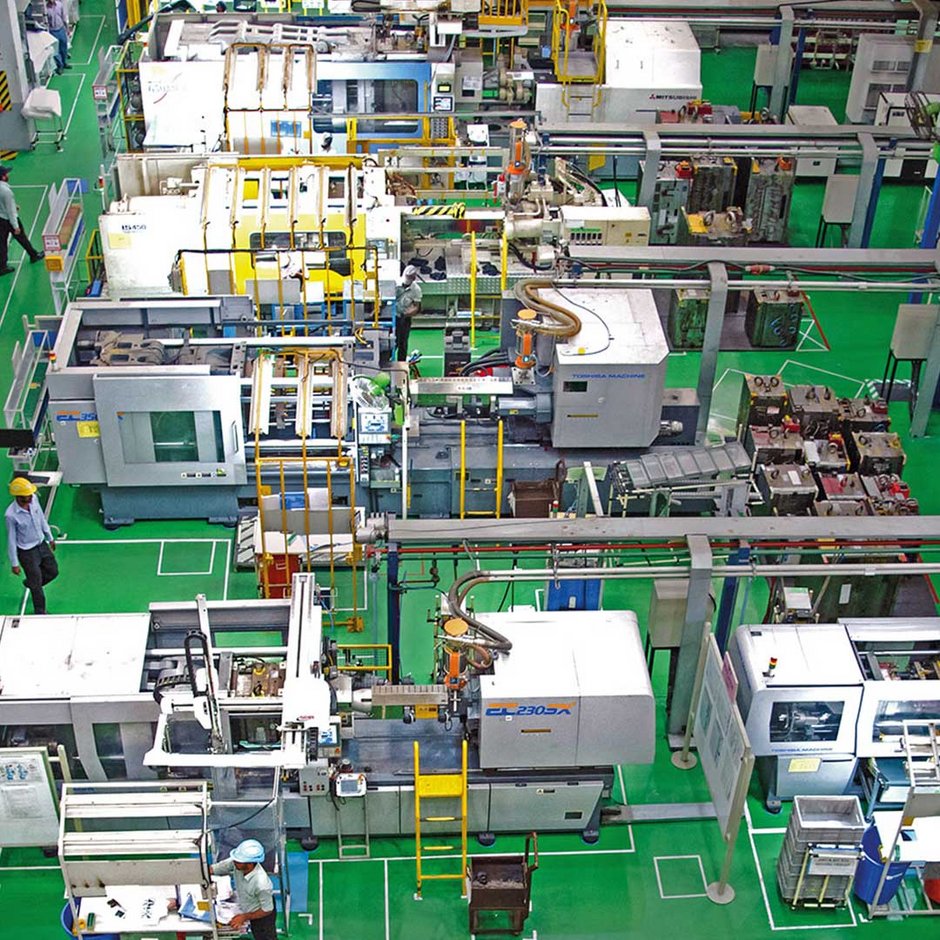
„TGSIN setzte in seiner Produktion auf ein kleinteiliges Zellenprinzip, das heißt jede Verarbeitungsmaschine hat ihre eigene Versorgung, was viele japanische Firmen bevorzugen“, erläutert Verkaufsleiter Anandakumar Ramachandran. „2010 hat das Unternehmen von uns 6 LUXOR HD 250 Warmlufttrockner und 6 METRO HPE 06 Fördergeräte mit dem gleichen Konzept gekauft“, berichtet er über die Anfänge.
Das Zellenprinzip und die damit einhergehende Materialversorgung direkt an der Verarbeitungsmaschine hat aber auch einige Nachteile wie zum Beispiel Lärm, Wärme, Staub, Platzmangel und Granulatreste in unmittelbarem Umfeld der Maschine. „Deshalb haben wir TGSIN für die zweite Erweiterungsphase um neun Spritzgießmaschinen ein zentrales Trocknungs- und Fördersystem vorgeschlagen, das neben der Platzersparnis in der Produktion, Sauberkeit rund um die Spritzgießmaschine sowie insbesondere eine bessere Energieeffizienz aufweist. So konnten wir uns von der Konkurrenz deutlich hervorheben“, erklärt Ramachandran.
Für die neue zentrale Materialversorgung wurde eine Bühne installiert. Beginnend mit der Materialaufgabe sind hier außerdem ein Teil der Förder- sowie der Trocknungsanlage untergebracht. Versorgt werden die Maschinen über 25 Kg und 750 Kg Sackware, deren Materialaufgabestelle sich genau gegenüber der Trocknungsanlage befinden, um lange Wege zu vermeiden.
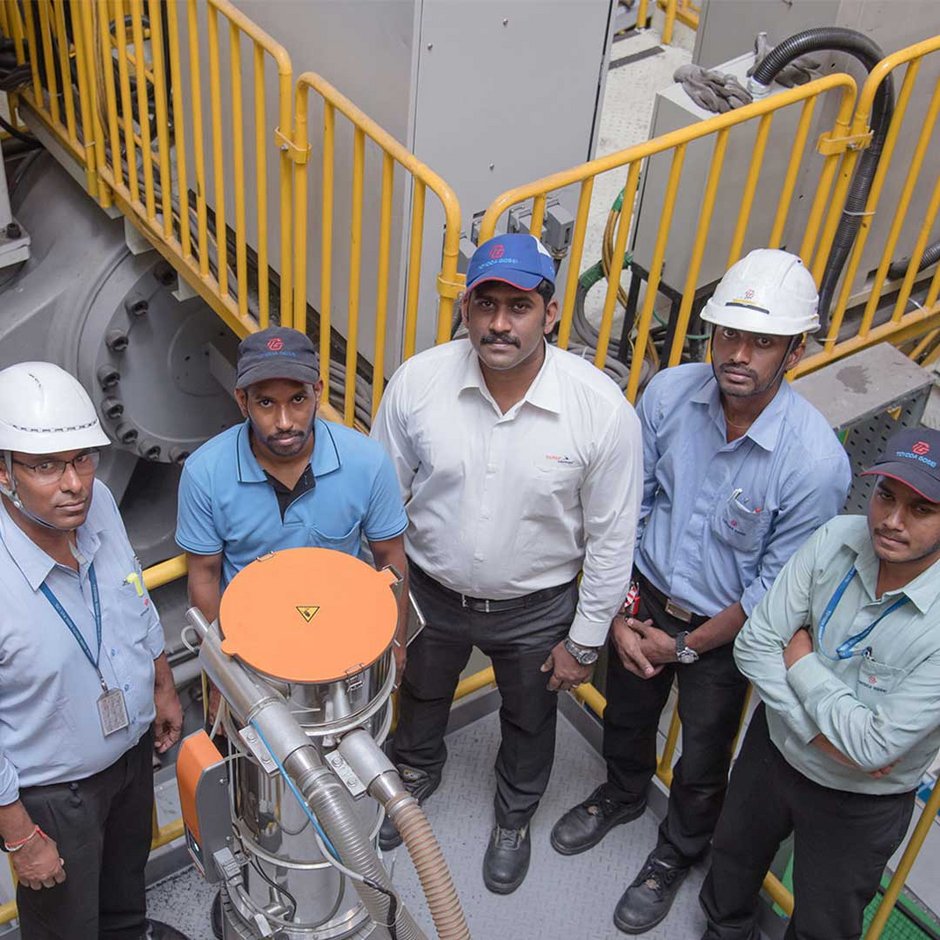
Durch die große Vielfalt an verwendeten Polymeren wurde die zentrale Materialförderung als ein maschinenbezogenes System konzipiert. Das bedeutet, dass jede Spritzgießmaschine ihre eigene Zuleitung hat und die Materialauswahl über eine Kupplungsstation erfolgt. Der manuelle METROCONNECT U Kupplungstisch bringt Flexibilität in der Materialaufgabe. So können mehrere Maschinen an eine Materialleitung angeschlossen werden. Ein weiterer Vorteil eines zentralen Fördersystems ist die Verlagerung der Fördergebläse an einen zentralen Ort. Auf diese Weise ist die Verarbeitungsmaschine und dessen Umgebung frei von Verschmutzung, Hitze und Lärm.
Durch die Umsetzung des Konzeptes einer zentralen Trocknungsanlage anstelle von Einzeltrocknern wurde die Gesamtleistung der Trockner von 353 kW auf 159,8 kW reduziert. Dieses erfolgreiche Ergebnis beruht auf einer ausgeklügelten Kombination von Luftgeneratoren und Trockentrichtern mit unterschiedlichen Litern Fassungsvermögen die zuvor in Versuchen im motan-colortronic India Technikum getestet und optimiert wurden.
„motan-colortronic India bietet Lösungen an, nicht nur Produkte“, fasst Ramachandran zusammen. „Eine unserer Stärken ist außerdem die hohe Projektierungs-Kompetenz, die uns von den Wettbewerbern in Indien unterscheidet“, zeigt er sich selbstbewusst. „Die Produkte, die wir in Indien herstellen sind qualitativ genauso gut, wie die aus Deutschland. Durch eine intensive Suche nach lokalen Lieferanten, die eine gleichbleibend hohe Qualität liefern sowie durch unsere intensiv geschulten Produktionsmitarbeiter, können wir das garantieren.“
Mr. Balamurugan, stellvertretender Geschäftsführer und zuständig für die Maschinenwartung bei TGSIN sagt: „Wir haben uns aufgrund der Qualität und Zuverlässigkeit für motan-colortronic entschieden. Weitere Kriterien waren die technische Kompetenz des Unternehmens, höhere Energieeffizienz und weniger Ausfall. Wobei das nicht ganz richtig ist. Der Ausfall ist aktuell bei null.“ Darüber hinaus hat sich dank der neuen Geräte und Anlagen die Sauberkeit in der Produktion sehr verbessert und auch die Serviceunterstützung durch motan-colortronic ist optimal.