40 Jahre gute Erfahrung und ein faible für anspruchsvolle Spritzgussprojekte
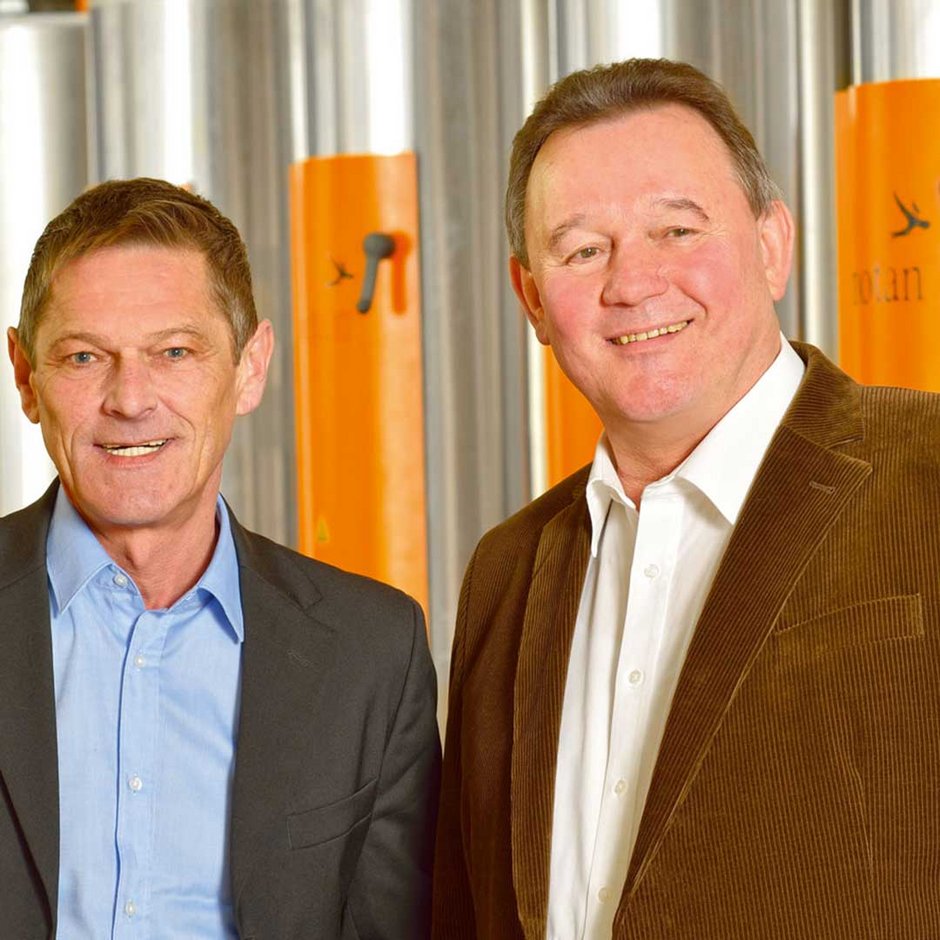
Mayer versteht sich als flexibler, schnell reagierender Systemanbieter, der von der Produktidee bis zur Lieferung einbaufertiger Baugruppen alles liefert. Auf etwa 40 Spritzgießmaschinen mit Schließkräften zwischen 250 und 17.000 kN entstehen vorzugsweise komplexere Teile, vielfach für den Sichtbereich. Ungewöhnlich für ein Unternehmen dieser Größe ist die Leistungsfähigkeit der Oberflächenveredelung: Verschiedene Drucktechnologien und eine moderne Inhouse-Lackieranlage ermöglichen die Lieferung matt oder glänzend lackierter Fahrzeugaußenteile direkt ans Band. Verschiedene Verbindungs- und Montagetechnologien sowie eine eigene Logistik ergänzen das Leistungsspektrum. Verarbeitet wird ein breites Spektrum an Thermoplasten einschließlich TPE, auch in Mehrkomponententechnik.
Das Unternehmen ist in der Zeit seines Bestehens beständig gewachsen. motan-colortronic war von Anfang dabei. Und der nächste Expansionsschritt ist bereits in Planung.
Tier-1- und Tier-2-Zulieferer für Automobilhersteller und deren Zulieferer – und das als mittelständischer Spritzgießer und Formenbauer mit 110 Mitarbeitern auf der schwäbischen Alb? Wie haben Sie das geschafft, Herr Mayer?
Vladimir Mayer // Wir hatten immer schon ein Faible für Produkte und Projekte, die nicht jeder Spritzgießer annimmt – z. B. so vermeintlich einfache Teile wie Fußmatten für den BMW X1 aus TPE. Designelemente, die der Kunde zur Individualisierung des BMW Mini einsetzen kann, erfordern exzellente Oberflächen in vielen Farben. Da hilft es uns, dass wir verschiedene Anlagen zur Oberflächenveredelung inhouse betreiben und eine Vielzahl von Werkstoffen verarbeiten. Das macht uns sehr flexibel und leistungsfähig. Und so kommt man eben auch als kleinerer Mittelständler an anspruchsvolle und attraktive Projekte wie Designelemente für den VW Passat, die partiell matt und teils hochglänzend lackiert werden.
Stichwort Vielzahl von Werkstoffen – ein Blick in die moderne Produktion zeigt, dass Sie beim Materials Handling offenbar ganz auf motan-colortronic setzen. Warum?
Vladimir Mayer // 40 Jahre gute Zusammenarbeit. Da weiß jeder, worauf es bei dem anderen ankommt. Man versteht sich eben. Wir haben seit unserer Unternehmensgründung in den 1970er Jahren mit motan Trocknern sowie Misch- und Dosiergeräten gute Erfahrungen gemacht. Eben auch mit der Beratung. Gerade, wenn es um die Verarbeitung für uns neuer, schwieriger Werkstoffe ging, stand uns motan-colortronic mit guten Tipps und schnellem Service zur Seite. So haben wir mit jedem Wachstumsschritt immer auch die leistungsfähigeren Komponenten von motan-colortronic installiert. 2014 schließlich haben wir gemeinsam ein neues, einheitliches und energiesparendes Konzept einschließlich zentraler Materialversorgung realisiert, um zukünftig noch wirtschaftlicher und flexibler produzieren zu können. Heute trocknen wir rund 70 Prozent unserer Werkstoffe wie PA, PC und ABS vor.
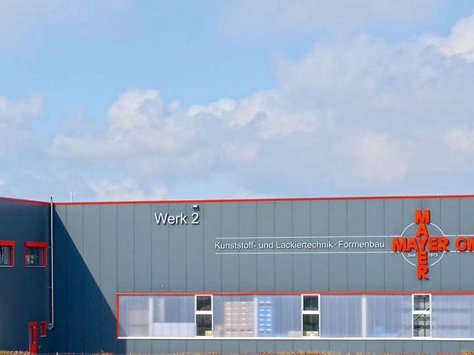
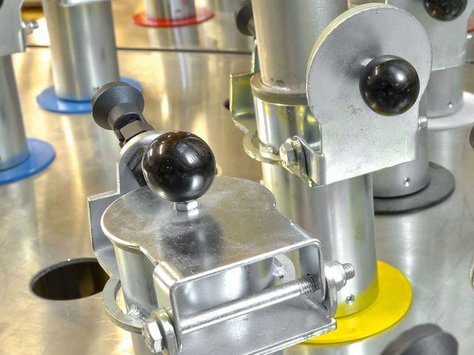
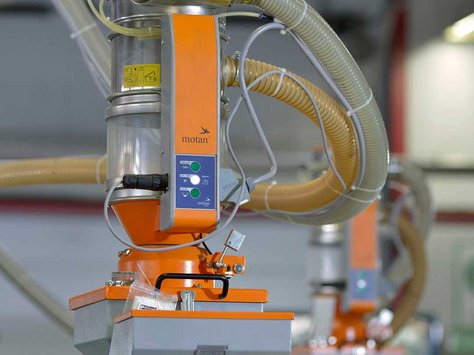
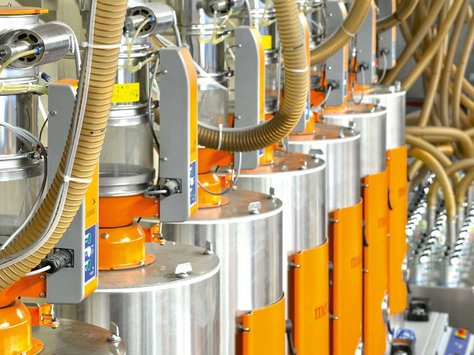
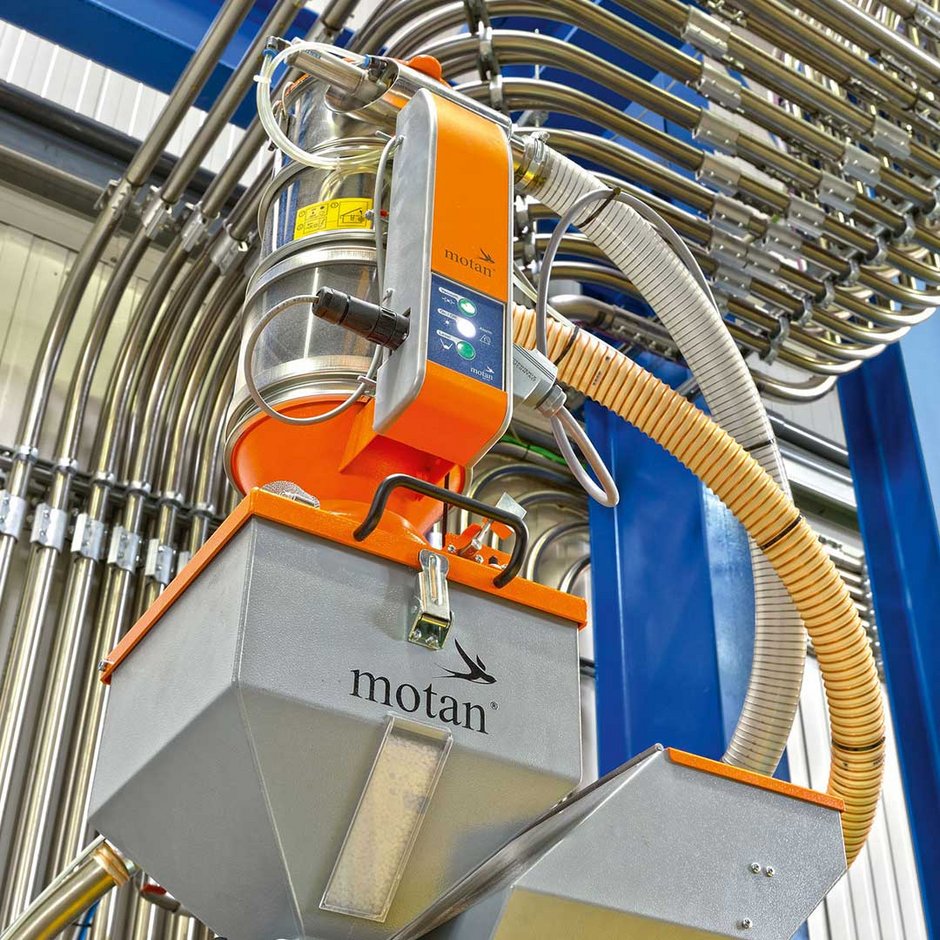
Wie haben Sie Ihre Materialversorgung konzeptionell aufgestellt?
Vladimir Mayer //
Wenn man mal über 40 Spritzgießmaschinen verfügt und immer mehr Werkstoffe verarbeitet, ist es mit einer „gewachsenen“ dezentralen Materialversorgung nicht mehr getan. Dann brauchst du ein durchgängiges Konzept. Allein schon, um den Energieverbrauch bei der Trocknung zu senken. Und das gilt erst recht, wenn du weiter expandierst. Um diesen Schritt zu stemmen, haben wir wiederum Ingo Staib und Anton Küble von motan-colortronic ins Boot geholt und miteinander ein exakt auf unsere Bedürfnisse angepasstes, zukunftsweisendes Konzept entwickelt. Das reicht von der Materiallagerung über die Trocknungs- und Verteilungstechnik bis hin zum automatischen Einschleusen von Recyclingmaterial und der Misch- und Dosiertechnik an den Maschinen.
In all diesen Fragen brauchten wir einfach umfassende Beratungskompetenz, auch bei eigentlich kleineren Themen wieder Auswirkung der Entstaubung auf die für uns so wichtige Spritzqualität. motan-colortronic hat sich dabei als echter Partner erwiesen und nichts versprochen, was am Schluss nicht gehalten wurde. Planungen und Leistungen wurden exakt eingehalten. Um eine Zahl zu nennen: Heute verbrauchen wir nur rund 40 Prozent der früher benötigten Energiemenge. Wir sparen 60 Prozent. Das spricht für sich. Und das hilft uns auch im Wettbewerb.
Ingo Staib // Die Umstellung auf die zentrale Materialversorgung entlastet außerdem das Personal beim Materialtransport. Teurer Lagerplatz in den Hallen muss auch nicht mehr vorgehalten werden und man vermeidet Fehler beim Beschicken. Obendrein ist es in der Produktion sehr viel sauberer.
Würden Sie mit Ihrer langjährigen Betriebserfahrung aus heutiger Sicht etwas anders machen?
Vladimir Mayer // Grundsätzlich nicht. Wir sind gerade dabei, auf einem Nachbargrundstück unsere Produktion mit Spritzgießmaschinen bis 2000 Tonnen und Mehrkomponententechnik zu erweitern. Auch dabei wird uns motan-colortronic begleiten. Schließlich hilft uns motan-Technik auch, Kunden von der Klasse unserer Produktion zu überzeugen. Bei vielen Rundgängen führen wir unsere Besucher am Schluss an der Trockneranlage vorbei und demonstrieren ihnen direkt an der Maschine, was wir für die Qualität ihrer Produkte tun. Und das wirkt